Silicon carbide (SiC) is a compound of silicon and carbon, known for its exceptional hardness and durability. It is widely used in refractory applications due to its unique properties, including high thermal conductivity, resistance to thermal shock, and excellent chemical stability. SiC is utilized in industries such as metallurgy, ceramics, and chemicals, where it serves as a key material for high-temperature and wear-resistant applications. Its ability to withstand extreme conditions makes it invaluable in the production of refractory materials, which are essential for lining furnaces, kilns, and reactors.
Key Points Explained:
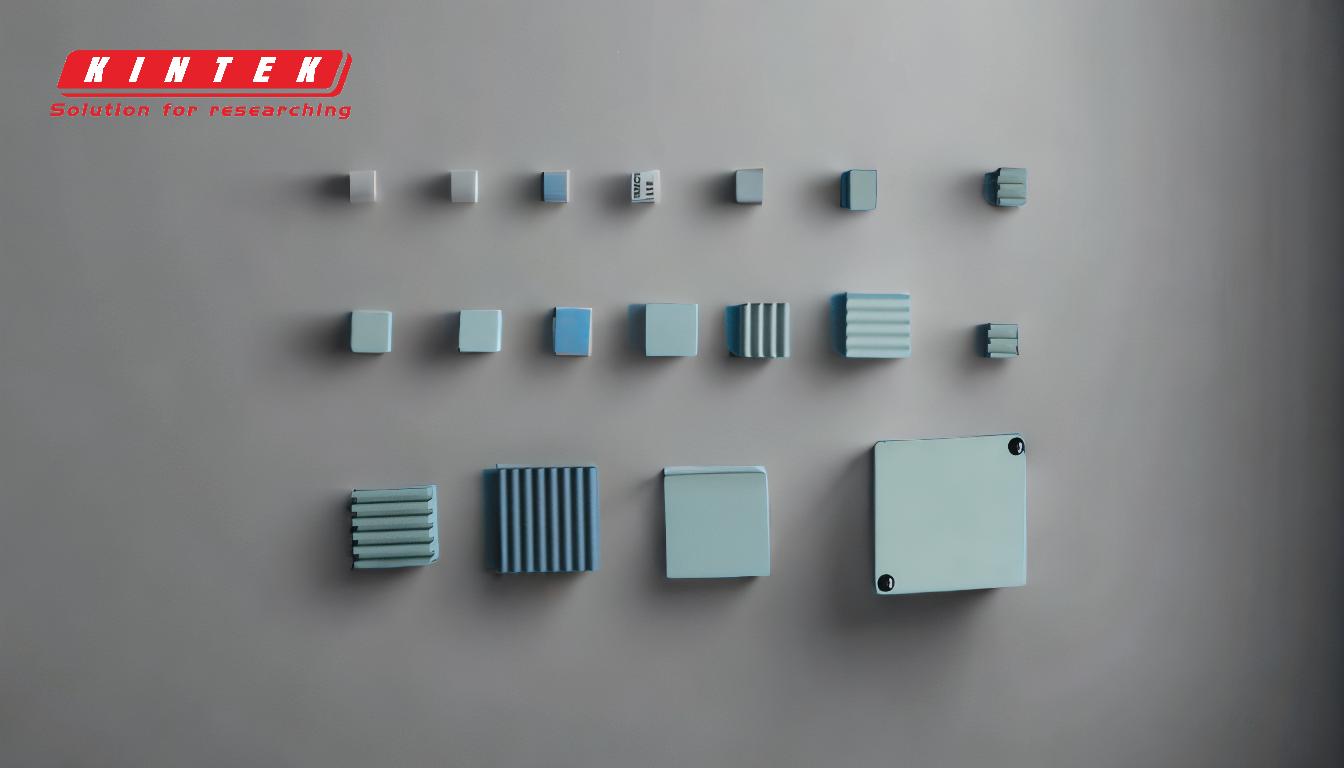
-
Composition and Properties of SiC:
- Silicon carbide is a compound made up of silicon and carbon, often referred to as carborundum.
- It is characterized by its extreme hardness, which is comparable to that of diamond, and its low density.
- SiC exhibits outstanding chemical resistance, making it inert to most acids, alkalis, and molten metals.
- It also has high thermal conductivity and excellent resistance to thermal shock, which are critical properties for refractory materials.
-
Applications in Refractory Materials:
- SiC is used in the production of refractory bricks, crucibles, and other components that are exposed to high temperatures and corrosive environments.
- In metallurgical industries, SiC-based refractories are used to line furnaces and ladles, where they provide resistance to thermal and mechanical stresses.
- In the ceramic industry, SiC is used in kiln furniture, such as shelves and setters, due to its ability to withstand repeated heating and cooling cycles without cracking.
-
Advantages in High-Temperature Environments:
- SiC's high melting point (approximately 2700°C) makes it suitable for applications involving extreme heat.
- Its resistance to oxidation and thermal shock ensures long-term durability in harsh conditions, reducing the need for frequent replacements.
- The material's low thermal expansion coefficient minimizes the risk of cracking under thermal cycling, which is a common issue in refractory applications.
-
Industrial Significance:
- The unique combination of properties in SiC makes it a preferred material for industries requiring high-performance refractory solutions.
- Its use in electrical industries, particularly in semiconductors, highlights its versatility and importance in modern technology.
- The growing demand for energy-efficient and durable materials in industrial processes has further increased the relevance of SiC in refractory applications.
In summary, silicon carbide (SiC) is a critical material in refractory applications due to its exceptional hardness, thermal stability, and chemical resistance. Its ability to perform reliably in extreme conditions makes it indispensable in industries such as metallurgy, ceramics, and chemicals, where it enhances the efficiency and longevity of high-temperature processes.
Summary Table:
Property | Description |
---|---|
Composition | Silicon and carbon compound (carborundum) |
Hardness | Comparable to diamond, extremely hard and durable |
Thermal Conductivity | High, ensuring efficient heat transfer |
Thermal Shock Resistance | Excellent, withstands rapid temperature changes |
Chemical Stability | Resistant to acids, alkalis, and molten metals |
Applications | Refractory bricks, crucibles, kiln furniture, furnace linings |
Industrial Use | Metallurgy, ceramics, chemicals, and semiconductors |
Interested in how SiC can enhance your industrial processes? Contact us today for expert advice!