A porcelain furnace is a specialized piece of equipment used primarily in dental laboratories and clinics for the fabrication and customization of dental restorations such as crowns, bridges, veneers, and inlays/onlays. It operates by heating ceramic materials to high temperatures, allowing them to sinter and achieve the desired strength, durability, and aesthetic properties. The furnace is designed to provide precise temperature control, ensuring consistent results. It plays a critical role in modern dentistry, enabling the creation of highly accurate and natural-looking dental prosthetics. Porcelain furnaces are available in various types, including manual, semi-automatic, and fully automatic models, catering to different workflow needs.
Key Points Explained:
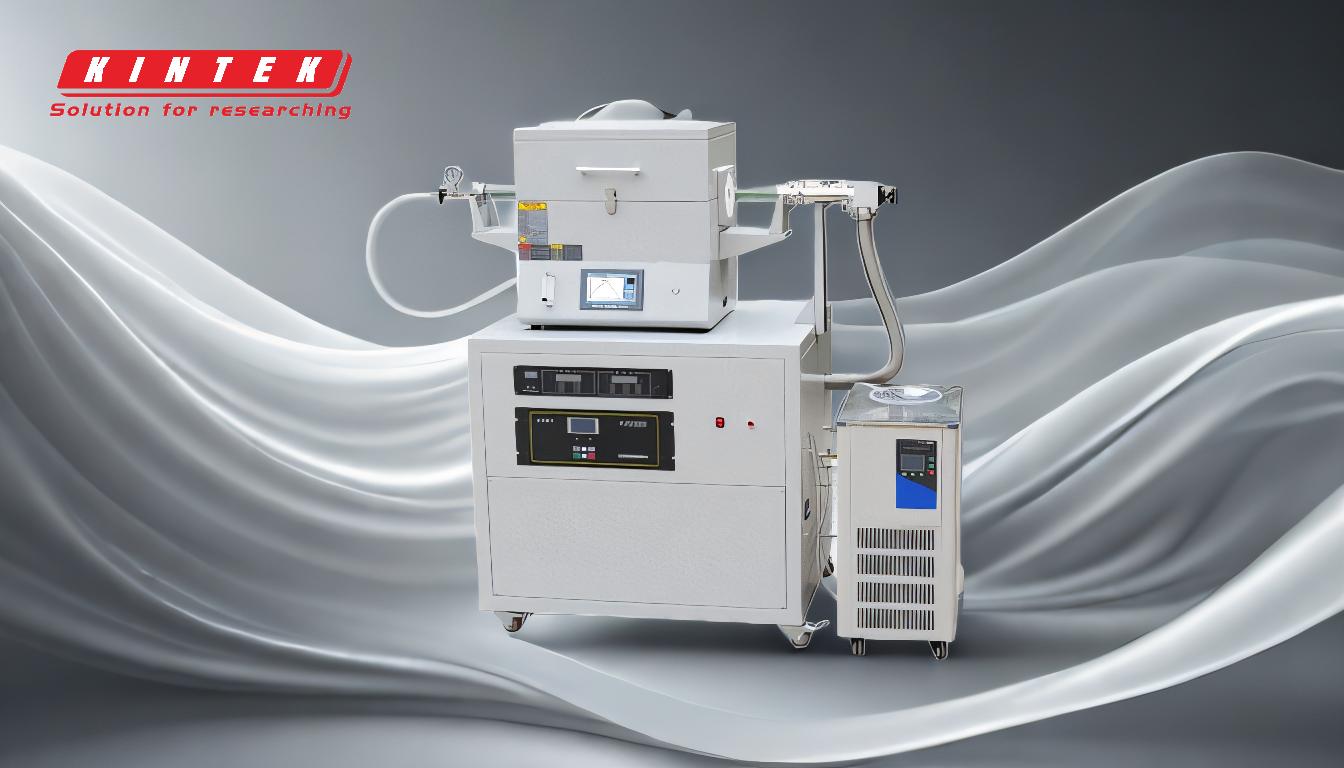
-
Definition and Purpose of a Porcelain Furnace
A porcelain furnace is a device used to process dental ceramics, transforming them into durable and aesthetically pleasing dental restorations. It is essential for sintering porcelain materials, which involves heating them to high temperatures to bond the particles together, resulting in a strong and cohesive structure. This process is crucial for creating restorations that mimic the natural appearance of teeth. -
How a Porcelain Furnace Works
- Heating Mechanism: The furnace uses electric heating elements to achieve temperatures ranging from 600°C to 1,100°C, depending on the material being processed.
