Pyrolysis technology for biomass energy involves the thermal decomposition of organic materials, such as biomass, in the absence of oxygen. This process occurs at high temperatures (typically 500°C–700°C) and breaks down biomass into three main products: pyrolysis vapor, gas, and char. The vapor is condensed into bio-crude oil, which can be further processed into transportation fuels or specialty chemicals. Pyrolysis is carried out in specialized equipment, such as a pyrolysis reactor, which includes components like a cracking furnace, feeding system, and heating system. The process is energy-efficient, as uncondensable gases are recycled to power the reactor, reducing external energy requirements. Pyrolysis is a promising technology for converting biomass into renewable energy and valuable chemical products.
Key Points Explained:
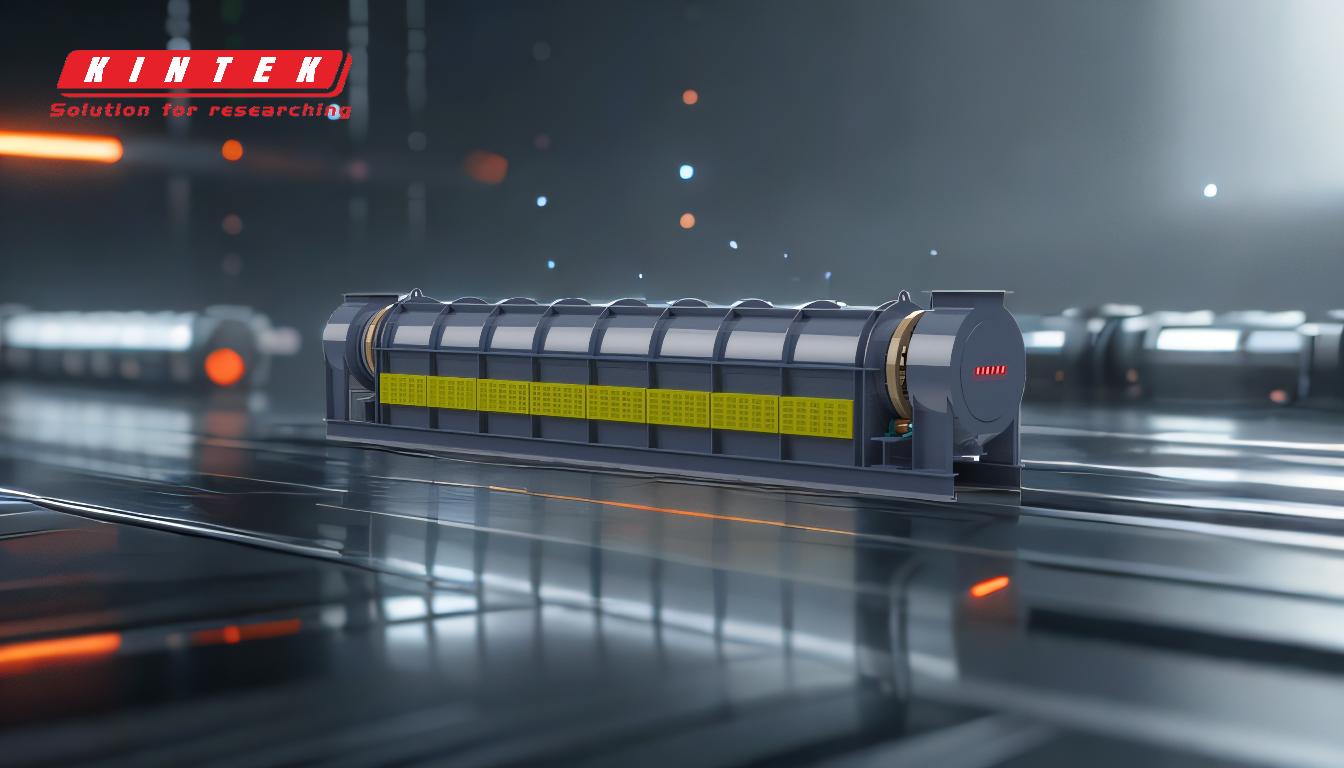
-
What is Pyrolysis?
