PVD (Physical Vapor Deposition) equipment is a specialized system used to deposit thin films of material onto a substrate in a vacuum environment. This process involves vaporizing a solid material, which then condenses onto the substrate to form a thin, durable coating. PVD is widely used in industries such as electronics, automotive, aerospace, and decorative applications due to its ability to produce high-quality, wear-resistant, and environmentally friendly coatings. The equipment typically includes components like a vacuum chamber, target material, power supply, and control systems to manage gas flow, pressure, and temperature. PVD coatings are known for their durability, precision, and versatility, making them ideal for enhancing product performance and appearance.
Key Points Explained:
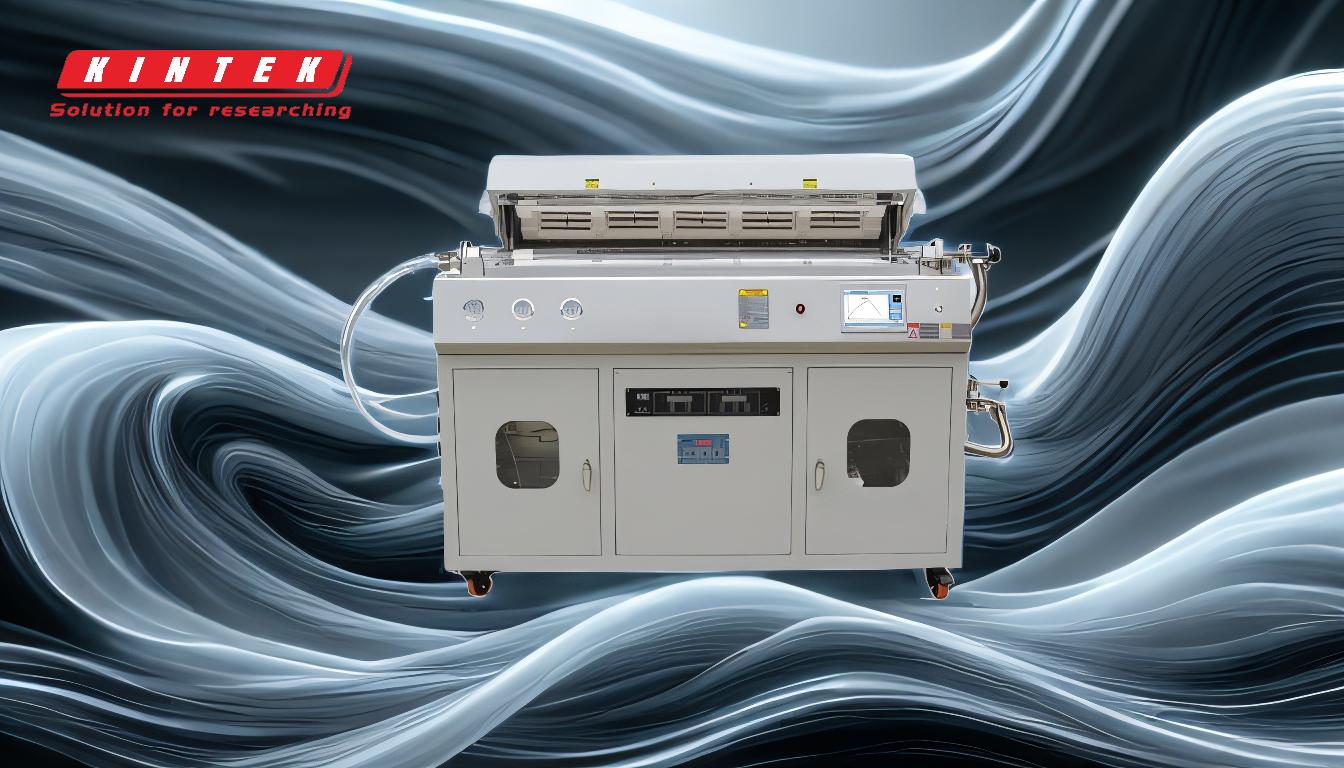
-
What is PVD Equipment?
- PVD equipment is a system designed to deposit thin films of material onto a substrate using a vacuum-based process. The process involves vaporizing a solid target material, which then condenses onto the substrate to form a thin, uniform coating. This equipment is essential for creating coatings that are highly durable, wear-resistant, and environmentally friendly.
-
How PVD Works
- The PVD process occurs in a vacuum chamber to ensure a clean environment. The target material is vaporized using techniques such as sputtering, electron beam evaporation, or cathodic arc. The vaporized material then condenses onto the substrate, forming a thin film. Reactive gases can be introduced to modify the composition of the coating, enhancing its properties.
-
Key Components of PVD Equipment
- Vacuum Chamber: Maintains the low-pressure environment necessary for the PVD process.
- Target Material: The solid material that is vaporized to form the coating.
- Power Supply: Provides the energy needed to vaporize the target material.
- Control Systems: Manage gas flow, chamber pressure, and temperature to ensure precise coating deposition.
- Cooling System: Removes excess heat generated during the process to maintain stable operating conditions.
-
Applications of PVD Coatings
- Durable-Decorative Coatings: Used in consumer products like watches, jewelry, and smartphones to enhance appearance and durability.
- Performance Coatings: Applied to industrial tools, automotive parts, and aerospace components to improve wear resistance and performance.
- Diamond-Like Carbon (DLC) Coatings: Provide exceptional hardness and low friction, making them ideal for cutting tools and engine components.
- PVD Chrome Alternatives: Offer a more environmentally friendly and cost-effective alternative to traditional chrome plating.
- Copper Coatings: Used in electronics for their excellent electrical conductivity and thermal properties.
-
Advantages of PVD Coatings
- Durability: PVD coatings are highly resistant to wear, corrosion, and chemical attack.
- Precision: The process allows for precise control over coating thickness and composition.
- Environmental Impact: PVD is a clean process that produces minimal waste and does not involve harmful chemicals.
- Versatility: PVD can be used to deposit a wide range of materials, including metals, ceramics, and composites.
-
Comparison with Other Coating Techniques
- PVD is often compared to Chemical Vapor Deposition (CVD). While both are vacuum-based processes, PVD operates at lower temperatures and typically results in thinner coatings. PVD is also more suitable for coating temperature-sensitive materials, whereas CVD is better for high-temperature applications.
-
Future Trends in PVD Technology
- The demand for PVD coatings is expected to grow due to their superior properties and environmental benefits. Advances in PVD equipment, such as improved control systems and more efficient power supplies, are likely to enhance the precision and efficiency of the process. Additionally, the development of new target materials and coating compositions will expand the range of applications for PVD technology.
In summary, PVD equipment is a critical tool for creating high-performance, durable, and environmentally friendly coatings. Its versatility and precision make it an essential technology in various industries, from electronics to aerospace. As technology advances, PVD is expected to play an increasingly important role in the development of innovative materials and products.
Summary Table:
Aspect | Details |
---|---|
Definition | System for depositing thin films of material onto a substrate in a vacuum. |
Key Components | Vacuum chamber, target material, power supply, control systems, cooling. |
Process | Vaporizes solid material, which condenses onto the substrate. |
Applications | Electronics, automotive, aerospace, decorative coatings, and more. |
Advantages | Durable, precise, environmentally friendly, and versatile. |
Comparison with CVD | Operates at lower temperatures, thinner coatings, and better for sensitive materials. |
Ready to enhance your products with PVD coatings? Contact us today to learn more!