Compression molding is a widely used method for processing plastic materials, particularly for thermosetting plastics and some thermoplastics. It involves placing a pre-measured amount of plastic material into a heated mold cavity, which is then compressed under pressure to shape the material into the desired form. The process relies on heat and pressure to soften the plastic, allowing it to flow and fill the mold cavity. Excess material, known as flash, is often produced and must be removed after the molding process. This method is suitable for producing large, relatively simple parts with consistent quality and is commonly used in industries such as automotive, aerospace, and consumer goods.
Key Points Explained:
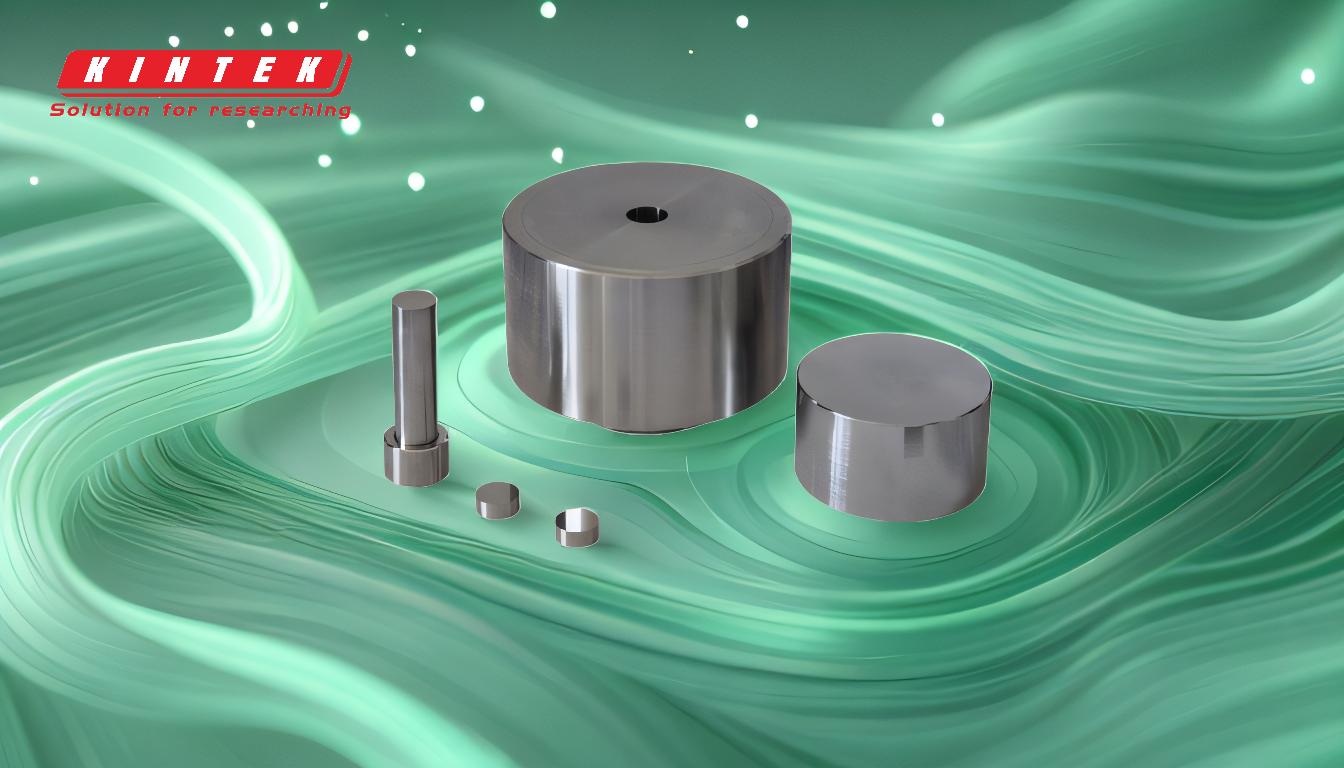
-
Overview of Compression Molding:
- Compression molding is a manufacturing process used to shape plastic materials by applying heat and pressure.
