Sputtering atmosphere refers to the controlled environment within a vacuum chamber where the sputtering process takes place. This environment typically involves the introduction of an inert gas, such as argon, which is ionized to create a plasma. The plasma consists of positively charged gas ions that are accelerated towards a target material, causing atoms to be ejected from the target. These ejected atoms then deposit onto a substrate, forming a thin film. The sputtering atmosphere is crucial for ensuring uniform deposition, controlling film thickness, and achieving desired material properties. The process is widely used in industries such as semiconductor manufacturing, solar panel production, and decorative coatings.
Key Points Explained:
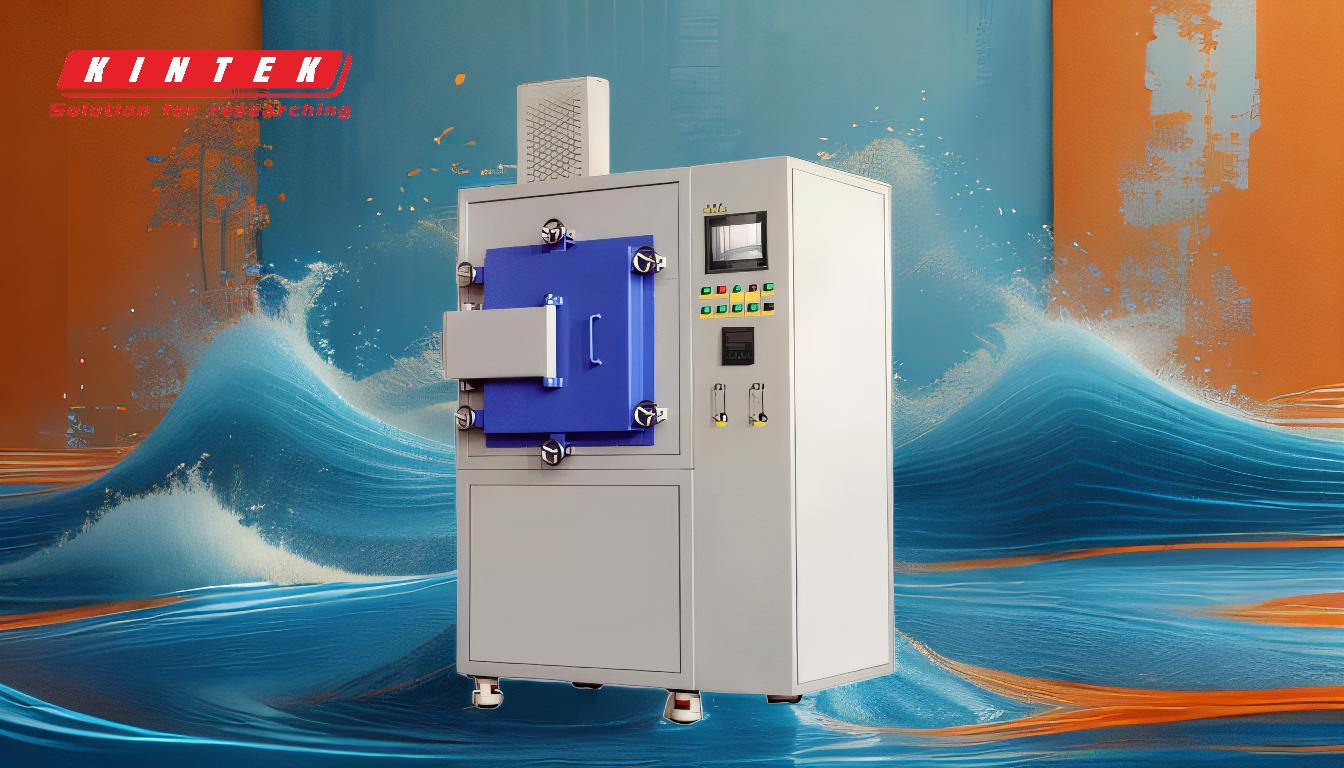
-
Definition of Sputtering Atmosphere:
- The sputtering atmosphere is the controlled environment within a vacuum chamber where the sputtering process occurs. It involves the use of an inert gas, typically argon, which is ionized to create a plasma.
- This plasma is essential for the ejection of atoms from the target material and their subsequent deposition onto a substrate.
-
Role of Inert Gas:
- Inert gases like argon are used because they do not react chemically with the target material or the substrate, ensuring a pure deposition process.
- The gas is introduced into the vacuum chamber at a controlled pressure, which is crucial for maintaining the stability of the plasma.
-
Plasma Generation:
- A high voltage is applied between the target material (cathode) and the chamber walls (anode), creating an electric field.
- This electric field ionizes the inert gas atoms, turning them into positively charged ions.
- The ions are then accelerated towards the target material due to the electric field.
-
Sputtering Process:
- When the high-energy ions collide with the target material, they transfer their momentum to the target atoms, causing them to be ejected.
- These ejected atoms form a vapor stream that travels through the vacuum chamber and deposits onto the substrate, forming a thin film.
-
Importance of Vacuum Environment:
- The vacuum environment minimizes the presence of other gases that could contaminate the deposition process.
- It also allows for precise control over the pressure and flow of the inert gas, which is critical for achieving uniform film deposition.
-
Control Over Film Properties:
- The sputtering atmosphere allows for precise control over film thickness by adjusting parameters such as deposition time, gas pressure, and voltage.
- It also enables the deposition of dense films with reduced residual stress, particularly at lower deposition temperatures.
-
Applications of Sputtering Atmosphere:
- Semiconductor Manufacturing: Used for depositing thin films of metals and dielectrics on silicon wafers.
- Solar Panels: Applied in the production of photovoltaic cells to enhance efficiency.
- Decorative Coatings: Utilized for applying uniform, shiny, and durable coatings on various products, such as automobile wheels and cookware.
-
Variations of Sputtering:
- Anodizing: A variation of sputtering used to give aluminum surfaces a uniform, shiny appearance and resistance to sticking.
- Re-sputtering: Involves the bombardment of deposited material to achieve specific film properties.
-
Historical Context:
- Thomas Edison was one of the first to use sputtering commercially in 1904 for applying thin metal layers to wax phonograph recordings.
- This historical use highlights the long-standing importance of sputtering in industrial applications.
-
Momentum Transfer:
- The sputtering process relies on the transfer of momentum from the high-energy ions to the target atoms, which is a fundamental principle of the technique.
- This momentum transfer is what enables the ejection of atoms from the target and their subsequent deposition onto the substrate.
In summary, the sputtering atmosphere is a critical component of the sputtering process, enabling the precise and controlled deposition of thin films. By understanding and optimizing the sputtering atmosphere, manufacturers can achieve high-quality coatings with specific properties tailored to various industrial applications.
Summary Table:
Key Aspect | Description |
---|---|
Definition | Controlled environment in a vacuum chamber using inert gas (e.g., argon) for plasma generation. |
Role of Inert Gas | Ensures pure deposition by preventing chemical reactions with target or substrate. |
Plasma Generation | High voltage ionizes inert gas, creating positively charged ions for sputtering. |
Sputtering Process | Ions collide with target, ejecting atoms that deposit as a thin film on substrate. |
Vacuum Importance | Minimizes contamination and allows precise control of gas pressure and flow. |
Film Control | Adjustable parameters (time, pressure, voltage) ensure uniform thickness and density. |
Applications | Semiconductors, solar panels, decorative coatings, and more. |
Optimize your thin film deposition process—contact our experts today!