- Temperature Control: Advanced models feature precise temperature control systems, including programmable settings and sensors, to ensure consistent results.
- Vacuum or Atmospheric Operation: Some furnaces operate under a vacuum to eliminate air bubbles and improve the density of the ceramic, while others work in a standard atmospheric environment.
-
Types of Porcelain Furnaces
- Manual Furnaces: Require the operator to manually set and monitor the temperature and firing cycles. These are typically more affordable but demand greater skill and attention.
- Semi-Automatic Furnaces: Offer pre-programmed firing cycles but still require some manual input. They strike a balance between cost and convenience.
- Fully Automatic Furnaces: Equipped with advanced software and sensors, these furnaces automate the entire firing process, reducing the risk of human error and improving efficiency.
-
Applications in Dentistry
- Crowns and Bridges: Used to create durable and natural-looking replacements for damaged or missing teeth.
- Veneers: Thin ceramic shells bonded to the front of teeth to improve their appearance.
- Inlays and Onlays: Custom-made restorations used to repair moderately damaged teeth.
- Custom Shading and Staining: Allows for precise color matching to blend seamlessly with the patient's natural teeth.
-
Advantages of Using a Porcelain Furnace
- High Precision: Ensures accurate and consistent results, critical for dental restorations.
- Aesthetic Quality: Produces restorations that closely resemble natural teeth in color, translucency, and texture.
- Durability: The sintering process enhances the strength and longevity of ceramic materials.
- Versatility: Can process a wide range of dental ceramics, including zirconia, lithium disilicate, and feldspathic porcelain.
-
Key Features to Consider When Purchasing
- Temperature Range: Ensure the furnace can reach the required temperatures for the materials you use.
- Firing Chamber Size: Choose a size that accommodates your typical workload.
- Programmability: Look for models with customizable firing programs for different materials and applications.
- Ease of Use: Consider the level of automation and user interface design.
- Maintenance Requirements: Opt for furnaces with easy-to-clean components and reliable after-sales support.
-
Maintenance and Care
- Regular cleaning of the firing chamber and heating elements to prevent contamination.
- Calibration checks to ensure accurate temperature control.
- Replacement of worn-out components, such as thermocouples, to maintain performance.
-
Future Trends in Porcelain Furnace Technology
- Integration with CAD/CAM Systems: Enhanced compatibility with digital dentistry workflows.
- Energy Efficiency: Development of furnaces that consume less power while maintaining performance.
- Smart Features: Incorporation of IoT capabilities for remote monitoring and diagnostics.
In summary, a porcelain furnace is an indispensable tool in modern dentistry, enabling the creation of high-quality dental restorations. Its precision, versatility, and ability to produce aesthetically pleasing results make it a cornerstone of dental laboratory and clinical workflows. When selecting a furnace, consider factors such as temperature range, programmability, and ease of use to ensure it meets your specific needs.
Summary Table:
Key Aspect | Details |
---|---|
Purpose | Processes dental ceramics for crowns, bridges, veneers, and inlays/onlays. |
Temperature Range | 600°C to 1,100°C, depending on material. |
Types | Manual, semi-automatic, fully automatic. |
Applications | Crowns, bridges, veneers, inlays/onlays, custom shading. |
Advantages | High precision, aesthetic quality, durability, versatility. |
Key Features to Consider | Temperature range, firing chamber size, programmability, ease of use. |
Maintenance | Regular cleaning, calibration, and component replacement. |
Future Trends | CAD/CAM integration, energy efficiency, IoT capabilities. |
Ready to enhance your dental lab's capabilities? Contact us today to find the perfect porcelain furnace for your needs!