Physical Vapor Deposition (PVD) is a critical technology in semiconductor fabrication, primarily used for depositing thin films of materials onto substrates. It is widely employed in the microelectronics industry due to its reliability, cost-effectiveness, and ability to produce high-quality, uniform films. PVD processes, such as sputtering and evaporation, are essential for creating microchips, thin-film photovoltaic cells, and other semiconductor devices. These processes involve vaporizing a solid material and depositing it onto a substrate, resulting in films with excellent adhesion and purity. PVD is also used in decorative applications, but its role in semiconductor manufacturing is particularly significant.
Key Points Explained:
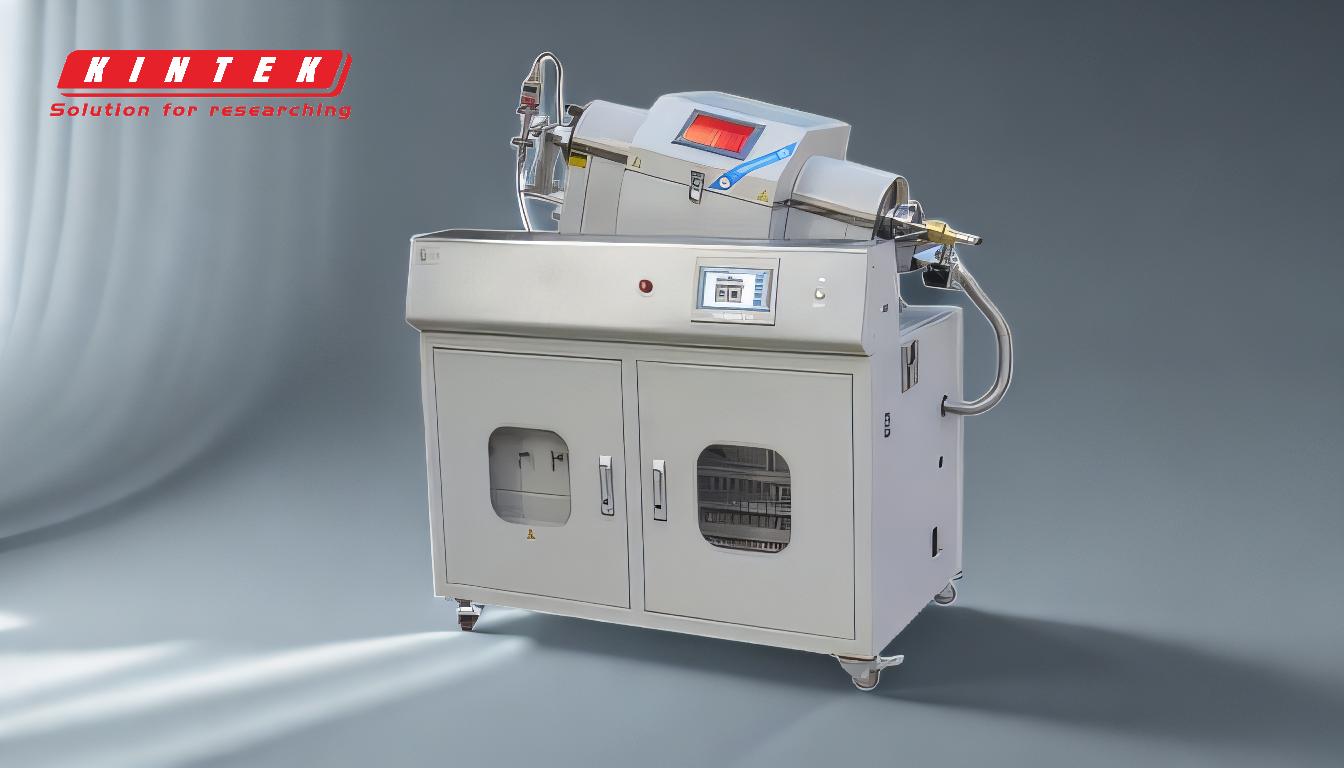
-
Definition and Importance of PVD in Semiconductors:
- PVD is a process used to deposit thin films of materials onto substrates, which is crucial in semiconductor fabrication.
