Chemical vapor deposition (CVD) of silicon carbide (SiC) is a process used to create high-purity SiC coatings or films on substrates. This technique involves the reaction of gaseous precursors, such as silane (SiH4) and methane (CH4), in a controlled environment to deposit a thin layer of SiC onto a substrate. The process is widely used in industries requiring materials with exceptional thermal, mechanical, and chemical properties, such as semiconductor manufacturing, aerospace, and industrial heating applications. SiC's unique properties, including high thermal conductivity, resistance to thermal shock, and excellent chemical stability, make it ideal for use in harsh environments. For instance, silicon carbide crucibles are often manufactured using CVD to ensure durability and resistance to extreme temperatures and corrosive substances.
Key Points Explained:
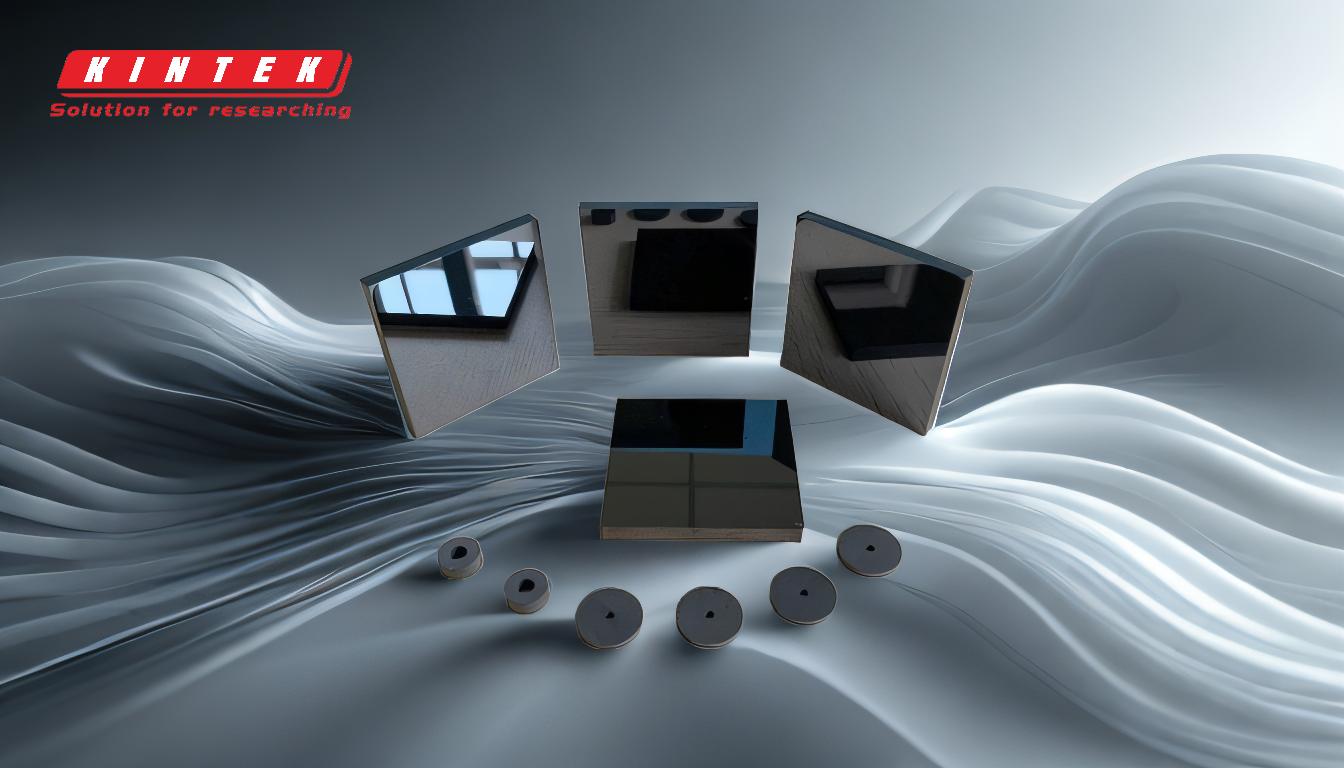
-
Definition of Chemical Vapor Deposition (CVD):
- CVD is a process where a thin solid film is deposited onto a substrate through the reaction of gaseous precursors in a controlled environment. Unlike physical vapor deposition (PVD), which relies on physical processes like evaporation or sputtering, CVD involves chemical reactions at the surface of the substrate. This method is particularly useful for creating high-purity and high-performance materials like silicon carbide.
-
Applications of CVD Silicon Carbide:
- CVD silicon carbide is extensively used in semiconductor processing, such as in rapid thermal processing (RTP) and oxide etch chamber components. Its ability to withstand high-energy plasmas and thermal shock makes it indispensable in these applications.
- Beyond semiconductors, CVD SiC is also used in the production of heating elements, rocket engine components, and desulfurization nozzles for thermal power plants. Its resistance to extreme temperatures and corrosive environments makes it a preferred material in these industries.
-
Properties of Silicon Carbide:
- Thermal Stability: SiC can operate at temperatures up to 1625°C, making it ideal for high-temperature applications like industrial heating elements and ceramic firing.
- Chemical Resistance: SiC is highly resistant to corrosive gases and liquids, which is why it is used in desulfurization nozzles and other applications exposed to harsh chemicals.
- Mechanical Strength: SiC's high mechanical strength and hardness make it suitable for use in demanding environments, such as in rocket engines and pump components.
-
Role of Silicon Carbide Crucibles in CVD:
- Silicon carbide crucibles are often used in CVD processes due to their ability to withstand the high temperatures and corrosive environments typical of these processes. These crucibles are essential for holding the substrate and precursors during the deposition process, ensuring that the resulting SiC film is of high quality and purity.
-
Advantages of CVD SiC in Industrial Applications:
- Durability: CVD SiC coatings are highly durable and can withstand extreme conditions, making them suitable for long-term use in industrial settings.
- Precision: The CVD process allows for precise control over the thickness and composition of the SiC film, which is crucial for applications in the semiconductor industry.
- Versatility: CVD SiC can be used in a wide range of applications, from electronic components to industrial heating elements, due to its versatile properties.
In summary, the chemical vapor deposition of silicon carbide is a critical process for producing high-performance materials used in various industries. The unique properties of SiC, combined with the precision and versatility of the CVD process, make it an essential technology for applications requiring materials that can withstand extreme conditions. For more information on the use of silicon carbide in specific applications, such as silicon carbide crucibles, refer to the linked topic.
Summary Table:
Key Aspect | Details |
---|---|
Process | Chemical reaction of gaseous precursors (e.g., silane, methane) in a controlled environment. |
Applications | Semiconductor manufacturing, aerospace, industrial heating, rocket engines. |
Properties | High thermal stability (up to 1625°C), chemical resistance, mechanical strength. |
Advantages | Durability, precision, versatility for extreme environments. |
Role of SiC Crucibles | Essential for CVD processes due to high-temperature and corrosion resistance. |
Interested in leveraging CVD silicon carbide for your industrial needs? Contact us today to learn more!