PVD (Physical Vapor Deposition) and CVD (Chemical Vapor Deposition) are two advanced coating technologies used to deposit thin films onto substrates, but they differ significantly in their processes, materials, and applications. PVD involves the physical vaporization of solid materials, which then deposit onto the substrate in a vacuum at relatively lower temperatures (250°C~450°C). In contrast, CVD relies on chemical reactions between gaseous materials and the substrate, occurring at higher temperatures (450°C to 1050°C). PVD is widely used in decorative and functional applications, such as jewelry, hardware, and automotive parts, due to its durability and eco-friendliness. CVD, on the other hand, is preferred for applications requiring dense, uniform coatings, such as in semiconductors and high-performance ceramics. Both methods have unique advantages, and the choice depends on the specific requirements of the application.
Key Points Explained:
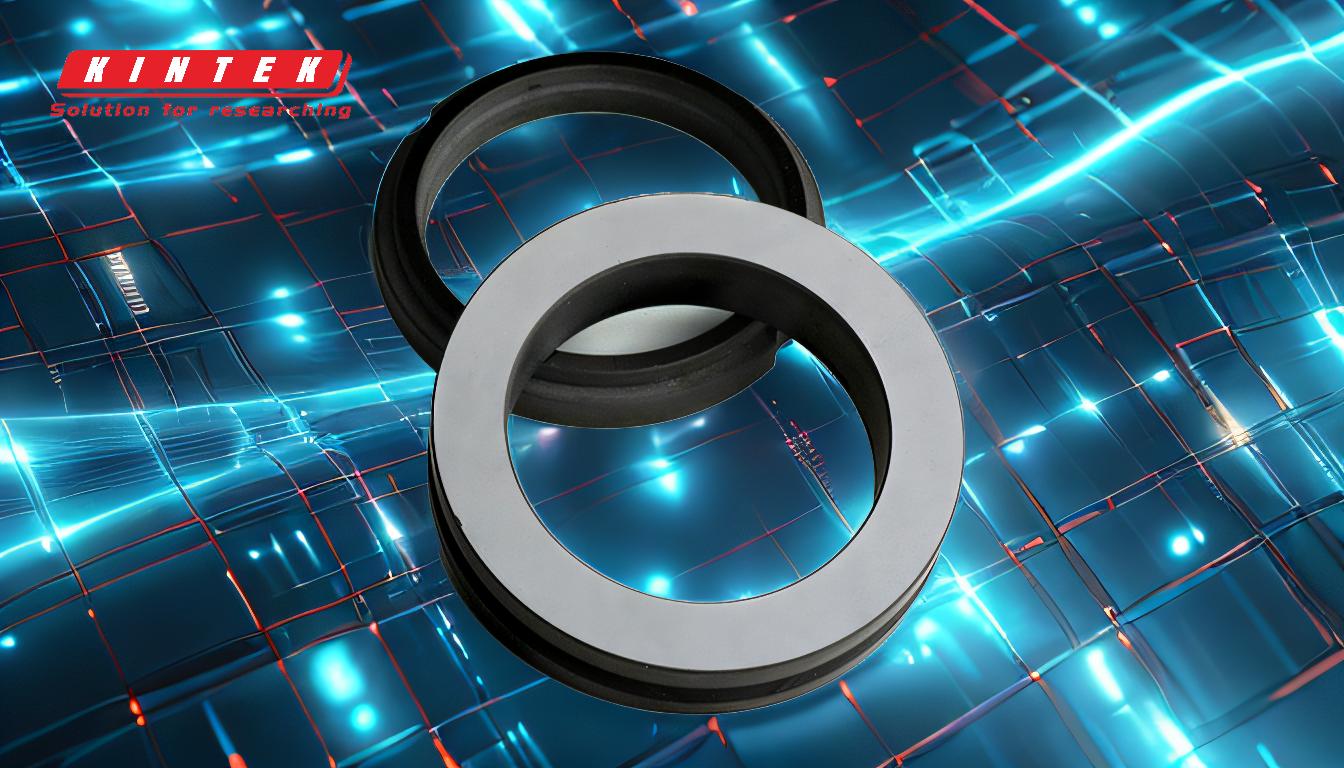
-
Working Mechanisms:
- PVD: Involves the physical vaporization of solid materials, which are then deposited onto the substrate in a vacuum. This process is primarily driven by physical forces.
- CVD: Relies on chemical reactions between gaseous materials and the substrate. The gaseous precursors react on the substrate surface to form the coating.
-
Operating Temperatures:
- PVD: Typically operates at lower temperatures, ranging from 250°C to 450°C. This makes it suitable for substrates that cannot withstand high temperatures.
- CVD: Requires higher temperatures, ranging from 450°C to 1050°C, which can limit its use to substrates that can tolerate such conditions.
-
Coating Substance Nature:
- PVD: Uses solid materials, including metals, alloys, and ceramics. The process allows for a wide range of material deposition.
- CVD: Utilizes gaseous materials, typically limited to ceramics and polymers. The chemical reactions enable the formation of highly uniform and dense coatings.
-
Coating Coverage Area:
- PVD: Provides excellent coverage on complex geometries due to the line-of-sight deposition process. However, it may require rotation or movement of the substrate to ensure uniform coverage.
- CVD: Offers superior conformal coverage, even on intricate shapes, due to the gas-phase reactions that occur uniformly across the substrate surface.
-
Film Thickness and Smoothness:
- PVD: Generally produces thinner films with a smoother surface finish. The coatings are less dense but faster to apply.
- CVD: Results in thicker, denser, and more uniform films. The process takes longer but yields coatings with superior mechanical and chemical properties.
-
Applications:
- PVD: Widely used in decorative and functional applications, such as jewelry, door and window hardware, automotive parts (e.g., wheels, pistons), surgical tools, and drill bits. It is also a greener alternative to chrome plating, enhancing product lifespan by up to ten times.
- CVD: Preferred for high-performance applications, including semiconductor manufacturing, high-temperature ceramics, and protective coatings for tools and components exposed to extreme conditions.
-
Environmental and Economic Considerations:
- PVD: Considered more environmentally friendly as it does not produce toxic substances. It is also cost-effective for mass production, especially in the hardware and decorative industries.
- CVD: While it may involve higher operational costs due to the need for high temperatures and specialized equipment, it provides superior coating quality, making it indispensable in high-tech industries.
In summary, the choice between PVD and CVD depends on the specific requirements of the application, including the desired coating properties, substrate material, and operational constraints. Both technologies offer unique advantages, making them essential tools in modern manufacturing and materials science.
Summary Table:
Aspect | PVD (Physical Vapor Deposition) | CVD (Chemical Vapor Deposition) |
---|---|---|
Working Mechanism | Physical vaporization of solid materials in a vacuum. | Chemical reactions between gaseous materials and the substrate. |
Operating Temperature | 250°C to 450°C | 450°C to 1050°C |
Coating Substance | Solid materials (metals, alloys, ceramics) | Gaseous materials (ceramics, polymers) |
Coverage Area | Excellent for complex geometries; may require substrate rotation. | Superior conformal coverage on intricate shapes. |
Film Thickness | Thinner, smoother films; less dense but faster to apply. | Thicker, denser, and more uniform films; slower process but superior properties. |
Applications | Jewelry, hardware, automotive parts, surgical tools, drill bits. | Semiconductors, high-temperature ceramics, protective coatings for extreme conditions. |
Environmental Impact | Eco-friendly; no toxic substances produced. | Higher operational costs; specialized equipment required. |
Need help deciding between PVD and CVD for your project? Contact our experts today to find the best solution!