Silicon carbide chemical vapor deposition (CVD) is a specialized process used to produce high-quality silicon carbide (SiC) films or coatings on substrates. This method involves the chemical reaction of gaseous precursors in a vacuum environment, which results in the deposition of silicon carbide onto a heated surface. The process is widely used in industries requiring materials with exceptional hardness, thermal conductivity, and resistance to wear and corrosion. Silicon carbide ceramic, produced via CVD, is particularly valued for its superior mechanical and thermal properties, making it ideal for applications in semiconductors, aerospace, and high-temperature environments.
Key Points Explained:
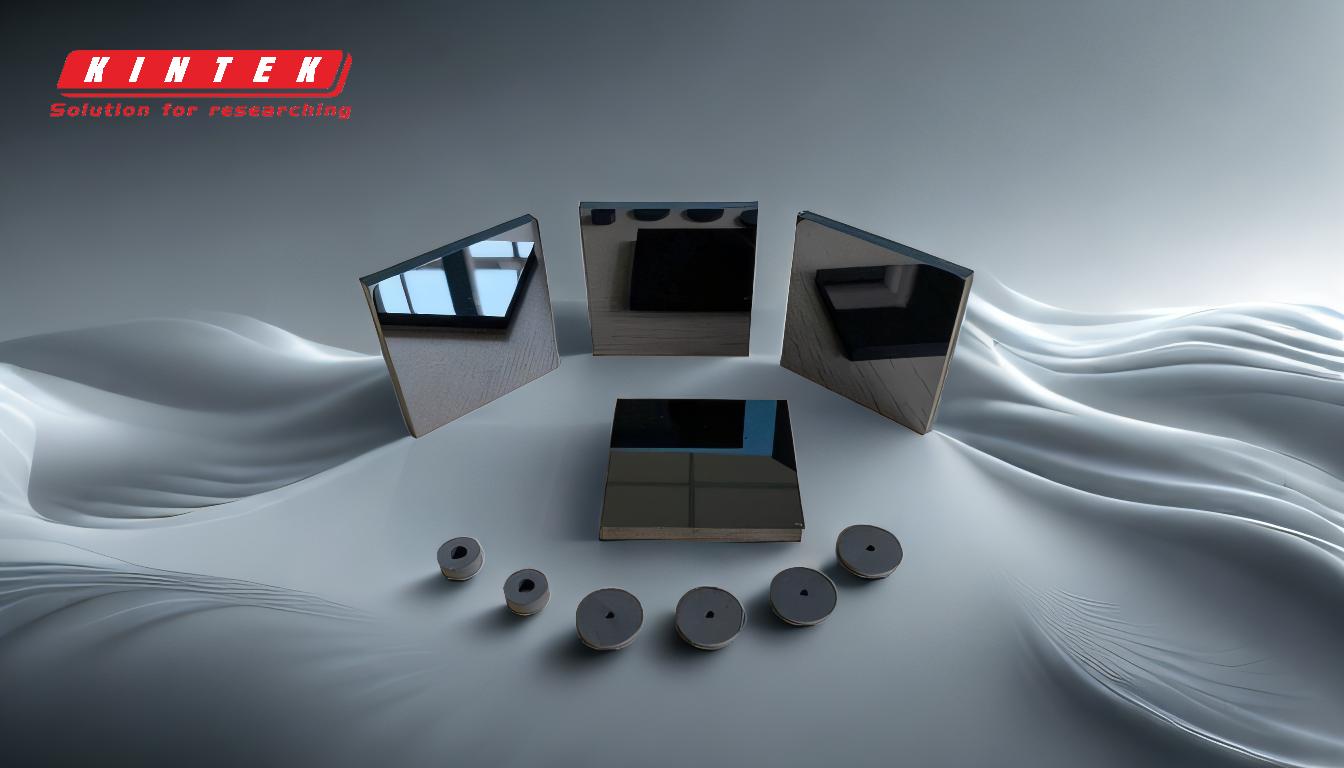
-
Definition of Chemical Vapor Deposition (CVD):
- CVD is a thin-film deposition process where a solid film is formed on a heated surface due to a chemical reaction in the vapor phase. This process typically involves atoms, molecules, or a combination of both as depositing species.
- The process is conducted in a vacuum environment, where particulate chemicals are drawn to the workpiece's surface, leading to a chemical reaction that hardens the material.
-
Silicon Carbide CVD Process:
- Silicon carbide CVD involves the use of gaseous precursors, such as silane (SiH₄) and methane (CH₄), which react at high temperatures to form silicon carbide (SiC) on a substrate.
- The substrate is heated to temperatures ranging from 800°C to 1600°C, depending on the desired properties of the SiC film.
- The reaction occurs in a controlled vacuum environment, ensuring uniform deposition and high-quality SiC films.
-
Advantages of Silicon Carbide CVD:
- High Purity: The CVD process produces silicon carbide with high purity, essential for applications in semiconductors and electronics.
- Uniformity: The process allows for the deposition of uniform and thin SiC films, which are critical for precision applications.
- Exceptional Properties: Silicon carbide ceramic produced via CVD exhibits superior hardness, thermal conductivity, and resistance to wear and corrosion, making it suitable for demanding environments.
-
Applications of Silicon Carbide CVD:
- Semiconductors: SiC is used in power electronics due to its high thermal conductivity and wide bandgap, which allow for efficient operation at high voltages and temperatures.
- Aerospace: The material's resistance to extreme temperatures and wear makes it ideal for components in aerospace applications.
- Industrial Tools: SiC coatings are used to enhance the durability and performance of cutting tools and wear-resistant parts.
-
Challenges in Silicon Carbide CVD:
- High Costs: The process requires specialized equipment and high temperatures, leading to increased production costs.
- Complexity: Achieving uniform deposition and controlling the reaction parameters can be challenging, requiring advanced expertise and technology.
In summary, silicon carbide chemical vapor deposition is a sophisticated process that leverages vacuum technology and chemical reactions to produce high-quality silicon carbide films. The resulting silicon carbide ceramic is highly valued for its exceptional properties and is widely used in advanced industrial applications. For more details on silicon carbide ceramic, visit silicon carbide ceramic.
Summary Table:
Aspect | Details |
---|---|
Process | Chemical reaction of gaseous precursors in a vacuum environment. |
Temperature Range | 800°C to 1600°C, depending on desired SiC film properties. |
Advantages | High purity, uniformity, exceptional hardness, thermal conductivity, and wear resistance. |
Applications | Semiconductors, aerospace, industrial tools. |
Challenges | High costs and process complexity. |
Discover how silicon carbide CVD can revolutionize your applications—contact our experts today!