Reactive sputtering is a specialized form of Physical Vapor Deposition (PVD) where a reactive gas, such as oxygen or nitrogen, is introduced into the sputtering chamber. This gas chemically reacts with the sputtered atoms from the target material, forming a compound that is then deposited as a thin film on the substrate. This technique allows for the creation of films with precise stoichiometry and tailored properties, such as conductivity, stress, and refractive index. The process is widely used in industries requiring high-performance coatings, such as semiconductors, optics, and protective coatings. However, it requires careful control of parameters like gas flow and partial pressure to avoid hysteresis-like behavior and ensure optimal film quality.
Key Points Explained:
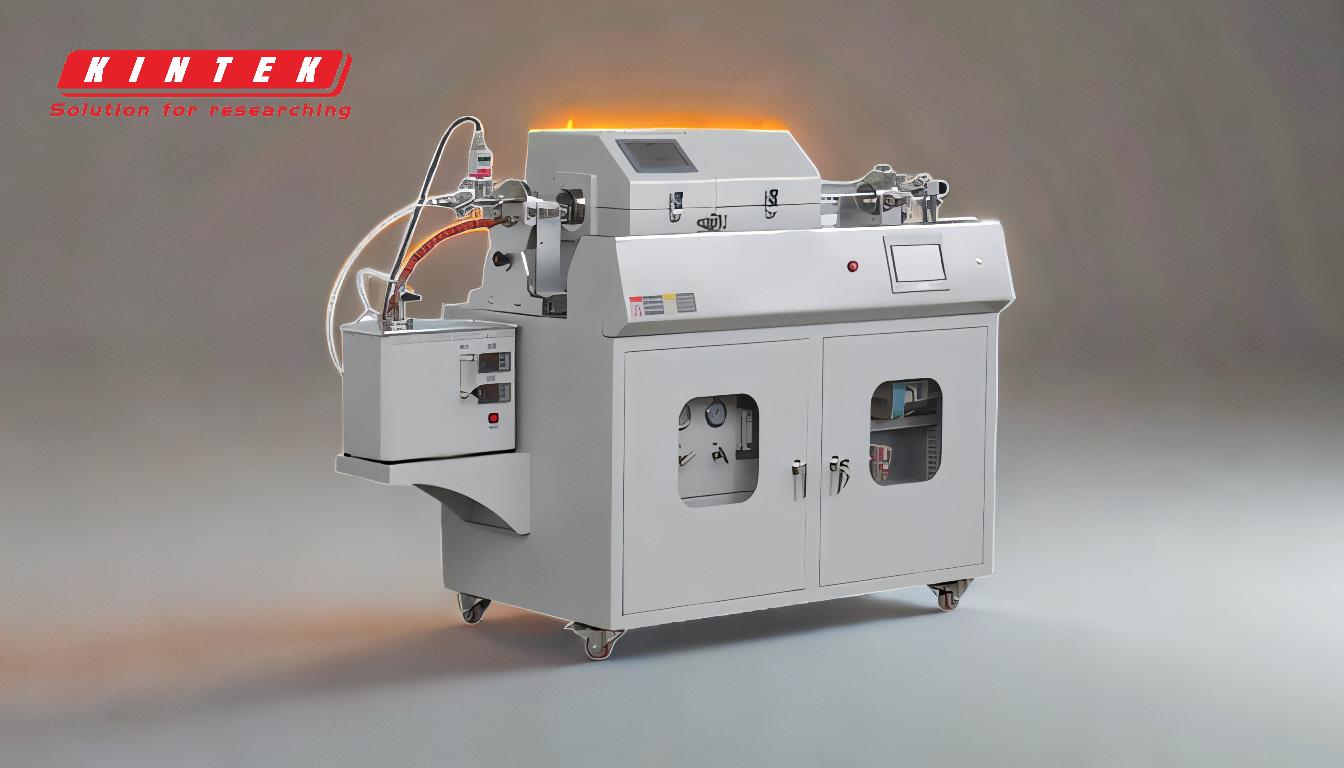
-
Definition and Mechanism of Reactive Sputtering:
- Reactive sputtering is a PVD process where a reactive gas (e.g., oxygen or nitrogen) is introduced into the sputtering chamber.
