The chemical deposition method for catalyst preparation, particularly through chemical vapor deposition (CVD), is a sophisticated process used to create thin films or coatings on substrates. This method involves the transformation of gaseous reactants into solid materials on a substrate surface through chemical reactions. The process is highly controlled and involves multiple steps, including the transport of reactants, adsorption, surface reactions, and the removal of by-products. CVD is widely used in industries for creating high-quality, uniform coatings, and it plays a crucial role in catalyst preparation due to its precision and ability to produce materials with specific properties.
Key Points Explained:
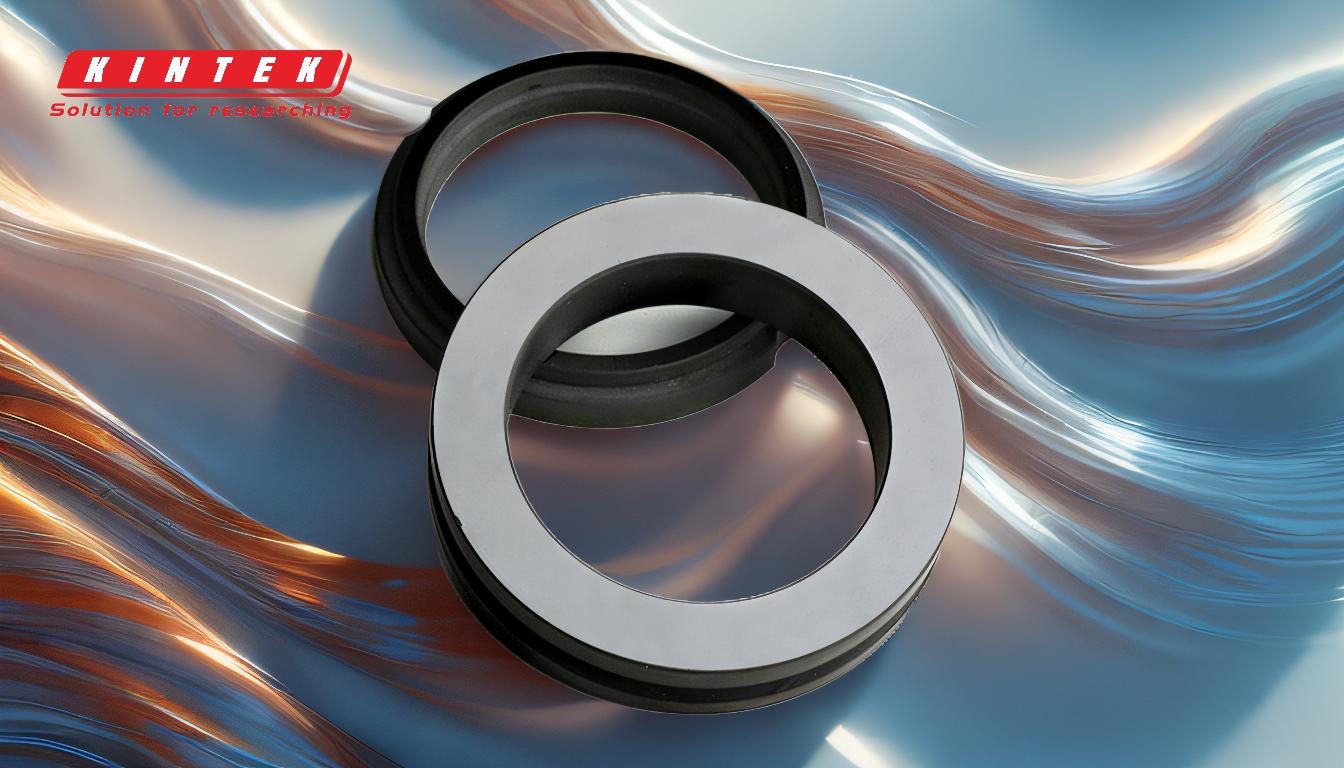
-
Evaporation and Vaporization of Reactants:
- The first step in the CVD process involves the evaporation of a volatile compound that contains the substance to be deposited. This compound is typically in a liquid or solid state and is heated to form a vapor. The vaporized compound is then transported into the reaction chamber where the deposition will occur.
-
Thermal Decomposition and Chemical Reactions:
- Once the vaporized compound reaches the reaction chamber, it undergoes thermal decomposition due to the high temperatures. This decomposition breaks the compound into its constituent atoms and molecules. Additionally, the vapor may react with other gases, vapors, or liquids present in the chamber. These reactions are crucial as they form the reactive species that will eventually deposit on the substrate.
-
Transport of Reactants to the Substrate:
- The reactive species formed in the previous step need to reach the substrate surface. This is achieved through convection or diffusion processes. The reactants move through the gas phase and traverse the boundary layer that exists near the substrate surface. Efficient transport is essential to ensure a uniform deposition.
-
Adsorption and Surface Reactions:
- Upon reaching the substrate, the reactive species adsorb onto its surface. This adsorption can be physical or chemical, depending on the nature of the interactions between the species and the substrate. Following adsorption, heterogeneous surface-catalyzed reactions occur, leading to the formation of a solid film. These reactions are often catalyzed by the substrate itself or by pre-deposited catalyst layers.
-
Nucleation and Growth of the Film:
- The adsorbed species diffuse across the substrate surface to find suitable growth sites. Once at these sites, nucleation occurs, leading to the formation of small clusters of the deposited material. These clusters grow and coalesce to form a continuous film. The growth process is influenced by factors such as temperature, pressure, and the nature of the substrate.
-
Desorption and Removal of By-products:
- As the film grows, volatile by-products are formed. These by-products desorb from the substrate surface and diffuse back through the boundary layer into the main gas stream. The by-products are then transported out of the reaction chamber via convection and diffusion processes. Efficient removal of these by-products is crucial to maintain the quality of the deposited film and to prevent contamination.
-
Control and Optimization of the CVD Process:
- The entire CVD process is highly dependent on precise control of various parameters such as temperature, pressure, gas flow rates, and the composition of the reactant gases. Optimization of these parameters is essential to achieve the desired film properties, such as thickness, uniformity, and chemical composition. Advanced CVD techniques, such as plasma-enhanced CVD (PECVD) and atomic layer deposition (ALD), offer even greater control and are used for more specialized applications.
In summary, the chemical deposition method for catalyst preparation via CVD is a multi-step process that involves the careful control of chemical reactions and physical processes to deposit high-quality thin films on substrates. This method is invaluable in the production of catalysts, as it allows for the precise engineering of material properties at the nanoscale, leading to enhanced catalytic performance.
Summary Table:
Step | Description |
---|---|
Evaporation and Vaporization | Volatile compounds are heated to form vapor for deposition. |
Thermal Decomposition | Vaporized compounds decompose into reactive species under high temperatures. |
Transport of Reactants | Reactive species are transported to the substrate via convection or diffusion. |
Adsorption and Surface Reactions | Species adsorb onto the substrate, forming a solid film through reactions. |
Nucleation and Growth | Adsorbed species form clusters that grow into a continuous film. |
Desorption and By-product Removal | Volatile by-products are removed to maintain film quality. |
Process Control and Optimization | Precise control of parameters ensures desired film properties. |
Learn how CVD can revolutionize your catalyst preparation—contact our experts today!