Tablet pressing in the pharmaceutical industry is a critical process that involves compressing powdered or granular active pharmaceutical ingredients (APIs) and excipients into solid tablets of uniform size, shape, and weight. This process is essential for ensuring accurate dosing, ease of administration, and patient compliance. Tablet pressing is achieved using specialized equipment called tablet presses, which apply mechanical force to compress the powders into tablets. The process involves several stages, including filling, compression, and ejection, and requires careful control of parameters such as compression force, speed, and tooling design to produce high-quality tablets. Tablet pressing is widely used in the pharmaceutical industry due to its efficiency, scalability, and ability to produce consistent and reproducible results.
Key Points Explained:
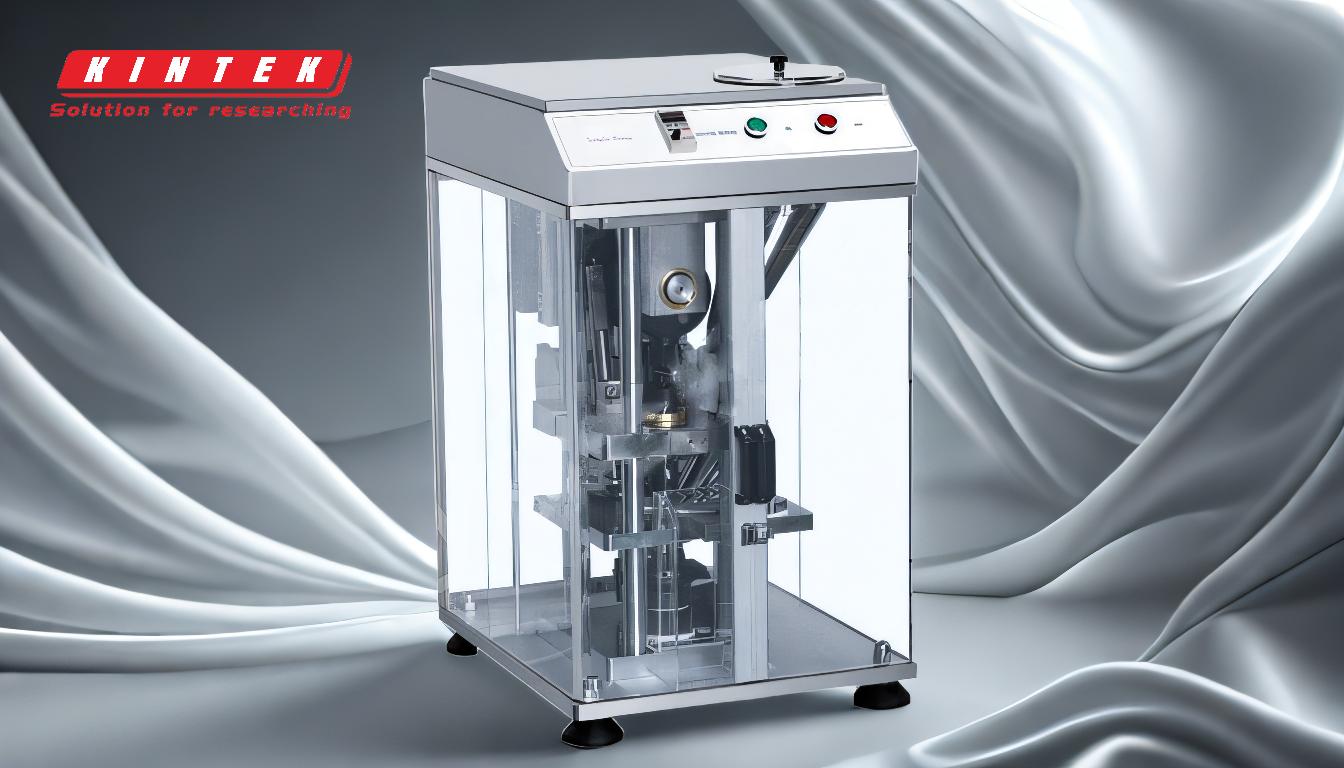
-
Definition and Purpose of Tablet Pressing:
- Tablet pressing is the process of compressing powdered or granular materials into solid tablets using mechanical force.
