Plasma-activated vapor deposition (PAVD) is an advanced thin-film coating technique that utilizes plasma to enhance the deposition process. It involves the activation of precursor gases or vapors into a highly reactive state using plasma, which then facilitates the deposition of thin films onto substrates. This method is widely used in industries such as semiconductors, optics, and surface engineering due to its ability to produce high-quality, uniform coatings with precise control over film properties. PAVD combines the principles of chemical vapor deposition (CVD) and plasma-enhanced chemical vapor deposition (PECVD), offering improved deposition rates, better adhesion, and enhanced film properties compared to traditional methods.
Key Points Explained:
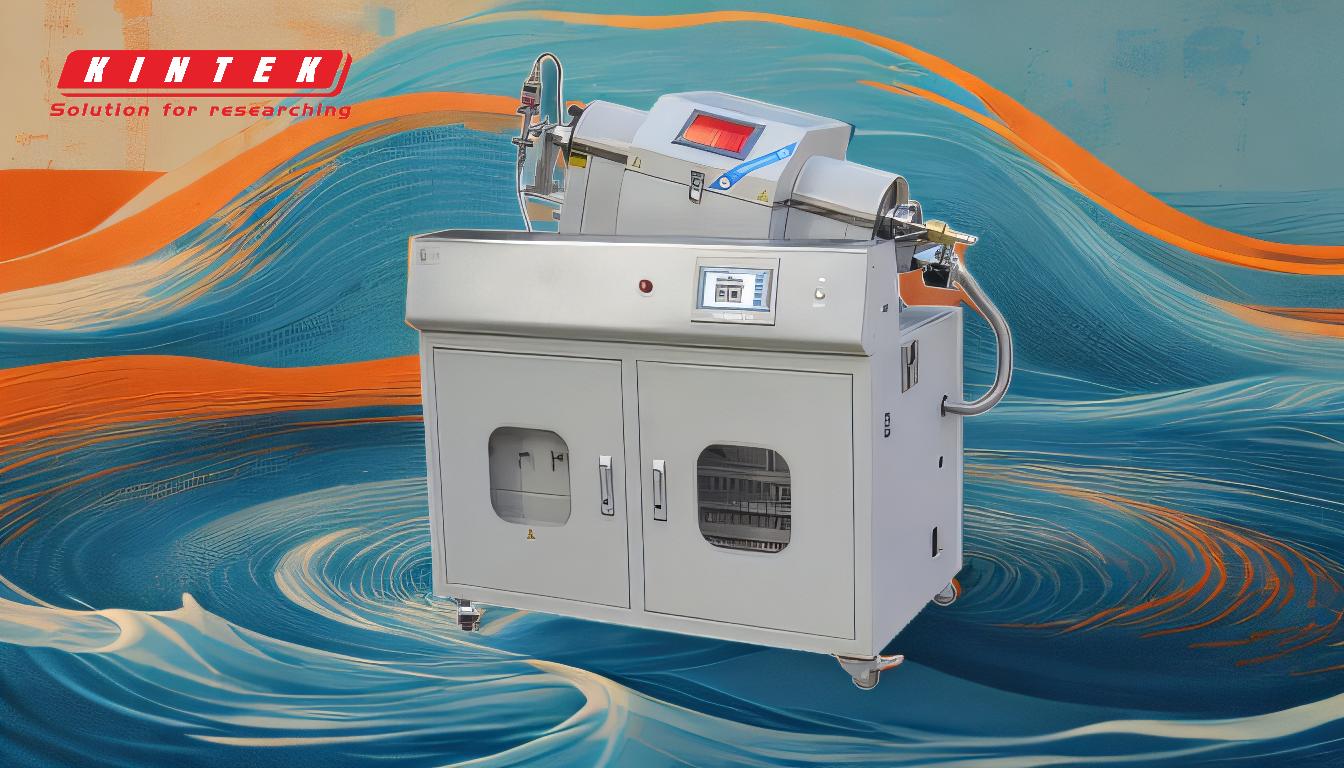
-
Definition and Mechanism of PAVD:
- Plasma-activated vapor deposition is a hybrid process that integrates plasma activation with vapor deposition techniques.
- In this process, precursor gases or vapors are ionized or excited into a plasma state using an electrical discharge or other energy sources.
- The plasma-activated species are highly reactive and facilitate the formation of thin films on the substrate surface.
-
Comparison with Traditional Vapor Deposition:
- Unlike conventional chemical vapor deposition (CVD), which relies solely on thermal energy to activate precursors, PAVD uses plasma to achieve activation at lower temperatures.
- This allows for deposition on temperature-sensitive substrates and reduces energy consumption.
- PAVD also offers better control over film properties, such as density, uniformity, and adhesion, compared to traditional methods.
-
Types of Plasma Used in PAVD:
- Low-Pressure Plasma: Operates under vacuum conditions, enabling precise control over the deposition environment and minimizing contamination.
- Atmospheric Pressure Plasma: Suitable for large-scale industrial applications, as it does not require vacuum systems.
- Radio Frequency (RF) Plasma: Commonly used for activating precursor gases, providing high-energy species for efficient deposition.
-
Applications of PAVD:
- Semiconductor Industry: Used for depositing dielectric layers, conductive films, and passivation layers in microelectronics.
- Optical Coatings: Enables the production of anti-reflective, scratch-resistant, and high-transparency coatings for lenses and displays.
- Surface Engineering: Enhances the wear resistance, corrosion resistance, and biocompatibility of materials used in medical devices and aerospace components.
-
Advantages of PAVD:
- Enhanced Film Quality: Plasma activation results in denser, more uniform films with improved mechanical and optical properties.
- Lower Processing Temperatures: Suitable for temperature-sensitive materials, expanding the range of applicable substrates.
- Versatility: Can be adapted for various precursor gases and deposition conditions, making it suitable for diverse applications.
-
Challenges and Limitations:
- Complexity: The process requires specialized equipment and precise control over plasma parameters, making it more complex than traditional methods.
- Cost: Initial setup and operational costs can be higher due to the need for plasma generation systems and vacuum equipment.
- Scalability: While atmospheric pressure PAVD is scalable, low-pressure systems may face challenges in large-scale industrial applications.
-
Future Trends in PAVD:
- Integration with Additive Manufacturing: Combining PAVD with 3D printing technologies to create functional coatings on complex geometries.
- Development of Green Precursors: Research into environmentally friendly precursor gases to reduce the environmental impact of the process.
- Advancements in Plasma Sources: Innovations in plasma generation, such as pulsed plasma and microwave plasma, to improve efficiency and film quality.
In summary, plasma-activated vapor deposition is a versatile and advanced coating technique that leverages plasma activation to achieve superior film properties. Its applications span multiple industries, and ongoing research continues to expand its capabilities and address existing challenges.
Summary Table:
Aspect | Details |
---|---|
Definition | Hybrid process combining plasma activation with vapor deposition techniques. |
Key Mechanism | Precursor gases are ionized into plasma for highly reactive thin-film formation. |
Applications | Semiconductors, optical coatings, surface engineering. |
Advantages | Enhanced film quality, lower processing temperatures, versatility. |
Challenges | High complexity, cost, and scalability limitations. |
Future Trends | Integration with 3D printing, green precursors, advanced plasma sources. |
Interested in how plasma-activated vapor deposition can benefit your industry? Contact our experts today to learn more!