- The reactive gas chemically reacts with the sputtered atoms from the target material, forming a compound (e.g., oxides or nitrides).
- This compound is then deposited as a thin film on the substrate.
-
Role of Reactive Gases:
- Reactive gases like oxygen (O₂) and nitrogen (N₂) are critical for forming compounds such as titanium oxide (TiO₂) or titanium nitride (TiN).
- These gases are ionized in the plasma environment, enabling them to react with the target material atoms.
-
Process Variants:
- Reactive sputtering can be performed using both DC (Direct Current) and HF (High Frequency) power sources.
- The choice of power source depends on the target material and the desired film properties.
-
Control of Film Stoichiometry:
- The composition and properties of the deposited film can be precisely controlled by adjusting the relative pressures of the inert gas (e.g., argon) and the reactive gas.
- This control is crucial for optimizing functional properties like conductivity, stress, and refractive index.
-
Challenges and Complexity:
- The introduction of reactive gases complicates the process, often leading to hysteresis-like behavior.
- Careful control of parameters such as gas flow, partial pressure, and power is required to achieve consistent and high-quality films.
-
Applications of Reactive Sputtering:
- Reactive sputtering is widely used in industries requiring high-performance thin films, such as:
- Semiconductors (e.g., barrier layers, conductive coatings).
- Optics (e.g., anti-reflective coatings, optical filters).
- Protective coatings (e.g., wear-resistant coatings, corrosion-resistant layers).
- Reactive sputtering is widely used in industries requiring high-performance thin films, such as:
-
The Berg Model:
- The Berg Model is a theoretical framework used to estimate the impact of reactive gases on target erosion and film deposition rates.
- It helps in understanding and optimizing the reactive sputtering process.
-
Examples of Reactive Sputtering:
- Sputtering silicon with oxygen to produce silicon oxide (SiO₂) films.
- Sputtering titanium with nitrogen to produce titanium nitride (TiN) films.
-
Advantages of Reactive Sputtering:
- Enables the deposition of compound films with tailored properties.
- Provides precise control over film stoichiometry and structure.
- Suitable for a wide range of applications, from electronics to decorative coatings.
-
Considerations for Equipment and Consumables Purchasers:
- When selecting equipment for reactive sputtering, consider:
- Compatibility with reactive gases.
- Control systems for gas flow and pressure.
- Power supply options (DC or HF).
- For consumables, ensure the target material and reactive gases are of high purity to achieve optimal film quality.
- When selecting equipment for reactive sputtering, consider:
By understanding these key points, purchasers of equipment and consumables can make informed decisions to optimize their reactive sputtering processes for specific applications.
Summary Table:
Key Aspect | Details |
---|---|
Definition | A PVD process using reactive gases to form compound thin films. |
Reactive Gases | Oxygen (O₂), nitrogen (N₂) for compounds like TiO₂ or TiN. |
Process Variants | DC or HF power sources, depending on target material and film properties. |
Film Control | Adjust inert/reactive gas pressures for precise stoichiometry. |
Challenges | Hysteresis-like behavior; requires precise gas flow and pressure control. |
Applications | Semiconductors, optics, protective coatings. |
Berg Model | Estimates reactive gas impact on target erosion and deposition rates. |
Examples | SiO₂ (silicon oxide), TiN (titanium nitride) films. |
Advantages | Tailored film properties, precise control, wide application range. |
Purchasing Considerations | Equipment compatibility, gas/pressure control, high-purity consumables. |
Optimize your reactive sputtering process—contact our experts today for tailored solutions!