- The primary purpose is to produce tablets with precise dosages, uniform size, and consistent weight, ensuring patient safety and efficacy.
-
Components of Tablet Pressing:
- Tablet Press Machine: The core equipment used in the process, which applies compression force to the powder blend.
- Punches and Dies: Tooling components that shape the tablets during compression.
- Hopper and Feeder: Systems that deliver the powder blend to the compression area.
- Compression Mechanism: Applies the required force to form the tablets.
- Ejection System: Removes the formed tablets from the dies.
-
Stages of Tablet Pressing:
- Filling: The powder blend is fed into the dies using a feeder system.
- Compression: Punches apply mechanical force to compress the powder into a solid tablet.
- Ejection: The formed tablet is ejected from the die and collected for further processing.
-
Types of Tablet Presses:
- Single-Punch Presses: Suitable for small-scale production or R&D, these presses use one set of punches and dies.
- Rotary Presses: Designed for high-volume production, rotary presses have multiple sets of punches and dies arranged in a circular motion.
-
Critical Parameters in Tablet Pressing:
- Compression Force: Determines the hardness and density of the tablet.
- Speed: Affects the production rate and tablet quality.
- Tooling Design: Influences the shape, size, and surface finish of the tablet.
- Powder Properties: Flowability, particle size, and moisture content impact the compression process.
-
Advantages of Tablet Pressing:
- Precision and Consistency: Ensures accurate dosing and uniform tablet properties.
- Scalability: Suitable for both small-scale and large-scale production.
- Ease of Administration: Tablets are convenient for patients to consume.
- Cost-Effectiveness: Efficient production process reduces manufacturing costs.
-
Challenges in Tablet Pressing:
- Capping and Lamination: Defects caused by improper compression or poor powder properties.
- Sticking and Picking: Issues arising from powder adhesion to the punches.
- Weight Variation: Inconsistent tablet weight due to poor powder flow or feeder issues.
-
Applications in the Pharmaceutical Industry:
- Tablet pressing is used to produce a wide range of pharmaceutical products, including immediate-release tablets, extended-release tablets, and chewable tablets.
- It is also employed in the production of nutraceuticals, vitamins, and other solid dosage forms.
-
Quality Control in Tablet Pressing:
- In-process checks for tablet weight, hardness, thickness, and disintegration time.
- Use of advanced technologies like real-time monitoring and automated inspection systems to ensure product quality.
-
Future Trends in Tablet Pressing:
- Integration of Industry 4.0 technologies, such as IoT and AI, for real-time process optimization.
- Development of continuous manufacturing systems for improved efficiency and flexibility.
- Adoption of advanced materials and coatings to enhance tablet performance and patient experience.
By understanding these key points, pharmaceutical manufacturers can optimize the tablet pressing process to produce high-quality tablets that meet regulatory standards and patient needs.
Summary Table:
Aspect | Details |
---|---|
Definition | Compressing powders into tablets for precise dosing and uniformity. |
Key Components | Tablet press machine, punches, dies, hopper, feeder, compression mechanism. |
Stages | Filling, compression, ejection. |
Types of Presses | Single-punch (small-scale), rotary (high-volume). |
Critical Parameters | Compression force, speed, tooling design, powder properties. |
Advantages | Precision, scalability, ease of administration, cost-effectiveness. |
Challenges | Capping, sticking, weight variation. |
Applications | Pharmaceuticals, nutraceuticals, vitamins, solid dosage forms. |
Quality Control | Weight, hardness, thickness, disintegration checks; real-time monitoring. |
Future Trends | IoT, AI integration, continuous manufacturing, advanced coatings. |
Optimize your tablet pressing process with expert guidance—contact us today!