The cost of an induction furnace varies significantly depending on its type, capacity, power rating, and additional features. Generally, smaller induction furnaces for laboratory or small-scale industrial use can cost anywhere from a few thousand dollars to tens of thousands of dollars. Larger industrial-grade induction furnaces, especially those using advanced technologies like IGBT (Insulated Gate Bipolar Transistor), can range from $50,000 to over $500,000. Factors influencing the price include the furnace's efficiency, automation level, cooling systems, and the quality of materials used in construction. Additionally, operational costs such as power consumption, maintenance, and consumables should also be considered when evaluating the overall investment.
Key Points Explained:
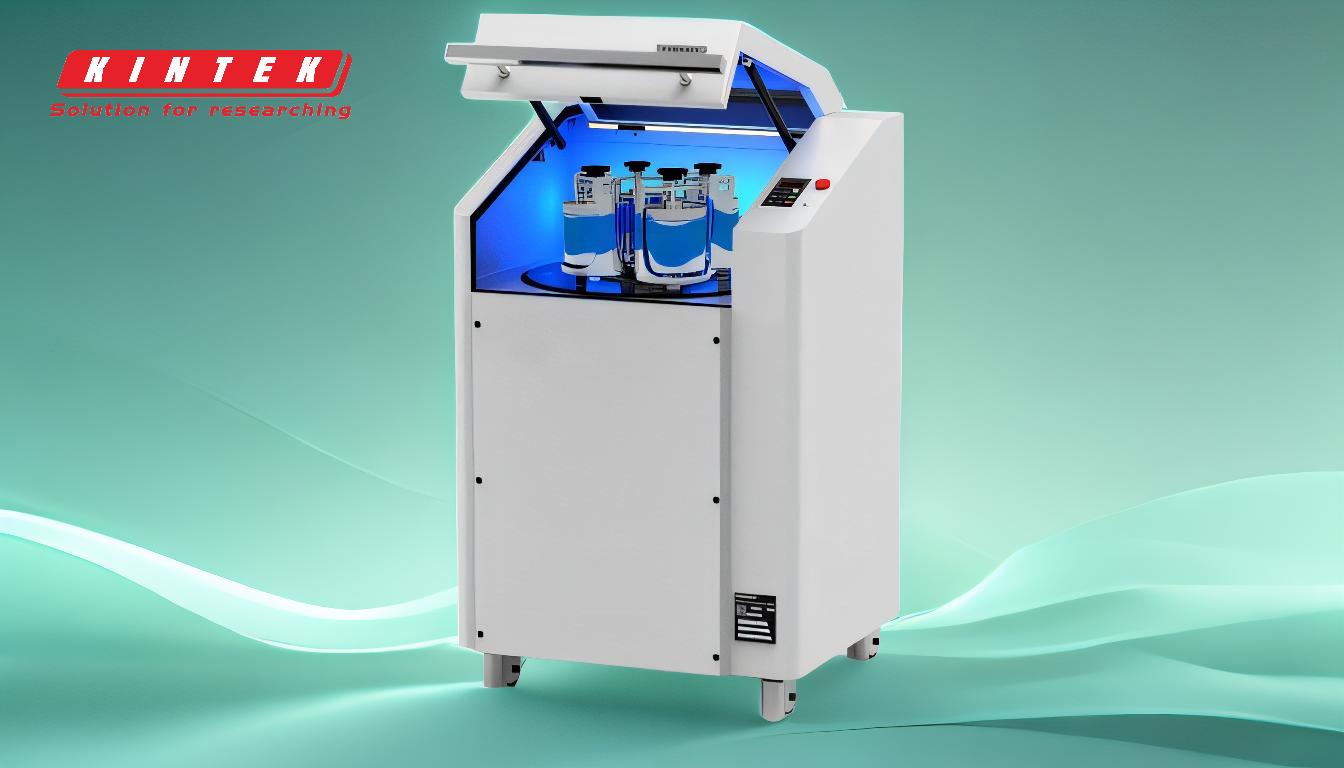
-
Types of Induction Furnaces:
- Induction furnaces come in various types, including coreless and channel furnaces. Coreless furnaces are more common for melting metals, while channel furnaces are often used for holding and superheating molten metal.
- The type of furnace significantly impacts the cost, with coreless furnaces generally being more expensive due to their versatility and higher melting efficiency.
-
Capacity and Power Rating:
- The capacity of the furnace, measured in kilograms or tons of metal it can melt, directly affects the price. Larger capacity furnaces are more expensive.
- Power rating, measured in kilowatts (kW), also plays a crucial role. Higher power ratings allow for faster melting but increase both the initial cost and operational expenses.
-
Technology and Efficiency:
- Modern induction furnaces often use IGBT technology, which offers higher efficiency, better control, and reduced energy consumption compared to older SCR (Silicon Controlled Rectifier) technology.
- IGBT induction furnaces are generally more expensive upfront but can lead to significant savings in energy costs over time.
-
Automation and Control Systems:
- Advanced automation and control systems, such as PLC (Programmable Logic Controller) and HMI (Human-Machine Interface), add to the cost but improve operational efficiency and reduce labor costs.
- Fully automated systems can adjust melting parameters in real-time, ensuring optimal performance and reducing the risk of human error.
-
Cooling Systems:
- Induction furnaces require efficient cooling systems to manage the heat generated during operation. Water-cooled systems are common and can add to the overall cost.
- The quality and capacity of the cooling system are critical for maintaining the furnace's longevity and performance.
-
Material Quality and Construction:
- The materials used in the construction of the furnace, such as the quality of the refractory lining and the robustness of the steel structure, influence the price.
- High-quality materials ensure better durability and lower maintenance costs, justifying a higher initial investment.
-
Operational Costs:
- Beyond the initial purchase price, operational costs such as electricity, maintenance, and consumables (e.g., refractory materials) must be considered.
- Energy-efficient models, while more expensive initially, can lead to lower operational costs over the furnace's lifespan.
-
Market and Supplier Variations:
- Prices can vary widely depending on the supplier, region, and market conditions. It's essential to obtain multiple quotes and consider the supplier's reputation and after-sales service.
- Customization options, such as specific melting capacities or additional features, can also affect the final price.
In summary, the cost of an induction furnace is influenced by a combination of factors, including its type, capacity, technology, automation level, and operational efficiency. While the initial investment can be substantial, especially for high-capacity, IGBT-based models, the long-term benefits in terms of energy savings and operational efficiency often justify the expense.
Summary Table:
Factor | Impact on Cost |
---|---|
Type | Coreless furnaces are more expensive due to higher versatility and efficiency. |
Capacity | Larger capacity furnaces cost more, with prices scaling with melting capacity. |
Power Rating | Higher power ratings increase both initial and operational costs. |
Technology | IGBT-based furnaces are pricier but offer energy savings over time. |
Automation | Advanced control systems add to the cost but improve efficiency. |
Cooling Systems | High-quality cooling systems are essential and increase the overall price. |
Material Quality | Durable materials justify higher upfront costs with lower maintenance expenses. |
Operational Costs | Energy-efficient models reduce long-term expenses despite higher initial costs. |
Market Variations | Prices vary by supplier, region, and customization options. |
Ready to find the perfect induction furnace for your needs? Contact us today for expert advice and a customized quote!