- It is particularly suitable for thermosetting plastics, which harden permanently when heated, and some thermoplastics.
- The process is ideal for producing large, flat, or moderately complex parts with high strength and durability.
-
Steps in the Compression Molding Process:
- Material Preparation: A pre-measured amount of plastic material, often in the form of pellets, powder, or preforms, is placed into the mold cavity.
- Mold Heating: The mold is heated to a specific temperature to soften the plastic material, making it pliable and ready to flow.
- Mold Closure: The mold is closed, and pressure is applied to force the softened plastic to conform to the shape of the mold cavity.
- Curing: For thermosetting plastics, the material undergoes a chemical reaction (curing) that hardens it into its final shape.
- Cooling and Ejection: The mold is cooled (for thermoplastics) or allowed to cool naturally, and the finished part is ejected from the mold.
-
Role of Heat and Pressure:
- Heat softens the plastic material, allowing it to flow and fill the mold cavity.
- Pressure ensures that the material fully conforms to the mold's shape and eliminates air pockets or voids.
- The combination of heat and pressure is critical for achieving uniform density and strength in the final product.
-
Handling Excess Material (Flash):
- During the molding process, excess material, known as flash, may flow out of the mold cavity through specially designed grooves or vents.
- Flash is typically trimmed off after the part is ejected from the mold, either manually or using automated trimming equipment.
- Proper management of flash is essential to ensure the dimensional accuracy and surface finish of the final product.
-
Advantages of Compression Molding:
- Cost-Effective for Large Parts: The process is economical for producing large, flat, or moderately complex parts.
- Material Efficiency: Minimal material waste occurs, as excess flash can often be recycled.
- High Strength and Durability: Compression-molded parts exhibit excellent mechanical properties, making them suitable for demanding applications.
- Versatility: It can be used with a wide range of materials, including thermosetting plastics, rubber, and some thermoplastics.
-
Applications of Compression Molding:
- Automotive Industry: Used for manufacturing components such as dashboards, bumpers, and interior trim.
- Aerospace Industry: Produces lightweight, high-strength parts for aircraft interiors and structural components.
- Consumer Goods: Commonly used for making electrical enclosures, appliance housings, and kitchenware.
- Industrial Components: Suitable for producing seals, gaskets, and other rubber or plastic parts.
-
Limitations of Compression Molding:
- Longer Cycle Times: Compared to other molding methods like injection molding, compression molding can have slower cycle times due to the need for heating and curing.
- Limited Complexity: It is less suitable for highly complex or intricate part designs.
- Material Restrictions: While versatile, it is primarily used for thermosetting plastics and certain thermoplastics, limiting its applicability for other materials.
-
Comparison with Other Molding Methods:
- Injection Molding: Faster cycle times and better suited for complex shapes, but typically more expensive for large parts.
- Transfer Molding: Similar to compression molding but uses a plunger to transfer material into the mold, allowing for more precise control over material flow.
- Blow Molding: Used for hollow parts like bottles and containers, but not suitable for solid parts.
By understanding the compression molding process, its advantages, and its limitations, purchasers of equipment and consumables can make informed decisions about whether this method is suitable for their specific manufacturing needs. The process offers a balance of cost-effectiveness, material efficiency, and part quality, making it a valuable option for many industries.
Summary Table:
Aspect | Details |
---|---|
Process | Uses heat and pressure to shape plastic materials into desired forms. |
Materials | Thermosetting plastics, rubber, and some thermoplastics. |
Advantages | Cost-effective, material-efficient, high strength, and versatile. |
Applications | Automotive, aerospace, consumer goods, and industrial components. |
Limitations | Longer cycle times, limited complexity, and material restrictions. |
Comparison | Slower than injection molding but more economical for large parts. |
Discover how compression molding can benefit your production—contact us today for expert advice!