Chemical Vapor Deposition (CVD) and Physical Vapor Deposition (PVD) are two widely used thin-film deposition techniques, each with distinct advantages and limitations. CVD involves chemical reactions at high temperatures, making it unsuitable for temperature-sensitive materials but offering excellent material utilization and cost efficiency. PVD, on the other hand, operates at lower temperatures, making it ideal for sensitive substrates, though it may involve higher material waste. Both methods have unique operational complexities, such as precursor handling in CVD and plasma generation in PVD. Understanding their differences is crucial for selecting the appropriate technique based on material properties, application requirements, and cost considerations.
Key Points Explained:
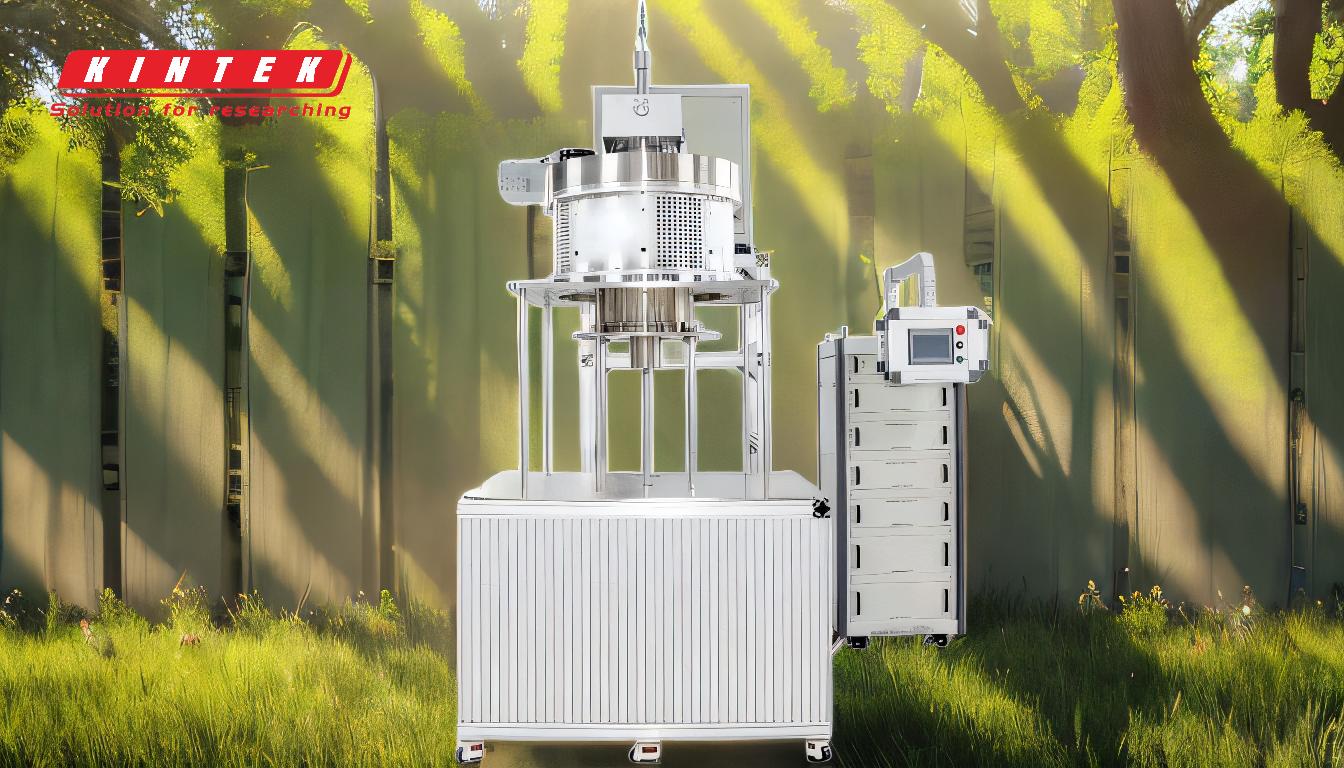
-
Temperature Sensitivity:
- CVD: Requires high temperatures (up to 900 °C or higher), making it unsuitable for temperature-sensitive materials like certain polymers or low-melting-point metals. For example, diamond nanoparticle growth in CVD requires substrate temperatures of around 1100 K.
