The capacity of a rotary furnace depends on its design, size, and intended application. Rotary furnaces are versatile and widely used in industries such as metallurgy, ceramics, and chemical processing. Their capacity is influenced by factors like the furnace's internal volume, material handling mechanisms, and the ability to adjust tilt angles and rotational speeds for optimal performance. These furnaces are designed to handle a variety of materials, including powders, granules, and solids, with features like uniform heating and precise temperature control ensuring efficient and consistent results.
Key Points Explained:
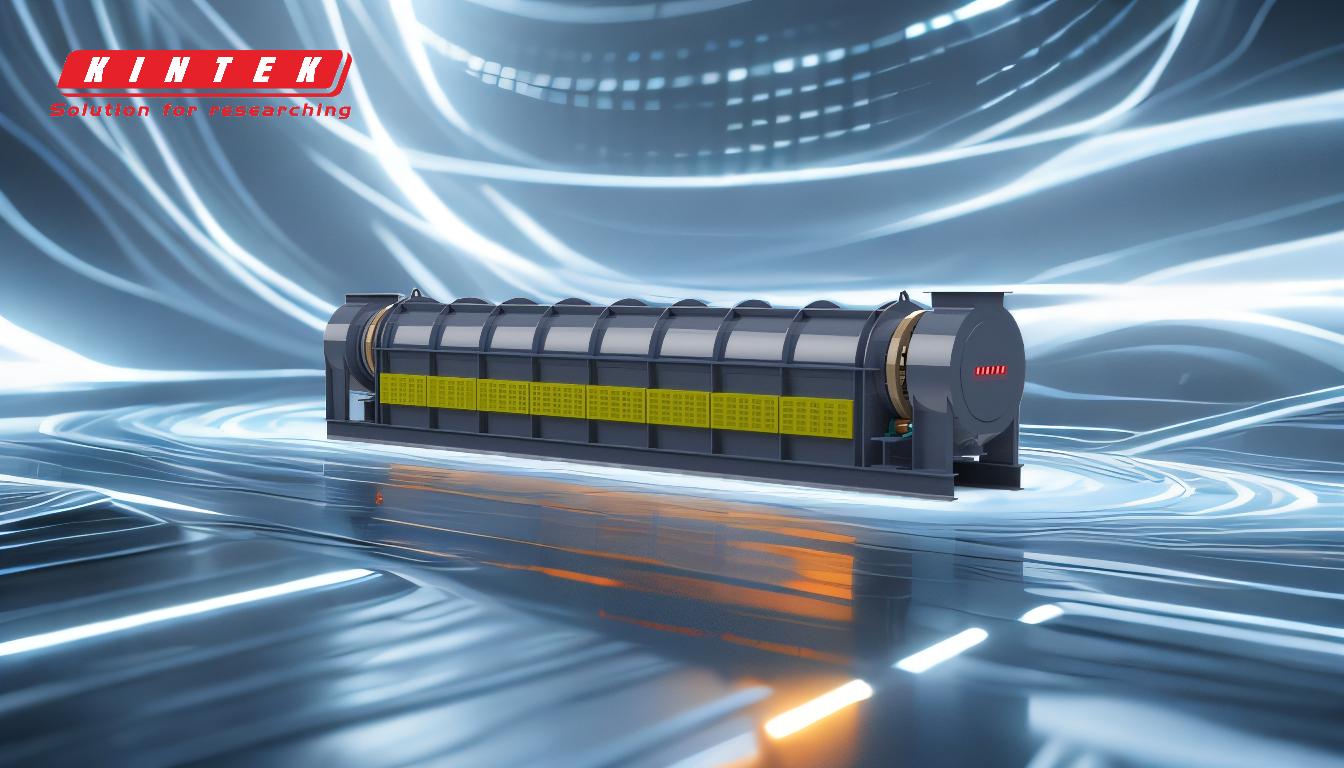
-
Components and Design of a Rotary Furnace
- A rotating furnace consists of key components such as the furnace body, lining, drive gear, and internal heat source. These elements work together to ensure efficient operation and durability.
- The furnace's design allows for 360-degree rotation and adjustable tilt angles (typically between 0 and 30 degrees), which enhances material handling and operational flexibility.
-
Material Loading Mechanisms
- Materials are loaded into the furnace through a port at the head. Dry blends are fed using mechanical feeders, while liquid or slurry blends can be poured or injected through nozzles.
- This flexibility in loading methods accommodates a wide range of materials, including powders, granules, and solids, making the furnace suitable for diverse industrial applications.
-
Capacity Factors
- The capacity of a rotary furnace is determined by its internal volume, which varies depending on the furnace's size and design. Larger furnaces can handle greater quantities of material per batch.
- The ability to adjust the tilt angle and rotational speed allows operators to optimize material flow and residence time, further influencing the furnace's throughput and capacity.
-
Heating and Temperature Control
- Rotary furnaces provide uniform heating due to their rotational motion, which ensures thorough mixing of materials and minimizes temperature gradients.
- Advanced temperature control systems, often computer-based, enable precise regulation of heating conditions, improving both process efficiency and product quality.
-
Applications and Versatility
- The wide scope of applications for rotary furnaces includes metallurgical processes, ceramic production, and chemical processing. Their ability to handle various material types and sizes makes them indispensable in many industries.
- The combination of adjustable tilt angles, rotational capabilities, and precise temperature control ensures that rotary furnaces can meet the specific requirements of different processes and materials.
In summary, the capacity of a rotary furnace is not a fixed value but rather a function of its design, operational parameters, and the specific application. By leveraging its adjustable features and advanced control systems, a rotary furnace can be tailored to achieve optimal performance and throughput for a wide range of industrial processes.
Summary Table:
Factor | Description |
---|---|
Internal Volume | Determines the quantity of material per batch; larger furnaces handle more. |
Tilt Angle & Speed | Adjustable settings optimize material flow and residence time for better output. |
Material Handling | Supports powders, granules, solids, and liquids for versatile applications. |
Heating & Control | Uniform heating and precise temperature control ensure consistent results. |
Applications | Ideal for metallurgy, ceramics, and chemical processing industries. |
Ready to optimize your industrial processes? Contact us today to find the perfect rotary furnace for your needs!