Sintered powdered metal refers to metal parts created through the sintering process in powder metallurgy. This process involves compacting metal powders into a desired shape and then heating them to a temperature below their melting point, causing the particles to fuse together. The result is a solid, durable part with enhanced mechanical properties. Sintering is widely used in industries such as automotive and aerospace due to its ability to produce complex, high-precision parts with minimal material waste. It is also an eco-friendly manufacturing method, offering advantages like energy efficiency, cost-effectiveness, and the ability to tailor material properties to specific applications.
Key Points Explained:
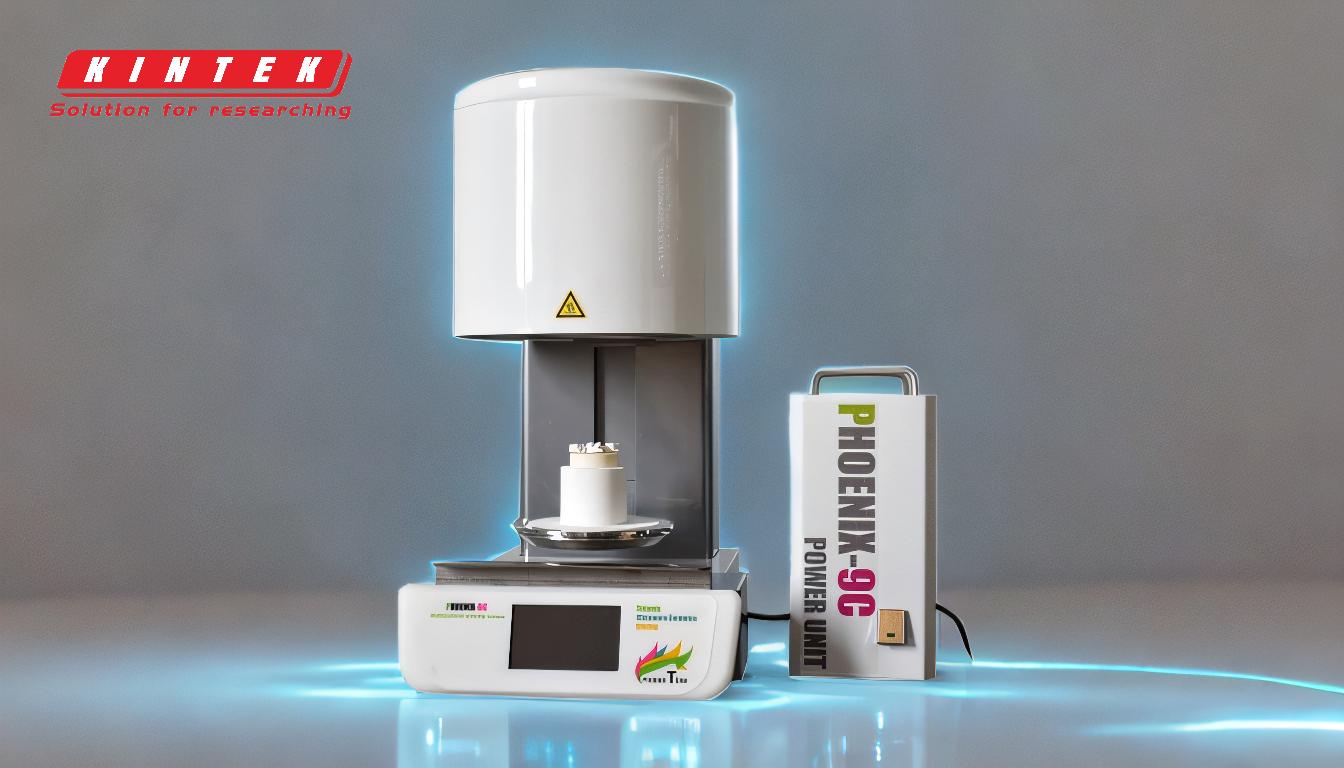
-
Definition of Sintered Powdered Metal:
- Sintered powdered metal is produced through the powder metallurgy process, which involves compacting metal powders into a desired shape and then heating them to fuse the particles without melting the material. This creates a solid, durable part with improved mechanical properties.
-
The Sintering Process:
- Compaction: Metal powders are pressed into a mold to form a "green" part, which is fragile and not yet fully bonded.
- Sintering: The green part is heated in a controlled environment to a temperature below the melting point of the metal. This causes the particles to bond through diffusion, resulting in a denser and stronger structure.
- Post-Processing: Additional steps like sizing, machining, or heat treatment may be applied to achieve the final product specifications.
-
Advantages of Sintered Powdered Metal:
- Complex Geometries: Sintering allows for the production of intricate shapes and internal features that would be difficult or impossible to achieve with traditional manufacturing methods.
- High Precision: The use of molds and dies made with wire EDM ensures tight tolerances and excellent dimensional accuracy.
- Material Efficiency: Powder metallurgy minimizes waste, with up to 97% of the material becoming part of the final product.
- Cost-Effectiveness: The process reduces material and machining costs, making it ideal for both low- and high-volume production.
- Eco-Friendly: Sintering is energy-efficient and produces minimal waste, aligning with green manufacturing principles.
-
Applications of Sintered Powdered Metal:
- Automotive Industry: Used for components like gears, bearings, and engine parts due to their strength, precision, and cost-effectiveness.
- Aerospace Industry: Ideal for lightweight, high-performance parts that require complex geometries and excellent mechanical properties.
- Electronics: Used in soft magnetic composites (SMCs) for applications requiring direct magnetic flux and reduced size and weight.
- General Manufacturing: Suitable for a wide range of parts, from simple to highly complex, across various industries.
-
Material Flexibility:
- Sintered powdered metal can be made from a variety of materials, including iron, steel, copper, and alloys. This allows for tailored material properties to meet specific application requirements, such as wear resistance, thermal conductivity, or magnetic performance.
-
Performance Properties:
- Sintered parts exhibit excellent mechanical properties, including high strength, durability, and resistance to wear and corrosion. They also offer good surface finishes and tight tolerance control, making them suitable for high-performance applications.
-
Economic and Environmental Benefits:
- The powder metallurgy process is energy-efficient and produces minimal scrap, reducing both production costs and environmental impact. This makes it a sustainable choice for modern manufacturing.
By combining these key points, sintered powdered metal emerges as a versatile, efficient, and environmentally friendly manufacturing solution, capable of producing high-quality parts for a wide range of industries.
Summary Table:
Aspect | Details |
---|---|
Definition | Metal parts created by compacting and heating metal powders below melting point. |
Process | Compaction → Sintering → Post-Processing (optional). |
Advantages | Complex geometries, high precision, material efficiency, cost-effectiveness, eco-friendly. |
Applications | Automotive, aerospace, electronics, general manufacturing. |
Material Flexibility | Iron, steel, copper, and alloys for tailored properties. |
Performance | High strength, durability, wear resistance, tight tolerance control. |
Benefits | Energy-efficient, minimal waste, sustainable manufacturing. |
Ready to explore how sintered powdered metal can transform your manufacturing process? Contact us today for expert advice!