PVD (Physical Vapor Deposition) coating is a sophisticated process used to apply thin, durable, and high-performance coatings to various substrates. The coatings are made by vaporizing a target material in a vacuum environment and depositing it onto a substrate, often in combination with reactive gases to form specific compounds. Common materials used in PVD coatings include titanium nitride (TiN), zirconium nitride (ZrN), chromium nitride (CrN), and diamond-like carbon (DLC). These materials provide enhanced properties such as hardness, wear resistance, corrosion resistance, and aesthetic appeal. The process involves multiple steps, including substrate cleaning, vaporization, reaction, and deposition, ensuring a high-quality and consistent coating.
Key Points Explained:
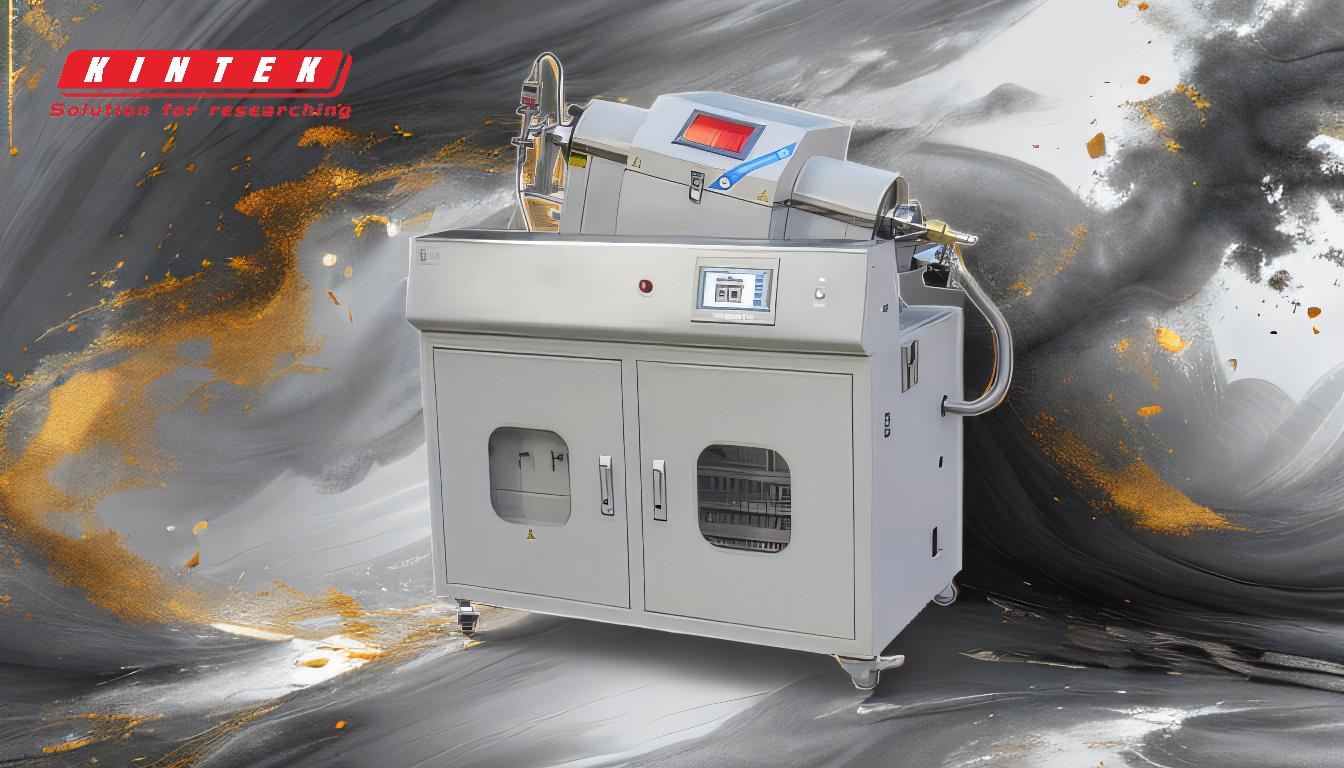
-
Materials Used in PVD Coatings:
- Titanium Nitride (TiN): Known for its gold-like appearance, TiN is widely used for its hardness and wear resistance. It is commonly applied to cutting tools, medical instruments, and decorative finishes.
- Zirconium Nitride (ZrN): Offers excellent corrosion resistance and a bright golden color. It is often used in applications requiring both durability and aesthetics.
- Chromium Nitride (CrN): Provides superior corrosion resistance and is often used in harsh environments, such as in the aerospace and automotive industries.
- Diamond-Like Carbon (DLC): Known for its exceptional hardness and low friction, DLC is used in applications requiring high wear resistance, such as engine components and cutting tools.
-
The PVD Coating Process:
- Substrate Cleaning: The substrate is thoroughly cleaned to remove any contaminants that could affect the adhesion and quality of the coating.
- Vaporization: The target material is vaporized in a vacuum chamber using methods such as electrical arcs, electron beams, or sputtering.
- Reaction: The vaporized material reacts with gases (e.g., nitrogen or oxygen) to form a compound with desired properties, such as hardness or color.
- Deposition: The vaporized and reacted material is deposited onto the substrate, forming a thin, uniform coating.
- Quality Control: Each batch of coated components is tested for consistency, thickness, and color using techniques like X-ray fluorescence (XRF) and spectrophotometry.
-
Key Factors in PVD Coating:
- Line-of-Sight Transfer: PVD is a line-of-sight process, meaning the coating is applied directly to surfaces visible to the vapor source. This requires careful positioning of the substrate.
- Surface Pretreatment: Proper surface preparation, including cleaning and pretreatment, is crucial for ensuring good adhesion and coating quality.
- Vacuum Environment: The process occurs in a high-vacuum environment to prevent contamination and ensure a pure deposition.
- Avoidance of Trapped Air: Tightly sealed tapped holes should be avoided to prevent trapped air from affecting the coating quality.
-
Applications of PVD Coatings:
- Industrial Tools: PVD coatings are widely used on cutting tools, molds, and dies to enhance their durability and performance.
- Medical Instruments: The biocompatibility and corrosion resistance of PVD coatings make them ideal for surgical tools and implants.
- Decorative Finishes: PVD coatings are used in the jewelry and watchmaking industries for their aesthetic appeal and durability.
- Automotive and Aerospace: Components in these industries benefit from the wear and corrosion resistance provided by PVD coatings.
-
Advantages of PVD Coatings:
- Durability: PVD coatings are highly durable and resistant to wear, corrosion, and high temperatures.
- Versatility: The process is compatible with a wide range of materials, including metals, plastics, and ceramics.
- Aesthetic Appeal: PVD coatings can be tailored to achieve various colors and finishes, enhancing the visual appeal of the coated products.
- Environmental Friendliness: The PVD process is environmentally friendly, as it does not involve harmful chemicals or produce hazardous waste.
In summary, PVD coatings are made from a variety of materials, each offering unique benefits, and are applied through a precise and controlled process to enhance the performance and appearance of various products.
Summary Table:
Material | Properties | Common Applications |
---|---|---|
Titanium Nitride (TiN) | Hardness, wear resistance, gold-like appearance | Cutting tools, medical instruments, decorative finishes |
Zirconium Nitride (ZrN) | Corrosion resistance, bright golden color | Applications requiring durability and aesthetics |
Chromium Nitride (CrN) | Superior corrosion resistance | Aerospace, automotive, and harsh environment applications |
Diamond-Like Carbon (DLC) | Exceptional hardness, low friction | Engine components, cutting tools, high-wear resistance applications |
Interested in enhancing your products with PVD coatings? Contact us today to learn more!