The deposition process in wafer fabrication is a critical step in semiconductor manufacturing, involving the application of thin films of materials onto a substrate to create functional layers. This process is essential for producing high-performance electronic devices. The deposition process typically involves preparing the substrate, cleaning it, depositing the material, and then cooling the system. Various techniques, such as Chemical Vapor Deposition (CVD) and Physical Vapor Deposition (PVD), are used depending on the material and application. These techniques ensure the creation of high-quality, uniform thin films necessary for semiconductor devices.
Key Points Explained:
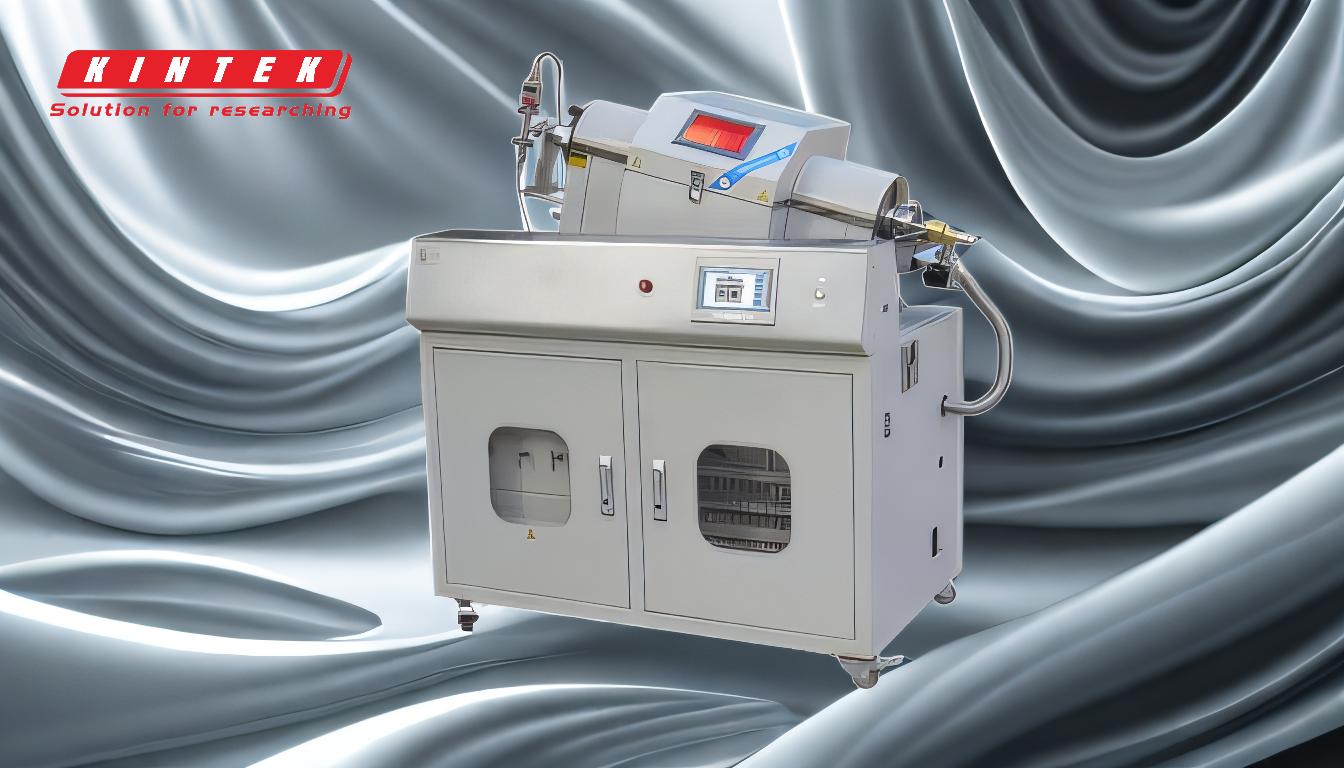
-
Purpose of Deposition in Wafer Fabrication:
- The deposition process is used to create thin films of materials on a substrate, which are essential for the functionality of semiconductor devices.
