The best crucible for melting depends on several factors, including the type of furnace, the specific alloy being melted, the melting temperature, and the operational requirements. Crucibles made from materials like silicon carbide, platinum, zirconium, or platinum alloys are commonly used due to their high melting points and chemical inertness. The choice of crucible material must align with the furnace's electrical characteristics, the metal's interaction with the crucible, and the crucible's resistance to thermal shock and corrosion. Additionally, factors such as furnace capacity, melting and holding temperatures, and operational processes like degassing or slag removal must be considered to ensure optimal performance and longevity of the crucible.
Key Points Explained:
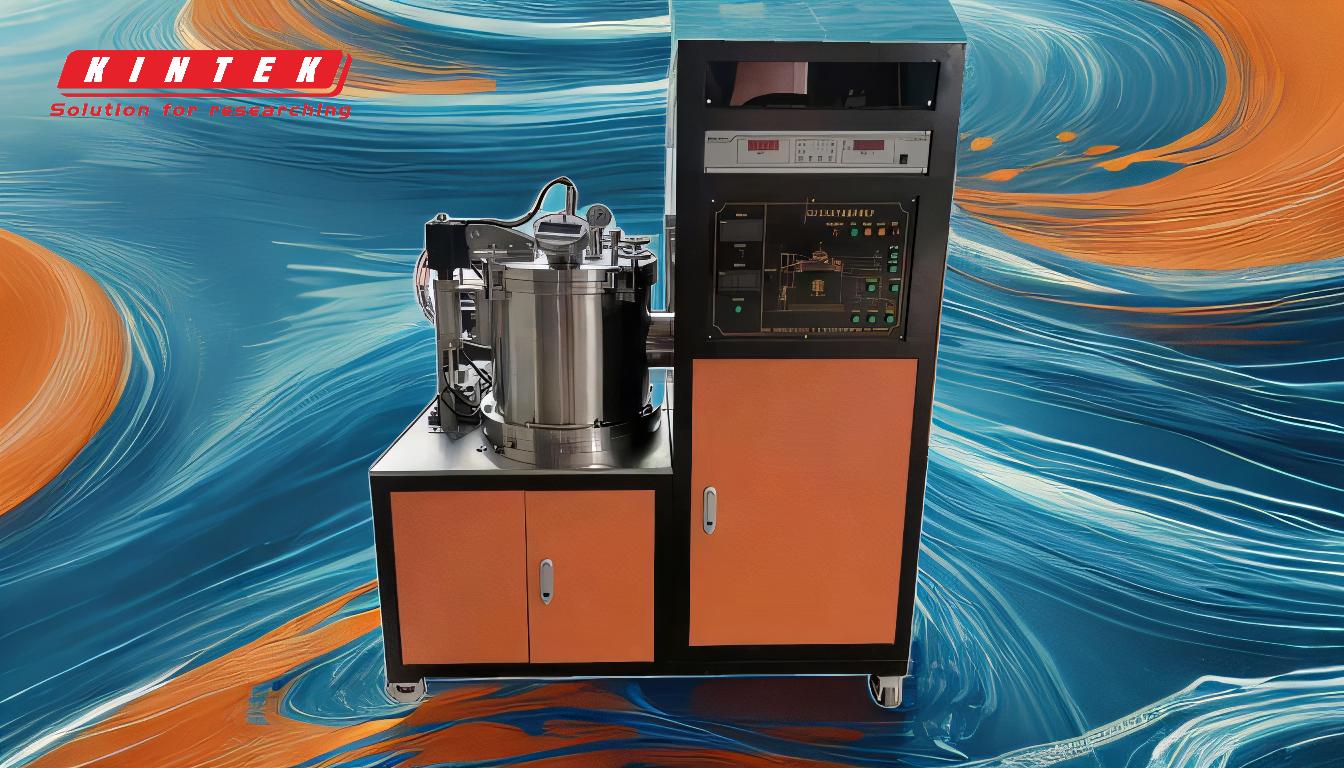
-
Crucible Material Selection:
- Silicon Carbide: Ideal for lower frequency induction furnaces and copper-based alloys due to its high thermal shock resistance.
- Platinum and Platinum Alloys: Suitable for high-temperature applications and scientific processes where contamination must be avoided.
- Zirconium: Used in scientific applications for its chemical stability and high melting point.
- Clay-based Crucibles: Often used in higher frequency induction furnaces due to their electrical resistivity.
-
Furnace Compatibility:
- The crucible's electrical resistivity must match the furnace's operating frequency to prevent overheating.
- Lower frequency furnaces may require crucibles with high silicon carbide content, while higher frequency furnaces may need high clay content.
-
Metal Alloy Considerations:
- The type of metal being melted determines the crucible's required characteristics, such as maximum temperature support and resistance to thermal shock or corrosion.
- For example, silicon carbide crucibles are preferred for melting copper-based alloys in fuel-fired furnaces.
-
Operational Requirements:
- Capacity and Dimensions: The crucible must fit the furnace and accommodate the required volume of metal.
- Melting and Holding Temperatures: The crucible must withstand the specific temperatures required for the melting process.
- Temperature Change Rates: The crucible should resist thermal shock from rapid temperature changes.
- Charging and Emptying Methods: The crucible design should facilitate easy charging and emptying of the metal.
- Fluxes and Additions: The crucible material should be compatible with any fluxes or additives used during melting.
- Degassing and Refining Processes: The crucible must withstand any degassing or refining processes without degradation.
- Slag or Dross Removal: The crucible should allow for efficient slag or dross removal.
- Avoiding Cross-Contamination: The crucible material should prevent contamination between different alloys.
-
Scientific Applications:
- Crucibles used in scientific applications must be made of inert materials like platinum or zirconium to avoid contaminating the analyte.
- They must withstand high temperatures and remain chemically stable to ensure accurate results in analytical chemistry and sample preparation.
-
Thermal and Chemical Resistance:
- The crucible must resist thermal shock, especially in applications with rapid temperature changes.
- It should also resist chemical reactions with the metal being melted to prevent contamination and degradation.
By carefully considering these factors, you can select the best crucible for your specific melting application, ensuring optimal performance and longevity.
Summary Table:
Factor | Key Considerations |
---|---|
Crucible Material | - Silicon Carbide: High thermal shock resistance, ideal for copper alloys. |
- Platinum/Platinum Alloys: High-temperature, contamination-free applications. | |
- Zirconium: Chemically stable, suitable for scientific processes. | |
- Clay-based: High electrical resistivity, suited for higher frequency furnaces. | |
Furnace Compatibility | - Match crucible resistivity with furnace frequency to prevent overheating. |
Metal Alloy | - Choose crucible based on alloy type, temperature, and corrosion resistance. |
Operational Requirements | - Consider capacity, temperature tolerance, charging methods, and slag removal. |
Scientific Applications | - Use inert materials like platinum or zirconium to avoid contamination. |
Thermal/Chemical Resistance | - Ensure resistance to thermal shock and chemical reactions for longevity. |
Need help selecting the perfect crucible for your melting needs? Contact our experts today for personalized advice!