Chemical Vapor Deposition (CVD) is a widely used method for growing high-quality, high-performance solid materials, particularly thin films, in various industries such as semiconductors, optics, and tool coatings. The process involves the chemical reaction of gaseous precursors at elevated temperatures to form a solid material on a substrate. CVD is known for its ability to produce uniform and conformal coatings, even on complex geometries like deep holes and internal walls. Below, we explore the CVD method in detail, focusing on its principles, types, and applications.
Key Points Explained:
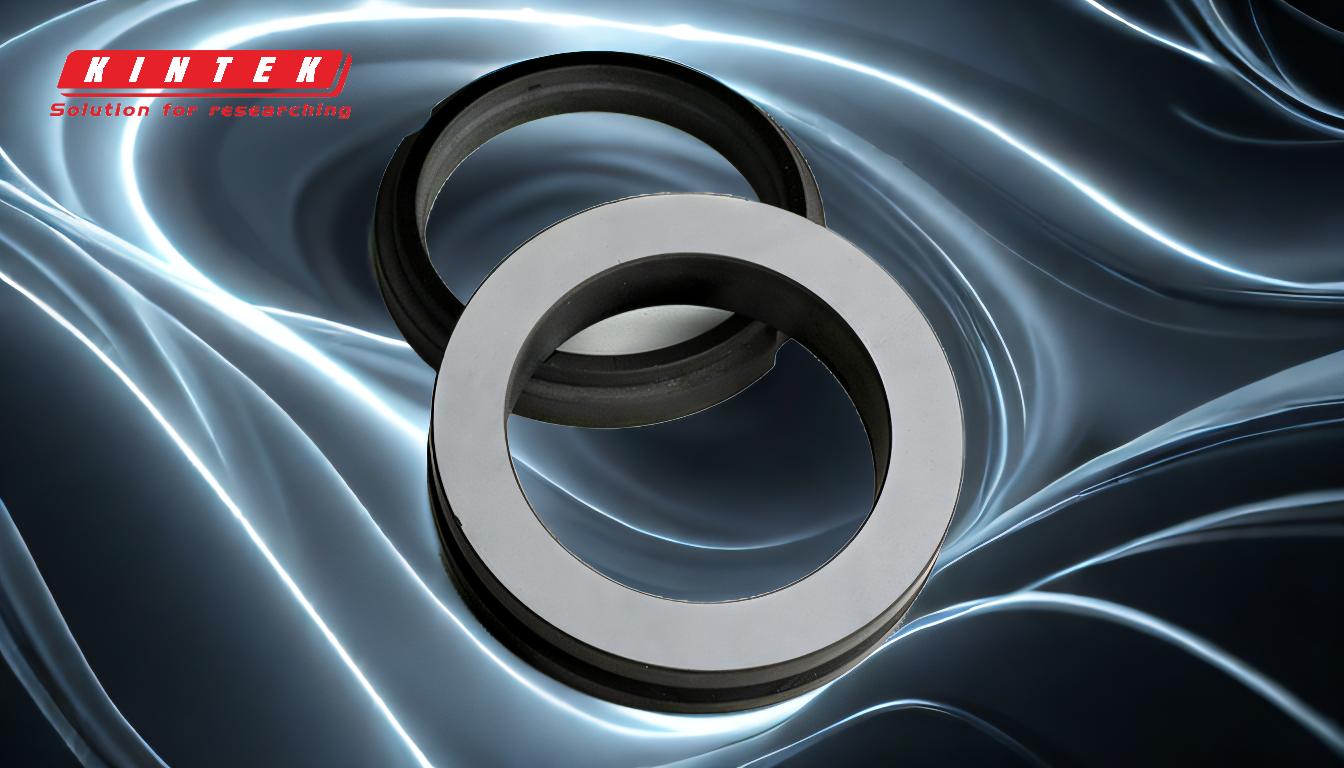
-
Basic Principle of CVD:
- CVD involves the chemical reaction of gaseous precursors (often volatile compounds) in a controlled environment. These precursors decompose or react at high temperatures, depositing a solid material onto a substrate.