- These thin films can be conductive, insulating, or semiconducting, depending on the application.
-
Key Steps in the Deposition Process:
- Ramp Up: The chamber is prepared by gradually increasing the temperature and decreasing the pressure to create the ideal environment for deposition.
- Etching: The substrate is cleaned using plasma etching to remove contaminants and improve adhesion of the deposited material.
- Coating: The material to be deposited is projected onto the substrate, forming a thin film.
- Ramp Down: The chamber is returned to room temperature and ambient pressure using a cooling system.
-
Types of Deposition Techniques:
-
Chemical Vapor Deposition (CVD):
- High-Density Plasma CVD (HDP-CVD): Used for depositing materials with high aspect ratios.
- Plasma-Enhanced CVD (PECVD): Utilizes plasma to enhance the deposition process at lower temperatures.
- CVD Tungsten: Specifically used for depositing tungsten layers.
-
Physical Vapor Deposition (PVD):
- Evaporation: Material is heated to a vapor and then condensed onto the substrate.
- Sputtering: Material is ejected from a target and deposited onto the substrate.
-
Chemical Vapor Deposition (CVD):
-
Materials Used in Deposition:
- Aluminum: Commonly used for the main layer of the substrate due to its conductivity and ease of deposition.
- Secondary Layers: Other materials are deposited to create specific components or functionalities within the semiconductor device.
-
Common Deposition Technologies:
- Low Pressure CVD (LPCVD): Operates at low pressures to deposit high-quality films.
- Plasma Enhanced CVD (PECVD): Uses plasma to allow deposition at lower temperatures.
- Sub-Atmospheric Pressure CVD (SACVD): Operates at pressures below atmospheric for specific applications.
- Atmospheric Pressure CVD (APCVD): Deposits films at atmospheric pressure.
- Atomic Layer Deposition (ALD): Deposits one atomic layer at a time for precise control.
- Physical Vapor Deposition (PVD): Includes techniques like sputtering and evaporation.
- Ultra-High Vacuum CVD (UHV-CVD): Operates under ultra-high vacuum conditions for high-purity films.
- Diamond-Like Carbon (DLC): Used for depositing hard, wear-resistant coatings.
- Commercial Film (C-F): General term for various commercial deposition films.
- Epitaxial Deposition (Epi): Deposits crystalline layers that match the substrate's crystal structure.
-
Applications of Deposition in Semiconductor Devices:
- Interlayer Insulators: Deposition is used to form insulating layers between conductive layers.
- Photoresist Patterns: Deposition helps in creating patterns that are used in subsequent etching processes.
- Doping: Deposition techniques are used to introduce dopants into the semiconductor material to alter its electrical properties.
-
Importance of Deposition in Semiconductor Industry:
- High-Quality Films: Ensures the production of high-performance, reliable semiconductor devices.
- Uniformity: Deposition techniques provide uniform thin films, which are crucial for device performance.
- Versatility: Various deposition methods allow for the creation of different types of materials and layers, enabling complex device architectures.
In summary, the deposition process in wafer fabrication is a multifaceted and essential step in semiconductor manufacturing. It involves a series of carefully controlled steps and utilizes various techniques to deposit materials onto substrates, ensuring the creation of high-quality, uniform thin films necessary for the functionality of modern electronic devices.
Summary Table:
Aspect | Details |
---|---|
Purpose | Creates thin films for conductive, insulating, or semiconducting layers. |
Key Steps | Ramp Up, Etching, Coating, Ramp Down. |
Techniques | CVD (HDP-CVD, PECVD, CVD Tungsten), PVD (Evaporation, Sputtering). |
Materials | Aluminum, secondary layers for specific functionalities. |
Technologies | LPCVD, PECVD, SACVD, APCVD, ALD, PVD, UHV-CVD, DLC, Epi, C-F. |
Applications | Interlayer insulators, photoresist patterns, doping. |
Importance | Ensures high-quality, uniform films for reliable semiconductor devices. |
Discover how advanced deposition techniques can enhance your semiconductor manufacturing—contact our experts today!