- PVD: Operates at lower temperatures, making it suitable for temperature-sensitive materials. This is a significant advantage for applications involving delicate substrates.
-
Material Utilization and Waste:
- CVD: Offers better material utilization since only the heated area is coated. This reduces material waste and can be further enhanced using computer-controlled lasers for selective heating.
- PVD: May involve higher material waste due to the nature of the deposition process, such as sputtering or evaporation, where not all material is efficiently deposited onto the substrate.
-
Cost Efficiency:
- CVD: Generally more cost-efficient for surface coating applications due to lower operational costs and better material utilization.
- PVD: May involve higher costs due to the complexity of equipment and processes, such as plasma generation in sputtering or electron-beam evaporation.
-
Precursor and Chemical Handling:
- CVD: Requires chemical precursors, which can be expensive, hazardous, or unstable. Specialized equipment is needed for precursor conditioning and dosing. Additionally, hazardous residues and fumes must be managed and removed from the exhaust.
- PVD: Does not involve chemical precursors, reducing the need for complex chemical handling and disposal systems.
-
Deposition Methods:
- CVD: Includes methods like atmospheric thermal CVD, which allows for uniform and adherent films at relatively low temperatures. However, it lacks highly volatile, nontoxic, and nonpyrophoric precursors.
- PVD: Encompasses methods such as sputtering, thermal evaporation, and electron-beam evaporation. Sputtering involves plasma generation under high voltage, while thermal and electron-beam evaporation use evaporation processes to deposit thin films.
-
Operational Complexity:
- CVD: Easy to operate and does not require a complicated setup. However, it has thermal constraints, such as high energy costs for heating the gas phase and difficulties in depositing onto low melting point polymers.
- PVD: Involves more complex processes, such as plasma generation in sputtering or precise control of evaporation rates in thermal and electron-beam evaporation.
-
Film Quality and Properties:
- CVD: Produces high-quality, uniform films with excellent adhesion. However, incomplete decomposition of precursors can leave undesirable impurities in the deposited material.
- PVD: Offers good film quality but may require more precise control over deposition parameters to achieve uniformity and adhesion comparable to CVD.
-
Application Suitability:
- CVD: Ideal for applications requiring high-temperature stability and excellent material utilization, such as semiconductor manufacturing or protective coatings.
- PVD: Better suited for applications involving temperature-sensitive materials or where precise control over film thickness and properties is critical, such as optical coatings or decorative finishes.
By understanding these key differences, one can make an informed decision on whether to use CVD or PVD based on specific application requirements, material properties, and cost considerations.
Summary Table:
Aspect | CVD | PVD |
---|---|---|
Temperature | High temperatures (up to 900°C+), unsuitable for sensitive materials. | Lower temperatures, ideal for temperature-sensitive substrates. |
Material Utilization | Better utilization, reduced waste, selective heating possible. | Higher material waste due to sputtering or evaporation processes. |
Cost Efficiency | More cost-efficient for surface coatings. | Higher costs due to complex equipment and processes. |
Chemical Handling | Requires hazardous chemical precursors and specialized equipment. | No chemical precursors, simpler handling. |
Film Quality | High-quality, uniform films with excellent adhesion. | Good quality, requires precise control for uniformity and adhesion. |
Applications | Ideal for high-temperature stability and semiconductor manufacturing. | Best for temperature-sensitive materials and optical/decorative coatings. |
Need help choosing between CVD and PVD for your project? Contact our experts today for personalized advice!