Sputtering PVD (Physical Vapor Deposition) is a thin-film deposition technique where a target material is bombarded by energetic ions from a plasma, typically argon, causing atoms to be ejected from the target. These ejected atoms then travel through the plasma and deposit onto a substrate, forming a thin, uniform film. This process is widely used for depositing materials with high melting points, such as carbon and silicon, as well as alloys. It is effective for creating coatings on complex surfaces and is commonly used in applications like SEM specimen preparation. The process requires low-pressure environments and can handle insulating materials with RF energy sources.
Key Points Explained:
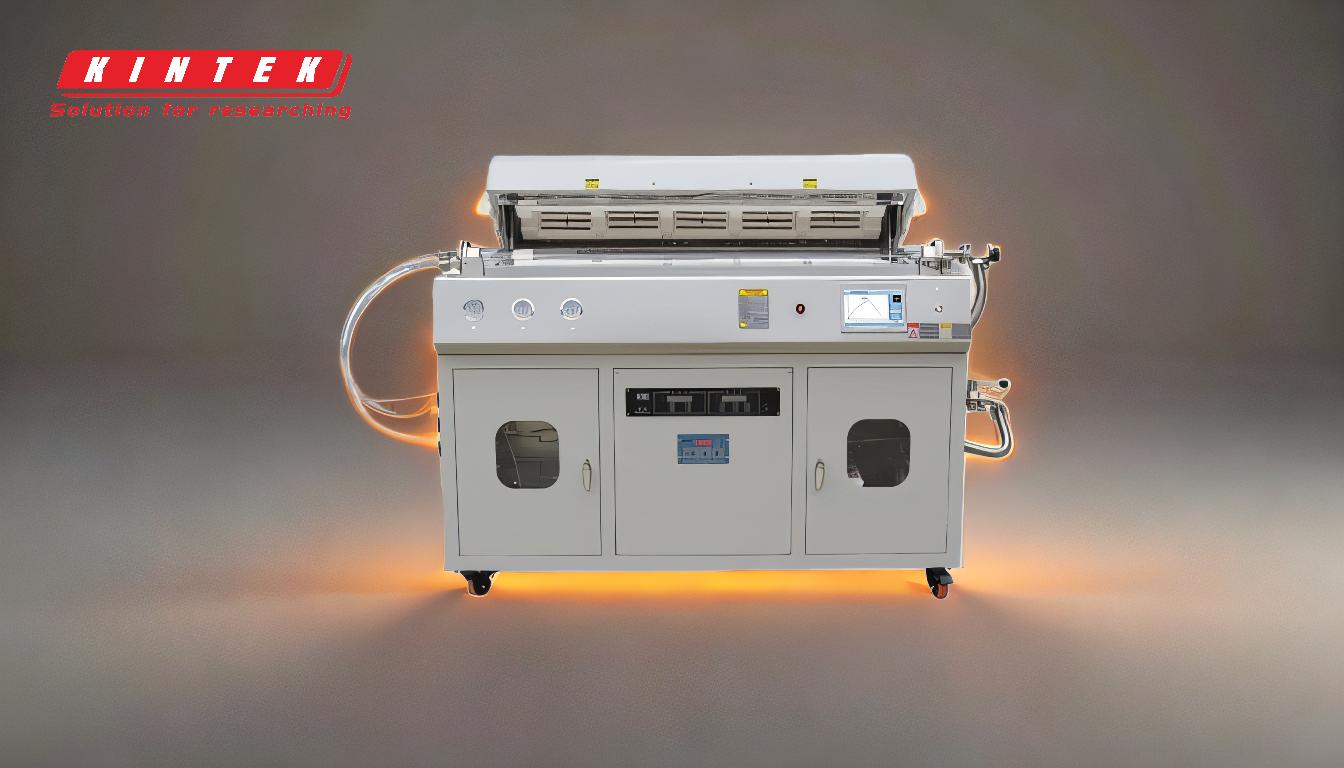
-
Definition of Sputtering PVD Deposition:
- Sputtering PVD is a process where a target material is bombarded by energetic ions from a plasma, causing atoms to be ejected and deposited onto a substrate.
- The plasma typically consists of argon ions and electrons, which are inert to avoid reacting with the substrate.
-
Mechanism of Sputtering:
- Ion Bombardment: High-energy ions (typically argon) collide with the target material, transferring enough energy to dislodge atoms from the target surface.
- Energy Requirement: The energy of the ions must be sufficiently high, typically around 4 times the bond energy of the target material (around 5 eV).
- Atom Ejection: Dislodged atoms from the target are ejected into the plasma and travel towards the substrate.
-
Plasma Generation:
- Plasma Composition: The plasma is generated in a low-pressure environment and consists of argon ions and electrons.
- Role of Plasma: The plasma provides the energetic ions needed for sputtering and ensures the ejected atoms can travel to the substrate.
-
Deposition Process:
- Atom Travel: Ejected atoms travel through the plasma and deposit onto the substrate.
- Film Formation: The deposited atoms form a thin, uniform film on the substrate surface.
-
Applications of Sputtering PVD:
- High Melting Point Materials: Effective for depositing materials with extremely high melting points, such as carbon and silicon.
- Alloys: Suitable for depositing alloy materials.
- Complex Surfaces: Capable of coating complex, three-dimensional surfaces.
- SEM Specimen Preparation: Commonly used to coat specimens with a conductive surface for scanning electron microscopy.
-
Environmental and Material Considerations:
- Low Pressure: Requires a low-pressure environment to maintain the plasma and ensure effective sputtering.
- Insulating Materials: Insulating materials may require an RF energy source to facilitate the sputtering process.
- Inert Gas: The use of inert gases like argon prevents unwanted chemical reactions with the substrate.
-
Advantages of Sputtering PVD:
- Uniform Deposition: Provides a uniform and consistent thin film deposition.
- Versatility: Can deposit a wide range of materials, including high melting point materials and alloys.
- Complex Coatings: Effective for coating complex geometries and three-dimensional surfaces.
-
Challenges and Limitations:
- Energy Requirements: High-energy ions are required, which can be energy-intensive.
- Low Pressure Environment: Maintaining the necessary low-pressure environment can be technically challenging.
- Material Specifics: Certain materials, especially insulators, may require specialized equipment like RF energy sources.
By understanding these key points, one can appreciate the complexity and versatility of sputtering PVD deposition, making it a valuable technique in various industrial and scientific applications.
Summary Table:
Aspect | Details |
---|---|
Definition | Thin-film deposition via ion bombardment of a target material. |
Mechanism | High-energy argon ions eject target atoms, which deposit onto a substrate. |
Applications | High melting point materials, alloys, SEM specimen preparation. |
Advantages | Uniform deposition, versatility, effective for complex geometries. |
Challenges | High energy requirements, low-pressure environment, specialized equipment. |
Discover how Sputtering PVD can enhance your applications—contact our experts today!