Sintered ceramic, often referred to as sintered stone or artificial stone, is a man-made material created by grinding natural components like silica, quartz, feldspars, clay, and mineral pigments into fine particles. These particles are then compacted under high heat and pressure, without melting, to form a solid, durable slab. This process enhances the material's mechanical strength, hardness, and thermal stability, making it suitable for various applications, including ceramic tiles, cutting tools, and refractory materials. Silicon carbide (SiC) ceramics, known for their excellent mechanical and thermal properties, play a significant role in this process, especially in high-tech fields like semiconductors and space technology.
Key Points Explained:
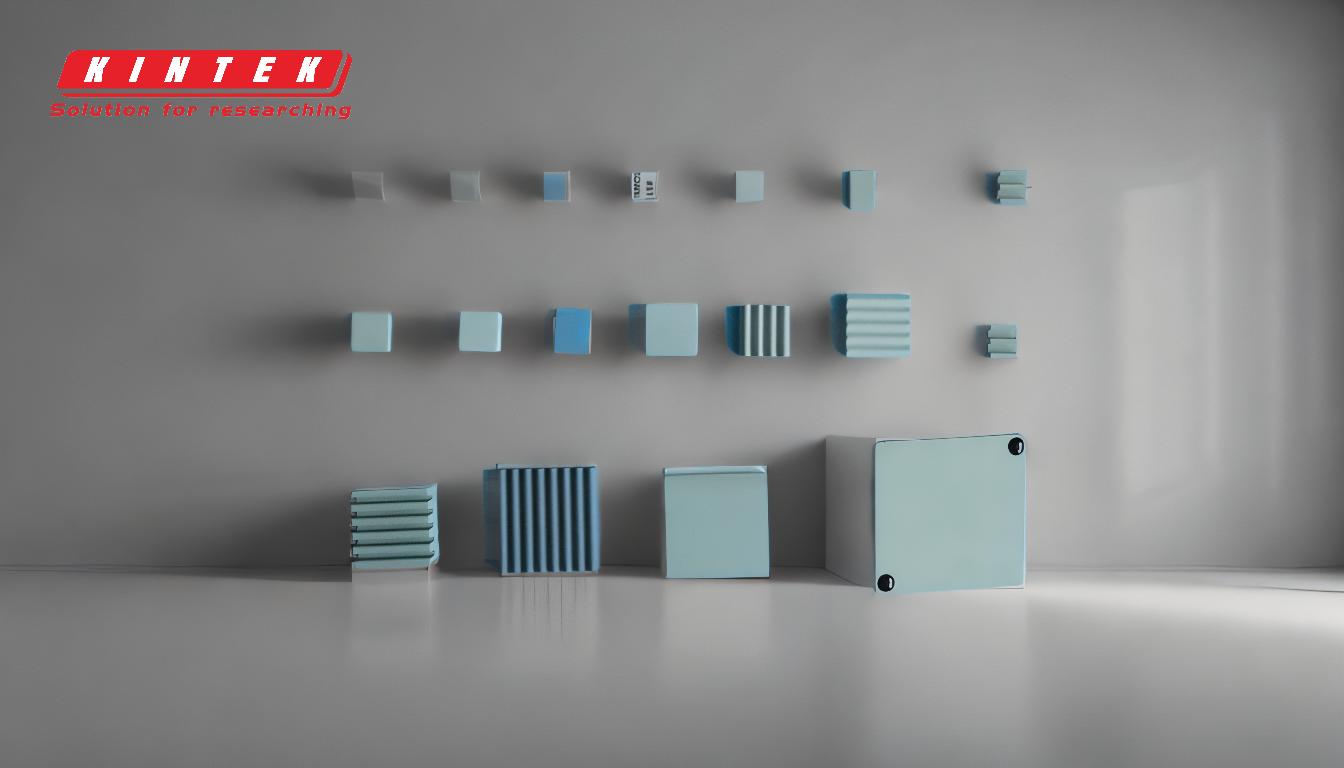
-
Definition of Sintered Ceramic:
- Sintered ceramic is a man-made material formed by compacting natural materials like silica, quartz, feldspars, clay, and mineral pigments under high heat and pressure. This process consolidates the powdery structure, reducing porosity and creating a solid, durable slab.
-
Sintering Process:
- The sintering process involves grinding natural materials into fine particles and then compacting them using heat and pressure. This process does not involve melting the materials but rather fusing them together at high temperatures, typically around 1200°C, to form a solid structure.
-
Role of Silicon Carbide (SiC) in Sintering:
- Silicon carbide (SiC) ceramics are widely used in the sintering process due to their excellent mechanical, thermal, and chemical properties. They are used in receiving capsules and muffles for sintering technical ceramics and porcelain, making them essential in both traditional and high-tech industries.
-
Applications of Sintered Ceramics:
- Sintered ceramics are used in a variety of applications, including:
- Ceramic tiles and sanitaryware.
- Cutting tools and refractory materials.
- Electrical insulators.
- High-tech fields such as semiconductors, nuclear energy, national defense, and space technology.
- Sintered ceramics are used in a variety of applications, including:
-
Advantages of Sintered Ceramics:
- Mechanical Strength: Sintered ceramics have high mechanical strength, making them durable and long-lasting.
- Thermal Stability: They can withstand high temperatures, making them suitable for applications requiring thermal resistance.
- Chemical Resistance: Sintered ceramics are resistant to chemical corrosion, enhancing their usability in harsh environments.
- Low Porosity: The sintering process reduces porosity, resulting in a denser and more robust material.
-
Control of Sintering Parameters:
- The properties of sintered ceramics, such as density, porosity, and microstructure, are carefully controlled by adjusting sintering parameters like temperature, pressure, and duration. This ensures the final product meets specific performance requirements.
-
Historical Context:
- Silicon nitride ceramic, initially produced by reacting elemental silicon with nitrogen or ammonia, was first used as a binder for silicon carbide refractory materials. This historical development highlights the importance of sintering in advancing ceramic technology.
In summary, sintered ceramics are versatile materials with a wide range of applications, from everyday items like tiles to advanced technologies in space and defense. The use of silicon carbide (SiC) in the sintering process enhances the material's properties, making it indispensable in both traditional and high-tech industries. The careful control of sintering parameters ensures that the final product meets the desired specifications, providing a reliable and durable solution for various applications.
Summary Table:
Aspect | Details |
---|---|
Definition | Man-made material from natural components compacted under heat and pressure. |
Sintering Process | Grinding and compacting particles at ~1200°C without melting. |
Key Material | Silicon carbide (SiC) enhances mechanical and thermal properties. |
Applications | Tiles, cutting tools, refractory materials, semiconductors, space tech. |
Advantages | High strength, thermal stability, chemical resistance, low porosity. |
Parameter Control | Temperature, pressure, and duration are adjusted for desired properties. |
Want to learn more about sintered ceramics? Contact our experts today for tailored solutions!