- The process is typically carried out in a low vacuum or atmospheric pressure environment, depending on the specific application.
- The substrate is heated to a temperature that activates the chemical reaction, often exceeding the tempering temperature of materials like high-speed steel.
-
Types of CVD:
-
Thermal Chemical Vapor Deposition (TCVD): This method relies on high temperatures to activate the chemical reactions. It includes:
- Metal Organic Chemical Vapor Deposition (MOCVD): Uses metal-organic compounds as precursors, commonly used for growing semiconductor materials.
- Chloride Chemical Vapor Deposition: Involves chloride-based precursors and is often used for depositing refractory metals.
- Hydride Chemical Vapor Deposition: Uses hydride gases as precursors, suitable for growing materials like silicon and germanium.
- Other CVD variants include Plasma-Enhanced CVD (PECVD), which uses plasma to lower the reaction temperature, and Atomic Layer Deposition (ALD), which provides atomic-level control over film thickness.
-
Thermal Chemical Vapor Deposition (TCVD): This method relies on high temperatures to activate the chemical reactions. It includes:
-
Process Characteristics:
- High-Temperature Operation: CVD processes often require temperatures exceeding 800°C, which can affect the substrate's mechanical properties. For example, high-speed steel tools must undergo vacuum heat treatment after coating to restore their hardness.
- Conformal Coating: CVD provides excellent step coverage, allowing uniform coatings on complex geometries, including deep holes and internal walls.
- Surface Roughness: CVD coatings tend to have a slightly rougher surface compared to the substrate, which can be beneficial for certain applications like tool coatings, where improved adhesion is required.
-
Applications of CVD:
- Semiconductor Industry: CVD is extensively used to grow thin films of silicon, silicon dioxide, and other materials for integrated circuits and microelectronics.
- Tool Coatings: CVD coatings, such as titanium nitride (TiN) and diamond-like carbon (DLC), are applied to cutting tools to enhance wear resistance and durability.
- Optics: CVD is used to deposit anti-reflective coatings and other optical layers on lenses and mirrors.
- Energy: CVD plays a role in manufacturing solar cells and fuel cells by depositing materials like silicon and ceramic layers.
-
Advantages of CVD:
- Uniformity and Conformality: CVD provides excellent coverage on complex shapes and high-aspect-ratio features.
- High Purity: The process can produce high-purity materials with minimal impurities.
- Versatility: CVD can deposit a wide range of materials, including metals, ceramics, and polymers.
-
Challenges and Considerations:
- High Temperature: The need for high temperatures can limit the choice of substrates and may require post-processing to restore material properties.
- Cost: CVD equipment and precursors can be expensive, making the process less economical for some applications.
- Safety: Handling toxic or flammable precursors requires strict safety protocols.
In summary, the CVD method of growth is a versatile and powerful technique for depositing high-quality thin films and coatings. Its ability to produce uniform and conformal coatings on complex geometries makes it indispensable in industries ranging from semiconductors to tool manufacturing. However, the high-temperature requirements and associated costs must be carefully managed to optimize its use.
Summary Table:
Aspect | Details |
---|---|
Basic Principle | Chemical reaction of gaseous precursors at high temperatures to deposit solid materials on a substrate. |
Types of CVD | - Thermal CVD (TCVD) |
- Plasma-Enhanced CVD (PECVD)
- Atomic Layer Deposition (ALD) | | Applications | - Semiconductors
- Tool Coatings
- Optics
- Energy (solar cells, fuel cells) | | Advantages | - Uniform and conformal coatings
- High purity
- Versatile material deposition | | Challenges | - High-temperature requirements
- Costly equipment and precursors
- Safety concerns with toxic/flammable gases |
Discover how the CVD method can revolutionize your material deposition process—contact our experts today for tailored solutions!