Pulsed DC sputtering is an advanced form of physical vapor deposition (PVD) that enhances the traditional DC sputtering process by introducing a pulsed power supply. This method is particularly useful for depositing insulating materials, as it helps mitigate issues like arcing and target poisoning. The process involves applying a pulsed DC voltage to the target material, which alternates between high and low voltage states, allowing for better control over the deposition process and improved film quality.
Key Points Explained:
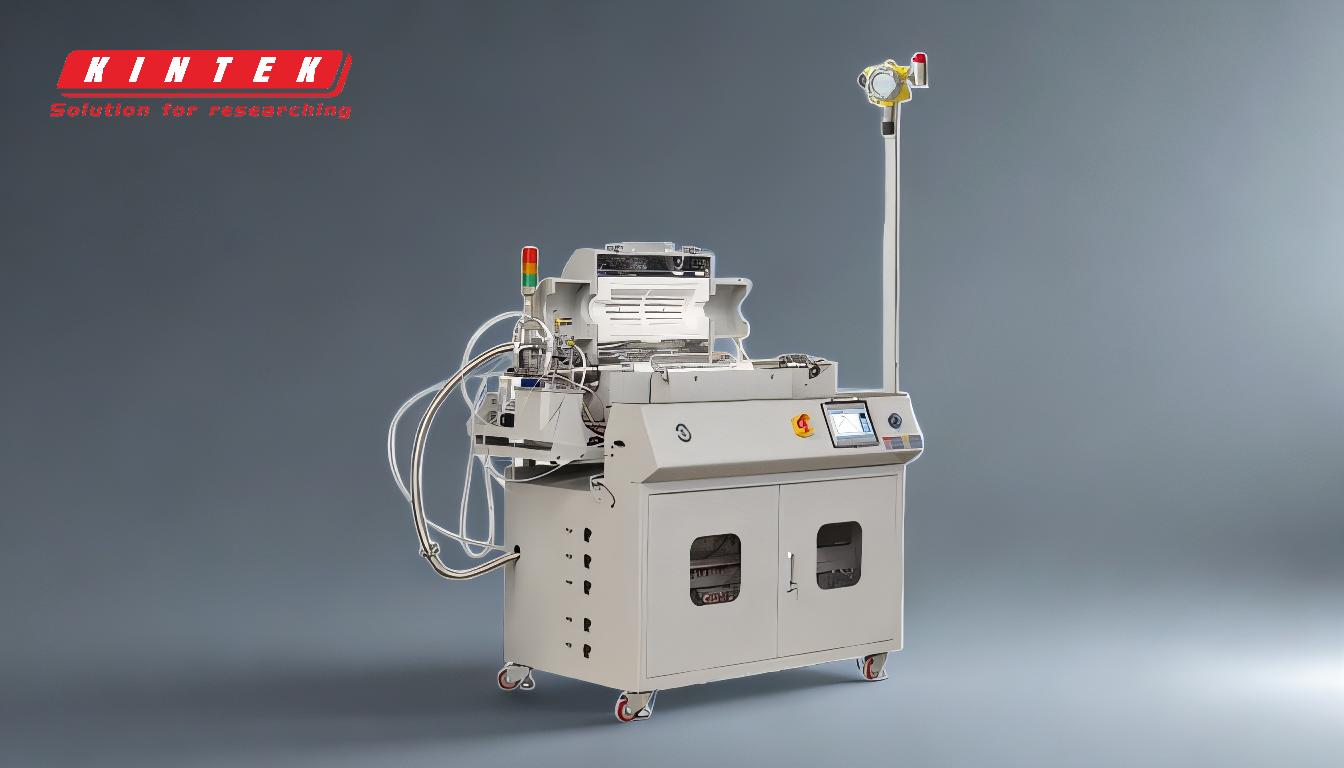
-
Basic Principle of DC Sputtering:
- In traditional DC sputtering, a DC electrical current, typically in the -2 to -5 kV range, is applied to the target coating material, which acts as the cathode. A positive charge is applied to the substrate, making it the anode. This setup creates a plasma environment where ions bombard the target, causing atoms to be ejected and deposited onto the substrate.
-
Challenges with Traditional DC Sputtering:
- Traditional DC sputtering faces challenges when dealing with insulating materials. These materials can accumulate charge on their surface, leading to arcing and target poisoning, which degrade the quality of the deposited film.
-
Introduction of Pulsed DC Sputtering:
- Pulsed DC sputtering addresses these challenges by using a pulsed power supply. The voltage applied to the target alternates between high and low states, allowing any accumulated charge to dissipate during the low-voltage phase. This reduces arcing and target poisoning, making it suitable for depositing insulating materials.
-
Advantages of Pulsed DC Sputtering:
- Reduced Arcing: The pulsed nature of the power supply helps in reducing arcing, which can otherwise damage the target and the substrate.
- Improved Film Quality: By mitigating target poisoning and arcing, pulsed DC sputtering results in smoother and more uniform films.
- Versatility: This method is particularly advantageous for depositing insulating materials, which are challenging to handle with traditional DC sputtering.
-
Mathematical Modeling:
- The sputtering rate in DC magnetron sputtering can be calculated using the formula:
[
R_{\text{sputter}} = \left(\frac{\Phi}{2}\right) \times \left(\frac{n}{N_A}\right) \times \left(\frac{A}{d}\right) \times \left(\frac{v}{1 + \frac{v^2}{v_c^2}}\right)
]
where:
- (\Phi) is the ion flux density,
- (n) is the number of target atoms per unit volume,
- (N_A) is Avogadro's number,
- (A) is the atomic weight of the target material,
- (d) is the distance between the target and substrate,
- (v) is the average velocity of the sputtered atoms,
- (v_c) is the critical velocity.
- The sputtering rate in DC magnetron sputtering can be calculated using the formula:
[
R_{\text{sputter}} = \left(\frac{\Phi}{2}\right) \times \left(\frac{n}{N_A}\right) \times \left(\frac{A}{d}\right) \times \left(\frac{v}{1 + \frac{v^2}{v_c^2}}\right)
]
where:
-
Process Details:
- Transformation of Material: Sputter coating works by transforming a solid material into a fine spray of microscopic particles, which appear as a 'gas' to the human eye. This process requires specialized chilling to manage the heat generated.
- Vapor Deposition: In PVD by sputtering, the material to be deposited as a film is converted into vapor by bombarding the source material with high-energy particles or ions.
-
Applications:
- Pulsed DC sputtering is widely used in the semiconductor industry, optical coatings, and the production of thin-film solar cells. Its ability to deposit high-quality insulating films makes it indispensable in these fields.
By understanding these key points, one can appreciate the technological advancements that pulsed DC sputtering brings to the field of thin-film deposition, particularly in handling challenging materials and improving film quality.
Summary Table:
Aspect | Details |
---|---|
Basic Principle | Uses DC electrical current to create plasma, ejecting atoms for deposition. |
Challenges Overcome | Reduces arcing and target poisoning in insulating materials. |
Advantages | Improved film quality, reduced arcing, and versatile material handling. |
Applications | Semiconductors, optical coatings, and thin-film solar cells. |
Ready to enhance your thin-film deposition process? Contact us today for expert guidance!