Pyrolysis plastic recycling is a thermal degradation process that converts waste plastic into valuable products like fuel oil, carbon black, and syngas in the absence of oxygen. This method not only reduces landfill waste and greenhouse gas emissions but also provides an alternative to fossil fuels by generating energy from domestic sources. The process involves preprocessing plastic to meet feeding requirements, heating it in a pyrolysis furnace, and producing pyrolysis oil and carbon black at high temperatures. Pyrolysis is a simple, cost-effective technology that addresses environmental concerns, reduces water pollution, and creates economic opportunities through waste cleanup and job creation.
Key Points Explained:
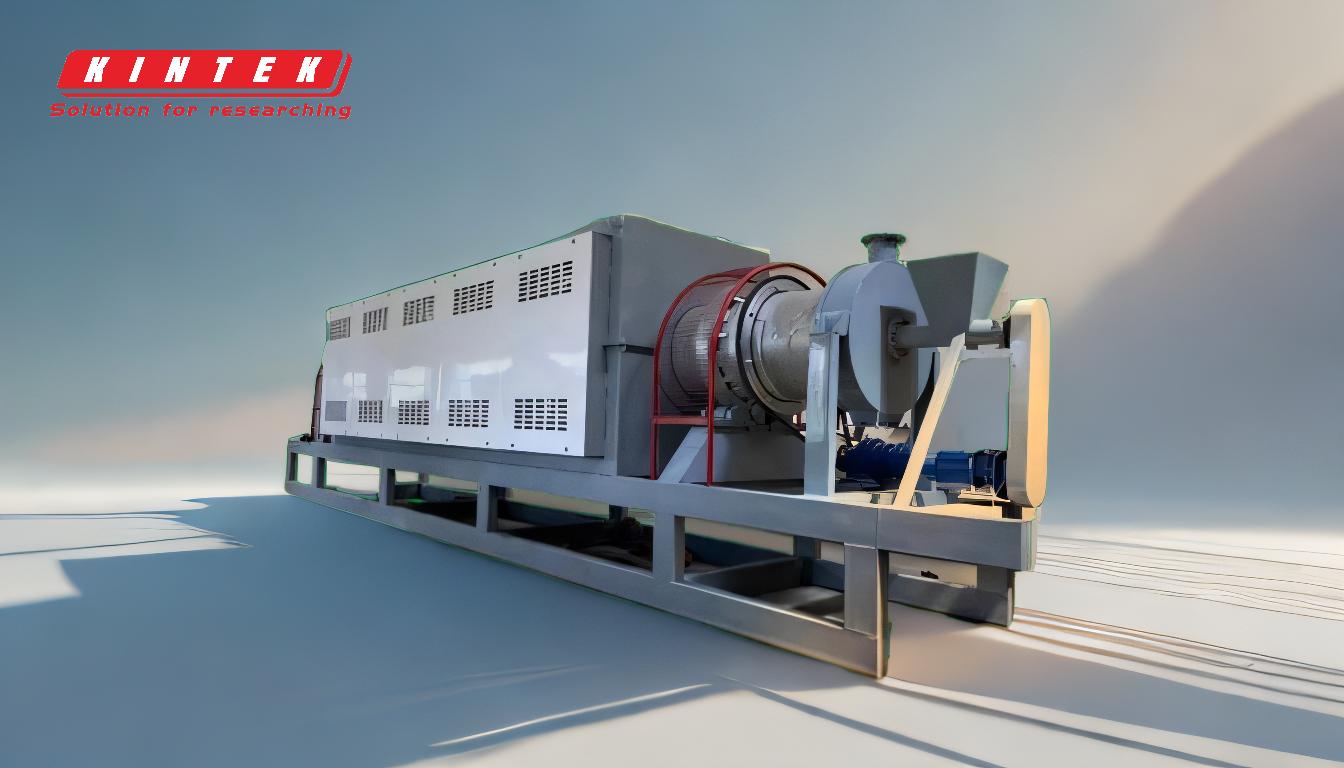
-
Definition and Process of Pyrolysis Plastic Recycling:
- Pyrolysis is a thermal degradation process that breaks down waste plastic into smaller molecules in the absence of oxygen.
- The process involves heating plastic at high temperatures, typically around 280°C, to produce fuel oil, carbon black, and syngas.
- Preprocessing steps, such as ensuring the correct size and moisture content of plastic, are crucial for efficient operation and high-quality output.
-
Environmental and Economic Benefits:
- Reduction in Landfill Waste: Pyrolysis significantly reduces the volume of plastic waste sent to landfills, mitigating environmental pollution.
- Greenhouse Gas Emission Reduction: By converting waste into usable energy, pyrolysis helps lower greenhouse gas emissions compared to traditional waste disposal methods.
- Energy Independence: The process generates fuel oil and syngas, reducing reliance on imported energy resources and promoting the use of domestic energy.
- Job Creation and Public Health: Pyrolysis plants create jobs and improve public health by cleaning up waste and reducing the risk of water pollution.
-
Advantages of Pyrolysis Technology:
- Simple and Cost-Effective: Pyrolysis is a straightforward and inexpensive technology for processing various types of plastic waste.
- Toxic Component Degradation: High temperatures in the pyrolysis process degrade toxic components and pathogens, making it a safer waste management option.
- Versatility: The process can handle a wide range of feedstocks, including mixed plastics and rubber, making it highly adaptable.
-
Output Products and Their Uses:
- Fuel Oil: The primary product of pyrolysis, fuel oil, can be used as an alternative to fossil fuels in industrial applications.
- Carbon Black: A byproduct used in manufacturing tires, inks, and other industrial products.
- Syngas: A gaseous mixture that can be used as a fuel source or further processed into chemicals.
-
Challenges and Considerations:
- Feedstock Quality: The efficiency of pyrolysis depends on the quality and consistency of the plastic feedstock, requiring proper preprocessing.
- Energy Consumption: While pyrolysis reduces the need for external fuel, the process itself requires energy, which must be managed efficiently.
- Market for Byproducts: The economic viability of pyrolysis depends on the demand for its byproducts, such as fuel oil and carbon black.
-
Future Prospects:
- Renewable Energy Source: As the world seeks renewable energy alternatives, pyrolysis is gaining importance for its ability to convert waste into energy.
- Waste Management Boost: The process provides a significant boost to waste management by processing solid wastes and plastics that are otherwise difficult to recycle.
- Innovation and Scaling: Ongoing research and development are expected to improve the efficiency and scalability of pyrolysis technology, making it more accessible globally.
In summary, pyrolysis plastic recycling is a promising technology that addresses both environmental and economic challenges by converting waste plastic into valuable resources. Its simplicity, cost-effectiveness, and ability to reduce landfill waste and greenhouse gas emissions make it a viable solution for sustainable waste management and energy production.
Summary Table:
Key Aspect | Details |
---|---|
Process | Thermal degradation of plastic at ~280°C in the absence of oxygen. |
Output Products | Fuel oil, carbon black, and syngas. |
Environmental Benefits | Reduces landfill waste, greenhouse gas emissions, and water pollution. |
Economic Benefits | Creates jobs, promotes energy independence, and generates valuable byproducts. |
Challenges | Feedstock quality, energy consumption, and market demand for byproducts. |
Future Prospects | Renewable energy source, improved waste management, and scalable technology. |
Transform waste into energy with pyrolysis technology—contact us today to learn more!