Injection molding is a widely used manufacturing process for producing plastic parts, and the choice of mold design plays a critical role in determining the efficiency, quality, and complexity of the final product. A three-plate mold offers several advantages over a two-plate mold, primarily due to its additional runner plate. This design allows for more complex part geometries, better control over gate locations, and the ability to separate runners and parts automatically. These features make three-plate molds ideal for high-volume production, multi-cavity setups, and intricate part designs where precision and efficiency are paramount.
Key Points Explained:
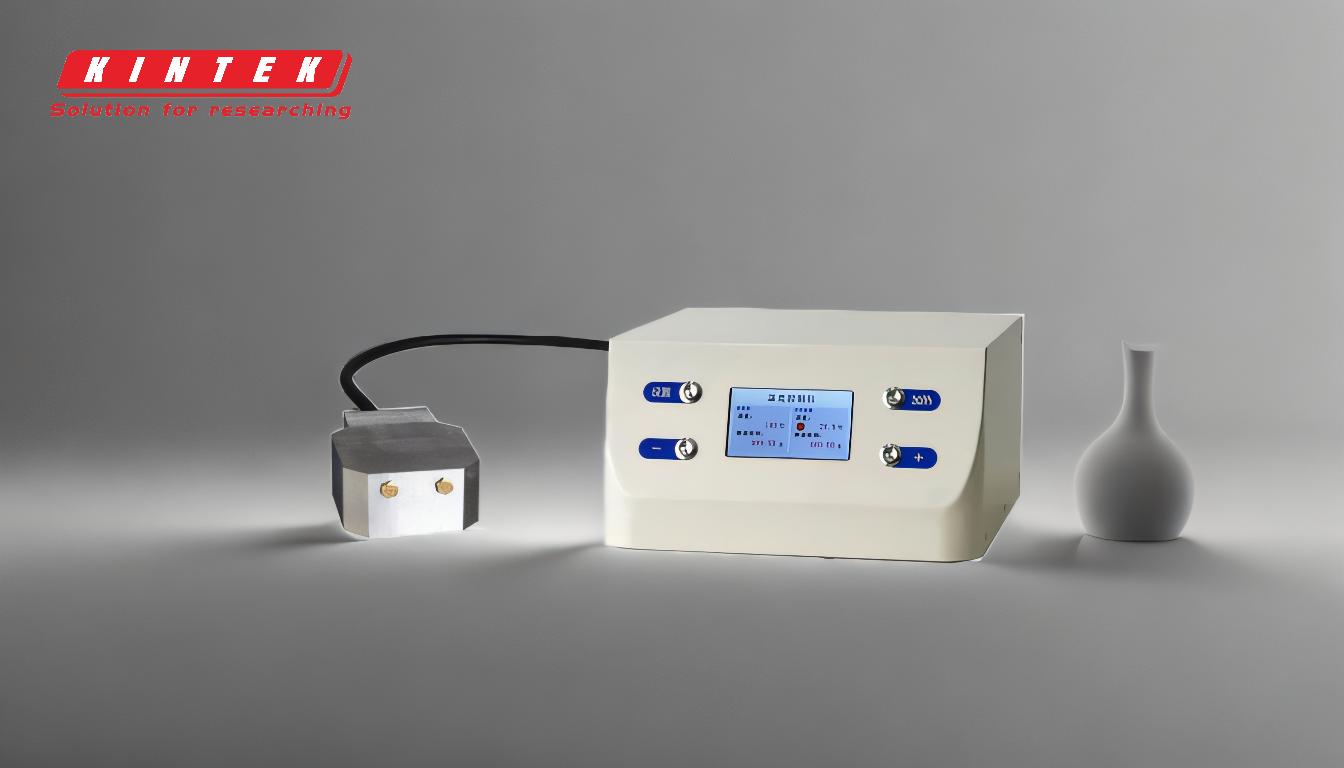
-
Additional Runner Plate for Enhanced Flexibility
- A three-plate mold includes an extra plate (runner plate) compared to a two-plate mold.
