PVD (Physical Vapor Deposition) treated stainless steel refers to stainless steel that has been coated with a thin ceramic layer through the PVD process. This coating enhances the steel's properties, such as corrosion resistance, durability, and aesthetic appeal, while preserving the texture and finish of the underlying material. The PVD coating is extremely thin (0.5 to 5 microns) and highly adherent, making it difficult to remove. It provides additional benefits like scratch resistance, improved hardness, and protection against environmental factors, making it ideal for applications requiring both functionality and visual appeal.
Key Points Explained:
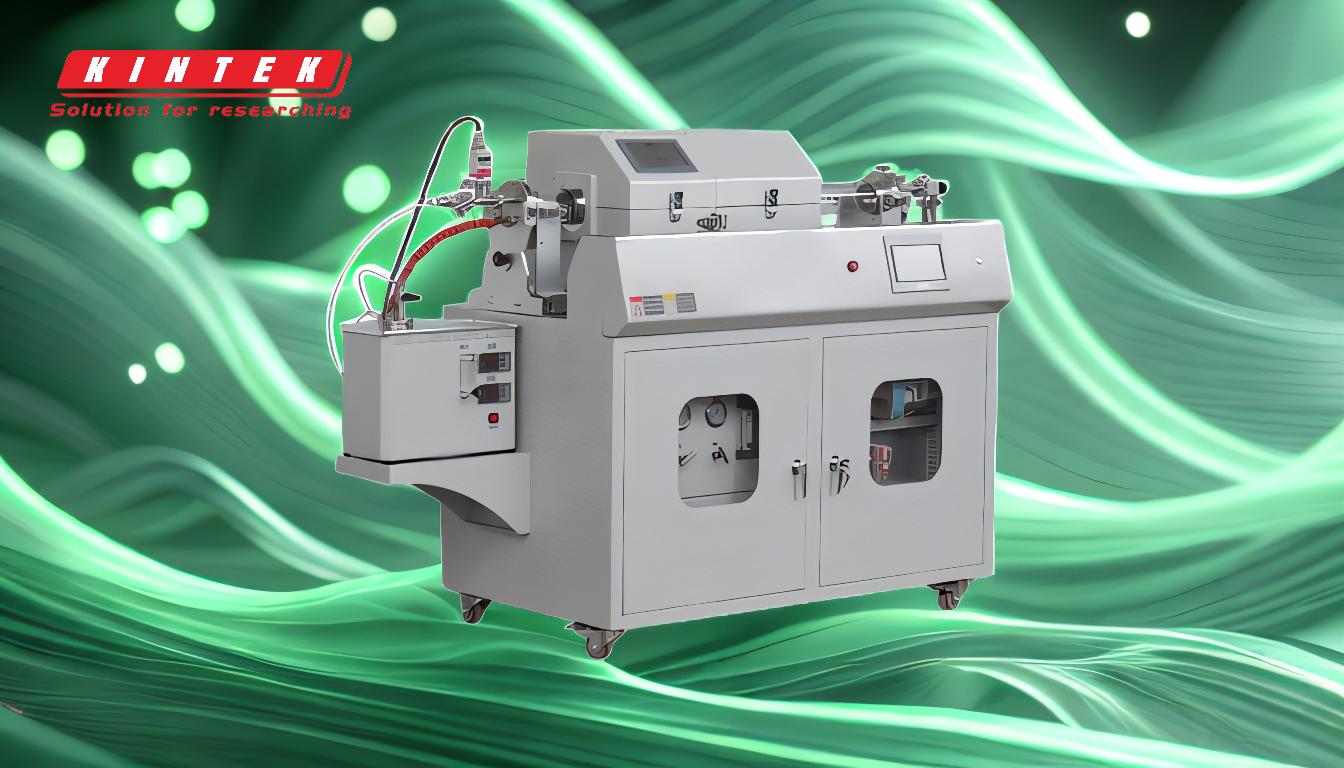
-
What is PVD Coating?
- PVD (Physical Vapor Deposition) is a process that deposits a thin ceramic coating onto a substrate, such as stainless steel.
- The coating is extremely thin, ranging from 0.5 to 5 microns, and is applied in a vacuum environment.
- This process allows the texture and finish of the underlying stainless steel to remain visible while enhancing its properties.
-
Benefits of PVD Coating on Stainless Steel
- Enhanced Corrosion and Oxidation Resistance: PVD coatings provide a protective barrier that significantly improves the steel's resistance to staining, corrosion, and oxidation.
- Improved Durability: The coating increases the hardness and wear resistance of stainless steel, making it more resistant to scratches, abrasions, and discoloration.
- Aesthetic Appeal: PVD coatings can replicate or enhance the original finish of stainless steel, offering a wide range of colors and finishes while maintaining the material's visual appeal.
-
Adhesion and Robustness of PVD Coatings
- PVD coatings exhibit excellent adhesion to stainless steel due to high levels of metal ionization during the deposition process.
- The coatings are more robust compared to other coating methods, offering consistent quality and durability.
- Their thinness and strong bonding make them difficult to remove, ensuring long-lasting performance.
-
Functional Improvements
- PVD coatings can improve the fatigue limit and endurance of stainless steel, as seen in other materials like Ti-6Al-4V alloy, where a TiN coating increased the fatigue limit by 22%.
- The hardness of the coating plays a critical role in determining its durability and resistance to wear and tear.
-
Applications of PVD-Treated Stainless Steel
- PVD-treated stainless steel is widely used in industries requiring both functionality and aesthetics, such as architecture, automotive, consumer electronics, and medical devices.
- It is ideal for applications where resistance to environmental conditions, scratches, and discoloration is essential.
-
Combination of Strength and Aesthetics
- PVD-plated stainless steel combines the inherent strength and durability of stainless steel with the enhanced properties of the PVD coating.
- This combination makes it a versatile material for applications that demand both performance and visual appeal.
In summary, PVD-treated stainless steel is a high-performance material that offers improved durability, corrosion resistance, and aesthetic versatility, making it suitable for a wide range of industrial and decorative applications.
Summary Table:
Key Feature | Description |
---|---|
Coating Thickness | 0.5 to 5 microns |
Enhanced Properties | Corrosion resistance, scratch resistance, improved hardness, and aesthetic appeal |
Adhesion | Excellent adhesion due to high metal ionization, making it difficult to remove |
Applications | Architecture, automotive, consumer electronics, medical devices |
Combination of Benefits | Strength, durability, and visual versatility |
Upgrade your materials with PVD-treated stainless steel—contact us today to learn more!