Sputtering is a versatile technique widely used across various industries for depositing thin films, cleaning surfaces, and analyzing material compositions. It is a key process in physical vapor deposition (PVD), enabling the creation of thin, uniform coatings on substrates. Applications range from semiconductor manufacturing and optical filters to architectural glass coatings and aerospace components. Sputtering is also utilized in surface physics for preparing high-purity surfaces and analyzing chemical compositions. Its ability to deposit precise, high-quality thin films makes it indispensable in advanced material development and industrial applications.
Key Points Explained:
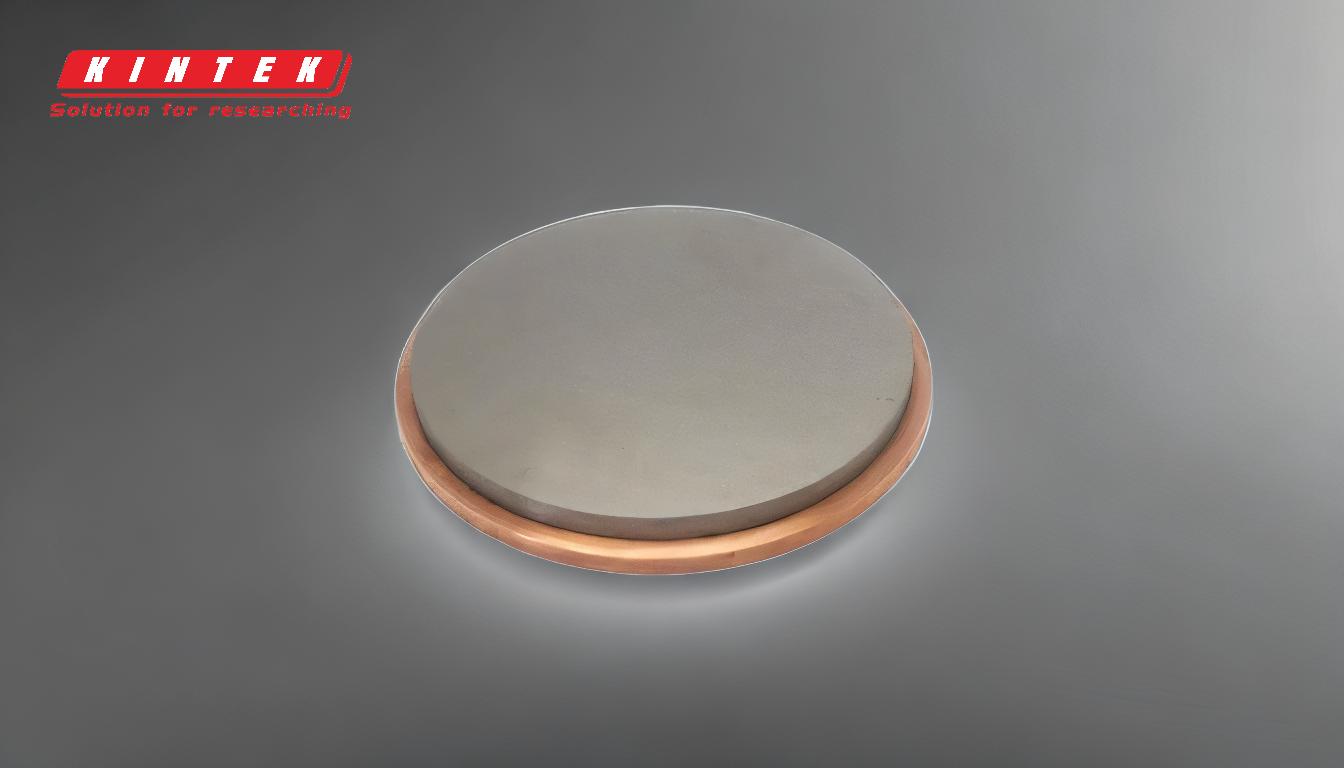
-
Sputter Deposition for Thin Film Creation
- Sputtering is primarily used in sputter deposition, a process that creates thin films ranging from nanometers to micrometers in thickness.
- The process involves bombarding a target material with high-energy ions, causing atoms to be ejected and deposited onto a substrate in a vacuum chamber.
- This method is widely used in industries such as semiconductors, optics, and data storage (e.g., hard disks, CDs, DVDs).
- Thin films produced by sputtering can include alloys, anti-reflective coatings, and high-emissivity films.
-
Surface Cleaning and Preparation
- In surface physics, sputtering is used as a cleaning method to prepare high-purity surfaces.
- By removing contaminants and oxides, sputtering ensures surfaces are pristine for further analysis or processing.
- This application is critical in research and development, where surface purity is essential for accurate results.
-
Chemical Composition Analysis
- Sputtering is employed in techniques like secondary ion mass spectrometry (SIMS) to analyze the chemical composition of surfaces.
- By sputtering away surface layers, researchers can study the elemental and molecular composition of materials at different depths.
- This is particularly useful in materials science and quality control in manufacturing.
-
Applications in the Semiconductor Industry
- Sputtering is crucial for depositing thin films in semiconductor manufacturing, such as metal interconnects and dielectric layers.
- It provides chemically resistant coatings and precise control over film thickness, which is essential for miniaturized electronic components.
- The technique is also used to create anti-reflective coatings on semiconductor devices.
-
Optical and Architectural Applications
- In the optical industry, sputtering is used to produce polarization filters and anti-reflective coatings for lenses and displays.
- For architectural glass, sputtering deposits coatings that enhance energy efficiency, such as low-emissivity (Low-E) films.
- These coatings improve thermal insulation and reduce glare, making them valuable in modern building design.
-
Aerospace and Defense Applications
- Sputtering is used to apply specialized coatings, such as gadolinium films for neutron radiography in aerospace and defense.
- It also creates gas-impermeable films to protect corrosion-prone materials in harsh environments.
- These applications ensure the durability and performance of critical components in demanding conditions.
-
Medical and Surgical Tool Coatings
- Sputtering is employed to produce dielectric stacks that electrically isolate surgical tools, enhancing their safety and performance.
- The technique is also used to create biocompatible coatings for medical implants and devices.
- These applications highlight the importance of sputtering in advancing healthcare technologies.
-
Advancing Material Science and Engineering
- Sputtering plays a key role in developing advanced materials and coatings for smaller, lighter, and more durable products.
- Researchers and engineers use sputtering to innovate in fields such as nanotechnology, renewable energy, and electronics.
- The technique's precision and versatility make it a cornerstone of modern material science.
By leveraging sputtering, industries can achieve high-quality, uniform coatings and surface modifications that are essential for cutting-edge technologies and applications. Its adaptability across diverse fields underscores its importance in both research and industrial processes.
Summary Table:
Application | Key Use Cases |
---|---|
Sputter Deposition | Thin film creation for semiconductors, optics, and data storage (e.g., CDs, DVDs). |
Surface Cleaning | Prepares high-purity surfaces by removing contaminants and oxides. |
Chemical Analysis | Analyzes material composition using techniques like SIMS. |
Semiconductor Industry | Deposits metal interconnects, dielectric layers, and anti-reflective coatings. |
Optical & Architectural | Produces polarization filters, Low-E films, and energy-efficient glass coatings. |
Aerospace & Defense | Applies specialized coatings for neutron radiography and corrosion protection. |
Medical & Surgical Tools | Creates dielectric stacks and biocompatible coatings for medical devices. |
Material Science | Advances nanotechnology, renewable energy, and electronics with precise coatings. |
Unlock the potential of sputtering for your industry—contact our experts today to learn more!