Chemical vapor deposition (CVD) is a versatile and widely used technique for depositing thin films and coatings on substrates through chemical reactions in the vapor phase. The process involves introducing precursor gases into a reaction chamber containing a heated substrate. These gases react or decompose on the substrate's surface, forming a solid material layer. CVD is known for producing high-quality, pure, and uniform coatings, making it essential in industries such as semiconductors, optoelectronics, and materials science. The process operates under controlled conditions, often under vacuum, to ensure precise deposition and minimize impurities. CVD is cost-effective and scalable, enabling its use in both research and industrial applications.
Key Points Explained:
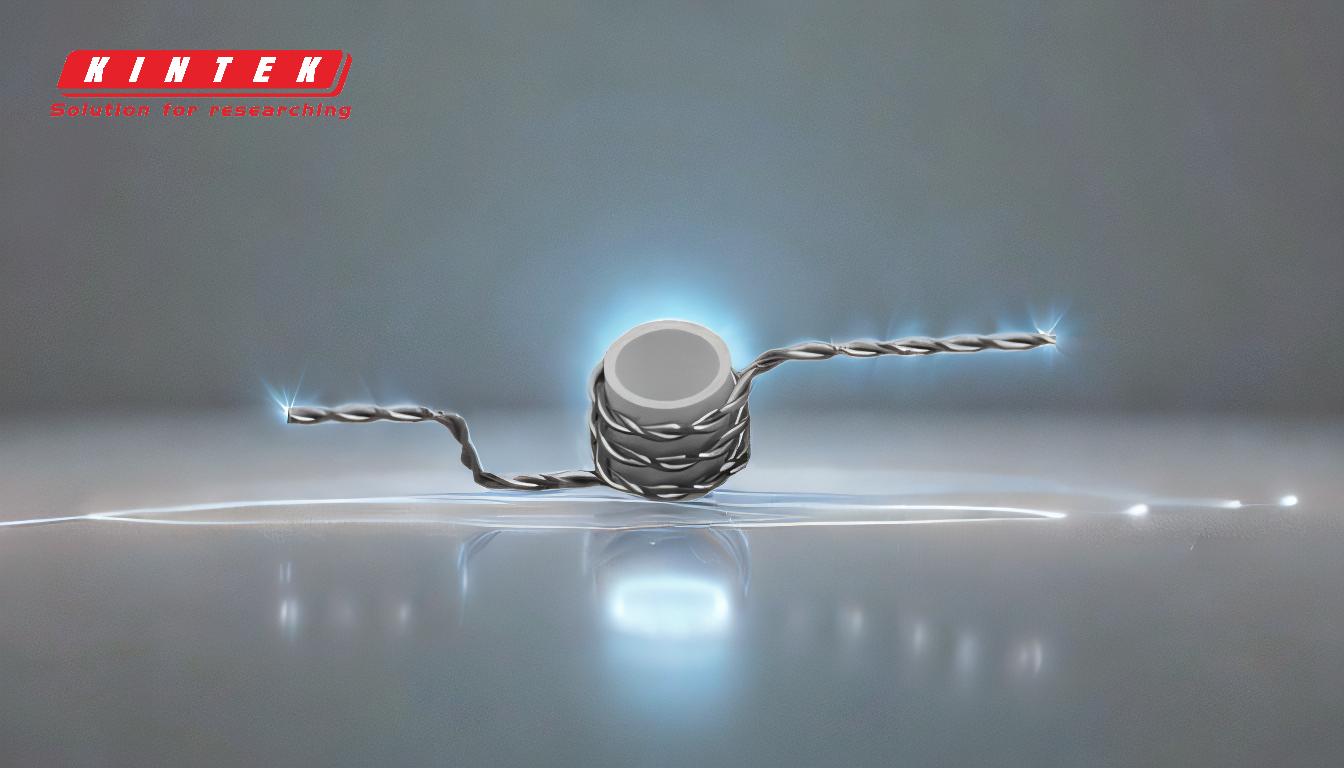
-
Basic Principle of CVD:
- CVD relies on chemical reactions between gaseous precursors and a heated substrate. The precursor gases flow into a reaction chamber and undergo reactions (such as decomposition or composition) on the substrate's surface, leading to the formation of a solid thin film.
- The process is driven by thermal energy, which activates the chemical reactions necessary for deposition.
-
Components of a CVD System:
- Reaction Chamber: A controlled environment where the deposition occurs. It is often maintained under vacuum or low-pressure conditions to ensure uniform deposition and minimize contamination.
- Precursor Gases: These are the source materials in gaseous form that react to form the desired coating. Common precursors include volatile compounds of metals, carbon, or silicon.
- Substrate: The material on which the thin film is deposited. The substrate is heated to facilitate the chemical reactions and ensure proper adhesion of the deposited material.
- Gas Flow System: Controls the introduction and removal of gases, ensuring a steady flow of precursors and by-products.
- Heating System: Maintains the substrate at the required temperature for the reactions to occur.
-
Types of CVD Processes:
- Atmospheric Pressure CVD (APCVD): Operates at atmospheric pressure, suitable for large-scale production but may result in less uniform coatings.
- Low-Pressure CVD (LPCVD): Conducted under reduced pressure, providing better uniformity and control over film properties.
- Plasma-Enhanced CVD (PECVD): Uses plasma to enhance the chemical reactions, allowing deposition at lower temperatures.
- Metal-Organic CVD (MOCVD): Utilizes metal-organic precursors for depositing compound semiconductors and other advanced materials.
-
Applications of CVD:
- Semiconductors: CVD is widely used to deposit thin films of silicon, silicon dioxide, and other materials in semiconductor device fabrication.
- Optoelectronics: Used for producing coatings and films in devices like LEDs and solar cells.
- Protective Coatings: CVD can create hard, wear-resistant coatings for tools and components.
- Graphene Production: CVD is a leading method for synthesizing high-quality graphene on a large scale.
- Polymers and Composites: CVD is employed to fabricate thin films of polymeric materials and composite coatings.
-
Advantages of CVD:
- High Purity: The process produces highly pure materials due to controlled gas-phase reactions.
- Uniformity: CVD ensures even deposition across the substrate, even on complex geometries.
- Versatility: It can deposit a wide range of materials, including metals, ceramics, and polymers.
- Scalability: CVD is suitable for both small-scale research and large-scale industrial production.
-
Challenges and Considerations:
- Precursor Selection: Choosing the right precursor gases is critical for achieving the desired material properties.
- Temperature Control: Precise temperature management is necessary to ensure proper reaction kinetics and film quality.
- By-Product Management: Volatile by-products must be efficiently removed to prevent contamination and ensure consistent deposition.
In summary, chemical vapor deposition is a highly effective and versatile technique for producing high-quality thin films and coatings. Its ability to deposit a wide range of materials with precision and uniformity makes it indispensable in modern technology and manufacturing.
Summary Table:
Aspect | Details |
---|---|
Basic Principle | Chemical reactions between gaseous precursors and a heated substrate. |
Key Components | Reaction chamber, precursor gases, substrate, gas flow system, heating system. |
Types of CVD | APCVD, LPCVD, PECVD, MOCVD. |
Applications | Semiconductors, optoelectronics, protective coatings, graphene production. |
Advantages | High purity, uniformity, versatility, scalability. |
Challenges | Precursor selection, temperature control, by-product management. |
Discover how CVD can revolutionize your thin film production—contact our experts today!