- It is highly valued for its reliability, cost-effectiveness, and ability to produce uniform, high-quality films.
- PVD is extensively used in the microelectronics industry, which is one of the largest markets for PVD equipment.
-
Main PVD Methods in Semiconductor Fabrication:
- Sputtering: The most widely-used PVD method in semiconductors. It involves bombarding a target material with high-energy ions, causing atoms to be ejected and deposited onto a substrate.
- Evaporation: Less commonly used than sputtering, this method involves heating a material until it vaporizes and then condenses onto a substrate.
- Both methods are essential for creating microchips and thin-film photovoltaic cells.
-
Types of PVD Processes:
- Thermal Evaporation: Material is heated until it enters the gas phase and then deposited onto a substrate.
- Sputter Deposition: Includes techniques like magnetron sputtering, where a magnetic field enhances the sputtering process.
- Ion Plating: Combines sputtering and evaporation with ion bombardment to improve film adhesion and density.
- Cathodic Arc Deposition: Uses an electric arc to vaporize material from a cathode target.
- Reactive Deposition: Involves a chemical reaction between the vaporized material and a reactive gas.
- Laser Ablation: Uses a laser to vaporize material from a target.
-
Applications of PVD in Semiconductors:
- Microchips: Metals like platinum, tungsten, or copper are sputter-coated onto silicon wafers, sometimes in multilayered depositions.
- Thin-Film Photovoltaic Cells: Materials like copper, indium, gallium, or tellurium are coated on glass or plastic substrates to create solar cells.
- PVD is also used in other industries, such as decorative hardware, but its role in semiconductors is paramount.
-
Advantages of PVD in Semiconductor Manufacturing:
- High Purity: PVD processes result in extremely pure films, which are essential for semiconductor performance.
- Uniformity: The films produced are highly uniform, ensuring consistent performance across the substrate.
- Adhesion: PVD films adhere well to the substrate, which is crucial for the durability and functionality of semiconductor devices.
- Versatility: PVD can deposit a wide range of materials, including metals, alloys, and composites, making it suitable for various semiconductor applications.
-
Comparison with Other Deposition Techniques:
- PVD is often compared with Chemical Vapor Deposition (CVD). While CVD involves chemical reactions to deposit films, PVD relies on physical processes, making it more suitable for certain materials and applications.
- PVD is generally more cost-effective and produces films with better adhesion and purity compared to some other deposition methods.
-
Future Trends in PVD for Semiconductors:
- Advanced Materials: Research is ongoing to develop new materials and composites that can be deposited using PVD for enhanced semiconductor performance.
- Process Optimization: Efforts are being made to optimize PVD processes for higher throughput and lower costs, making it even more attractive for large-scale semiconductor manufacturing.
- Integration with Other Technologies: PVD is being integrated with other fabrication techniques to create more complex and multifunctional semiconductor devices.
In summary, PVD is a cornerstone technology in semiconductor fabrication, offering a reliable and cost-effective method for depositing high-quality thin films. Its versatility and ability to produce uniform, adherent films make it indispensable in the production of microchips, photovoltaic cells, and other semiconductor devices. As the semiconductor industry continues to evolve, PVD technology is expected to play an increasingly important role in enabling the next generation of electronic devices.
Summary Table:
Aspect | Details |
---|---|
Definition | Deposits thin films of materials onto substrates for semiconductor devices. |
Main Methods | Sputtering, Evaporation. |
Key Processes | Thermal Evaporation, Sputter Deposition, Ion Plating, Laser Ablation. |
Applications | Microchips, Thin-Film Photovoltaic Cells, Decorative Hardware. |
Advantages | High purity, uniformity, adhesion, and versatility. |
Future Trends | Advanced materials, process optimization, integration with other tech. |
Discover how PVD can elevate your semiconductor manufacturing—contact our experts today!