Sputter coating in the context of scanning electron microscopy (SEM) is a critical preparatory technique used to enhance the imaging of non-conductive or poorly conductive specimens. By depositing a thin layer of conductive material, typically metals like gold, platinum, or palladium, onto the specimen's surface, sputter coating prevents charging effects caused by the electron beam. This process not only improves conductivity but also enhances the secondary electron signal, leading to clearer and more detailed SEM images. The coating thickness is usually in the range of 2-20 nanometers, ensuring minimal interference with the specimen's original structure while providing the necessary electrical conductivity.
Key Points Explained:
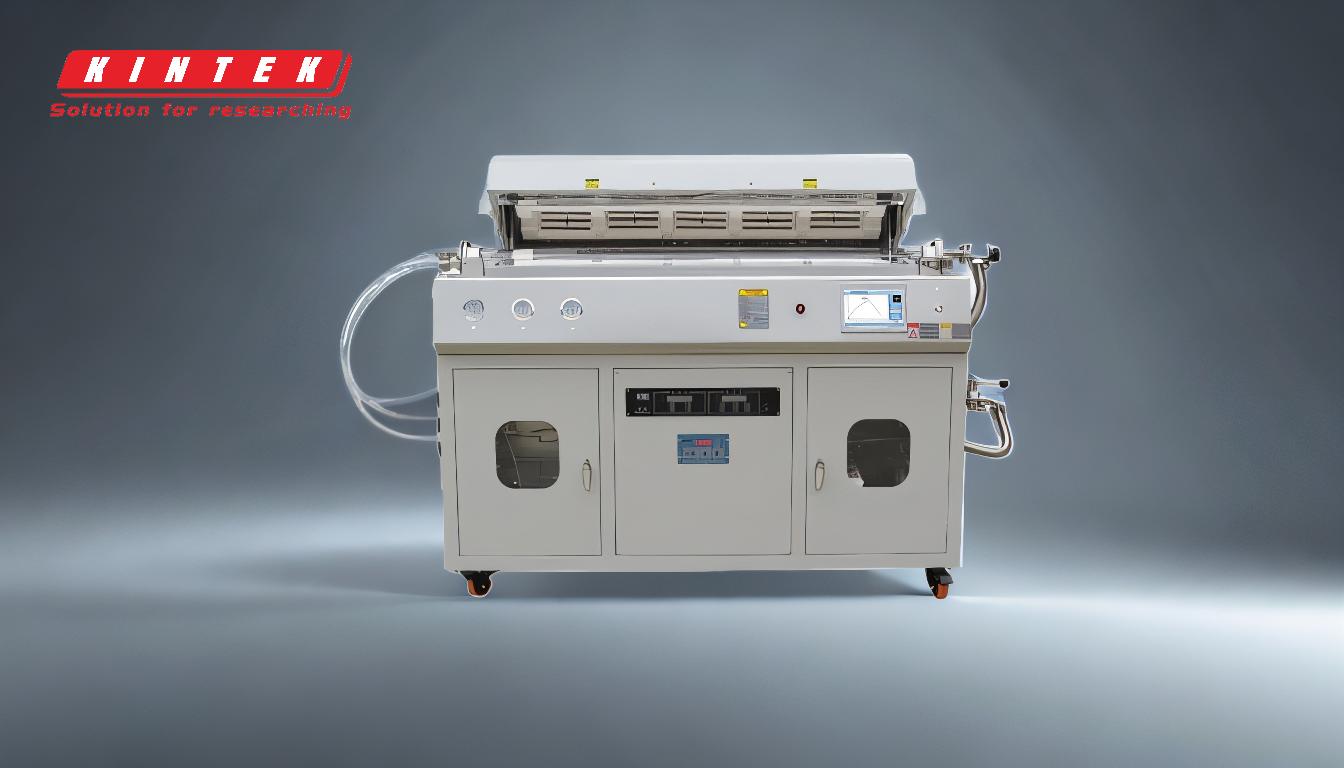
-
Purpose of Sputter Coating in SEM:
- Sputter coating is primarily used to prepare non-conductive or poorly conductive specimens for SEM analysis. Non-conductive materials can accumulate electric charges when exposed to the electron beam, leading to imaging artifacts and distortions. By applying a thin conductive layer, sputter coating neutralizes these charging effects, ensuring accurate and high-quality imaging.
-
Materials Used for Sputter Coating:
- Common materials used for sputter coating include gold (Au), platinum (Pt), palladium (Pd), and their alloys (e.g., gold/palladium). These metals are chosen for their excellent conductivity, ease of deposition, and ability to form uniform, ultra-thin layers. The choice of material depends on the specific requirements of the sample and the desired imaging results.
-
Process of Sputter Coating:
- The sputter coating process involves placing the specimen in a vacuum chamber and introducing a small amount of the coating material. A high-voltage electric field is applied, causing gas ions to collide with the target material, dislodging atoms that then deposit onto the specimen's surface. This results in a uniform, conductive layer that adheres well to the sample.
-
Benefits of Sputter Coating:
- Improved Conductivity: The conductive layer allows the electron beam to interact with the sample without causing charge buildup.
- Enhanced Imaging: By reducing charging effects and increasing secondary electron emission, sputter coating produces clearer and more detailed SEM images.
- Protection Against Beam Damage: The thin metal layer can also protect delicate samples from thermal damage caused by the electron beam.
-
Thickness of the Coating:
- The thickness of the sputter-coated layer typically ranges from 2 to 20 nanometers. This ultra-thin layer is crucial to avoid obscuring fine details of the specimen's surface while providing sufficient conductivity.
-
Applications of Sputter Coating in SEM:
- Sputter coating is widely used in materials science, biology, and nanotechnology for imaging non-conductive samples such as polymers, ceramics, biological tissues, and organic materials. It is also essential for energy-dispersive X-ray spectroscopy (EDS) analysis, where conductivity is required for accurate elemental mapping.
-
Considerations for Sputter Coating:
- Sample Compatibility: Not all samples are suitable for sputter coating. For instance, some biological samples may require alternative preparation methods to avoid damage.
- Coating Uniformity: Achieving a uniform coating is critical to avoid artifacts in the SEM images. Proper calibration of the sputter coater and optimization of coating parameters are necessary.
- Coating Material Selection: The choice of coating material should consider factors such as conductivity, melting point, and compatibility with the sample.
By understanding the principles and techniques of sputter coating, SEM users can effectively prepare non-conductive samples for high-quality imaging and analysis, ensuring accurate and reliable results.
Summary Table:
Aspect | Details |
---|---|
Purpose | Prevents charging effects, improves conductivity, and enhances SEM imaging. |
Materials Used | Gold (Au), platinum (Pt), palladium (Pd), and their alloys. |
Coating Thickness | 2-20 nanometers for minimal interference and optimal conductivity. |
Applications | Materials science, biology, nanotechnology, and EDS analysis. |
Key Benefits | Improved conductivity, enhanced imaging, and protection against beam damage. |
Considerations | Sample compatibility, coating uniformity, and material selection. |
Optimize your SEM imaging with sputter coating—contact our experts today for tailored solutions!