- Pyrolysis is a thermal decomposition process that occurs in the absence of oxygen. It breaks down biomass into three primary products:
- Pyrolysis vapor: Condensed into bio-crude oil.
- Gas: Can be recycled to power the reactor.
- Char: A solid residue that can be removed and used or disposed of.
- This process typically occurs at high temperatures (500°C–700°C) and is a key method for converting biomass into renewable energy.
- Pyrolysis is a thermal decomposition process that occurs in the absence of oxygen. It breaks down biomass into three primary products:
-
Pyrolysis Equipment and Components
- The core of pyrolysis technology is the pyrolysis reactor, which is designed to handle high temperatures and ensure efficient conversion of biomass. Key components include:
- Cracking furnace: Where the thermal decomposition occurs.
- Feeding system: Supplies biomass to the reactor.
- Heating system: Provides the necessary high temperatures.
- Waste gas recovery and reuse system: Recycles uncondensable gases to reduce energy consumption.
- Dust removal system: Ensures clean operation by removing particulate matter.
- These systems work together to maximize efficiency and product yield.
- The core of pyrolysis technology is the pyrolysis reactor, which is designed to handle high temperatures and ensure efficient conversion of biomass. Key components include:
-
Types of Pyrolysis Reactors
- Pyrolysis can be conducted in various types of reactors, including:
- Fluidized bed reactors: These separate waste flows into two zones—a bed section (low oxygen) for drying, pyrolysis, and gasification, and a free section (with added air) for further combustion.
- Fixed bed reactors: Simpler designs where biomass is heated in a stationary bed.
- The choice of reactor depends on the scale of operation and desired products.
- Pyrolysis can be conducted in various types of reactors, including:
-
Products of Pyrolysis
- The main products of pyrolysis are:
- Bio-crude oil: A liquid fuel that can be upgraded for transportation or used to produce specialty chemicals like adhesives.
- Syngas: A gaseous product that can be used for energy generation or recycled to power the reactor.
- Biochar: A solid residue that can be used as a soil amendment or for carbon sequestration.
- These products make pyrolysis a versatile technology for biomass utilization.
- The main products of pyrolysis are:
-
Energy Efficiency of Pyrolysis
- Pyrolysis plants are designed to be energy-efficient. The uncondensable gases produced during the process are recycled to the burner, reducing the need for external energy sources. This closed-loop system minimizes operational costs and environmental impact.
-
Applications of Pyrolysis Technology
- Pyrolysis has several applications, including:
- Biofuel production: Bio-crude oil can be refined into transportation fuels.
- Chemical production: Specialty chemicals, particularly ring-structure compounds, can be derived from bio-oil.
- Waste management: Pyrolysis can process organic waste, reducing landfill use and generating valuable products.
- These applications highlight the versatility and sustainability of pyrolysis technology.
- Pyrolysis has several applications, including:
-
Solar Pyrolysis
- An emerging variant of pyrolysis is solar pyrolysis, which uses concentrated solar energy as the heat source. This approach upgrades biomass energy by storing solar energy in chemical forms within the pyrolysis products. Solar pyrolysis is particularly promising for regions with abundant sunlight and biomass resources.
-
Environmental and Economic Benefits
- Pyrolysis offers significant environmental benefits, such as reducing greenhouse gas emissions and diverting organic waste from landfills. Economically, it provides a pathway to produce renewable fuels and chemicals, reducing dependence on fossil fuels.
By leveraging pyrolysis technology, biomass can be transformed into valuable energy and chemical products, contributing to a more sustainable and circular economy. The pyrolysis reactor plays a central role in this process, ensuring efficient and effective conversion of biomass into usable resources.
Summary Table:
Aspect | Details |
---|---|
Process | Thermal decomposition of biomass at 500°C–700°C in the absence of oxygen. |
Main Products | Bio-crude oil, syngas, and biochar. |
Key Equipment | Pyrolysis reactor, cracking furnace, feeding system, heating system. |
Energy Efficiency | Uncondensable gases are recycled to power the reactor, reducing energy use. |
Applications | Biofuel production, chemical synthesis, waste management. |
Environmental Benefits | Reduces greenhouse gas emissions and diverts organic waste from landfills. |
Discover how pyrolysis technology can transform your biomass into renewable energy—contact us today to learn more!