- This plate allows for the separation of the runner system (the channels through which molten plastic flows) from the molded parts.
- The separation occurs automatically during the mold opening process, reducing manual intervention and improving efficiency.
-
Better Control Over Gate Locations
- The three-plate design enables gates (the entry points for molten plastic into the part cavity) to be located anywhere on the part, not just on the parting line.
- This flexibility is particularly useful for parts with complex geometries or those requiring gates in specific locations to minimize visible marks or defects.
-
Suitability for Multi-Cavity Molds
- Three-plate molds are ideal for multi-cavity setups, where multiple parts are produced in a single cycle.
- The runner system can be designed to distribute molten plastic evenly to all cavities, ensuring consistent part quality.
-
Automatic Runner and Part Separation
- In a three-plate mold, the runner system and the molded parts are ejected separately.
- This feature eliminates the need for manual separation, reducing labor costs and minimizing the risk of damage to the parts.
-
Improved Part Quality and Aesthetics
- The ability to place gates in optimal locations reduces the likelihood of defects such as weld lines, sink marks, or visible gate marks.
- This results in higher-quality parts with better surface finishes, which is critical for applications requiring aesthetic appeal.
-
Efficient Material Usage
- The three-plate mold design allows for a more compact runner system, reducing material waste.
- This efficiency is particularly beneficial for high-volume production, where even small reductions in material usage can lead to significant cost savings.
-
Versatility for Complex Part Designs
- Three-plate molds are better suited for producing parts with intricate designs or undercuts that would be challenging to mold with a two-plate design.
- The additional plate provides more space and flexibility for ejector pins, slides, and other components necessary for complex part geometries.
-
Reduced Cycle Times
- The automatic separation of runners and parts in a three-plate mold can lead to faster cycle times compared to two-plate molds, where manual separation may be required.
- Faster cycle times translate to higher production rates and lower manufacturing costs.
-
Cost-Effectiveness in High-Volume Production
- While three-plate molds are generally more expensive to design and manufacture than two-plate molds, their advantages in high-volume production often justify the initial investment.
- The reduced labor costs, material savings, and increased production efficiency make them a cost-effective choice for large-scale manufacturing.
-
Applications in Advanced Manufacturing
- Three-plate molds are commonly used in industries requiring high precision and complex part designs, such as automotive, medical devices, and consumer electronics.
- Their ability to produce high-quality parts with minimal post-processing makes them indispensable in these sectors.
In summary, the three-plate mold offers significant advantages over the two-plate mold, particularly in terms of flexibility, efficiency, and part quality. Its ability to handle complex designs, reduce material waste, and automate the separation of runners and parts makes it a superior choice for high-volume and precision-driven manufacturing processes. While the initial cost may be higher, the long-term benefits often outweigh the investment, making three-plate molds a preferred option for many industries.
Summary Table:
Advantage | Description |
---|---|
Additional Runner Plate | Enables automatic separation of runners and parts, improving efficiency. |
Better Gate Location Control | Allows gates to be placed anywhere on the part, reducing defects. |
Multi-Cavity Suitability | Ideal for producing multiple parts in a single cycle with consistent quality. |
Automatic Runner Separation | Eliminates manual separation, reducing labor costs and part damage. |
Improved Part Quality | Minimizes defects like weld lines and sink marks for better aesthetics. |
Efficient Material Usage | Compact runner system reduces material waste, saving costs. |
Versatility for Complex Designs | Supports intricate geometries and undercuts with added flexibility. |
Reduced Cycle Times | Faster production rates due to automatic processes. |
Cost-Effectiveness | Long-term savings in labor, materials, and efficiency justify higher initial costs. |
Advanced Manufacturing Applications | Widely used in automotive, medical, and electronics industries. |
Ready to enhance your injection molding process? Contact us today to learn how a three-plate mold can benefit your production!