The deposition rate of e-beam evaporation typically ranges from 0.1 to 100 nanometers (nm) per minute, depending on factors such as the material being evaporated, the power of the electron beam, and the substrate temperature. This range makes e-beam evaporation a highly efficient and versatile method for depositing thin films, especially for materials with high melting points. The process is characterized by low impurity levels, good directionality, and high throughput, making it suitable for applications requiring precise and uniform coatings. However, achieving uniform deposition can be challenging due to the isotropic nature of the process, which is often mitigated using spherical wafer holders or planetary systems.
Key Points Explained:
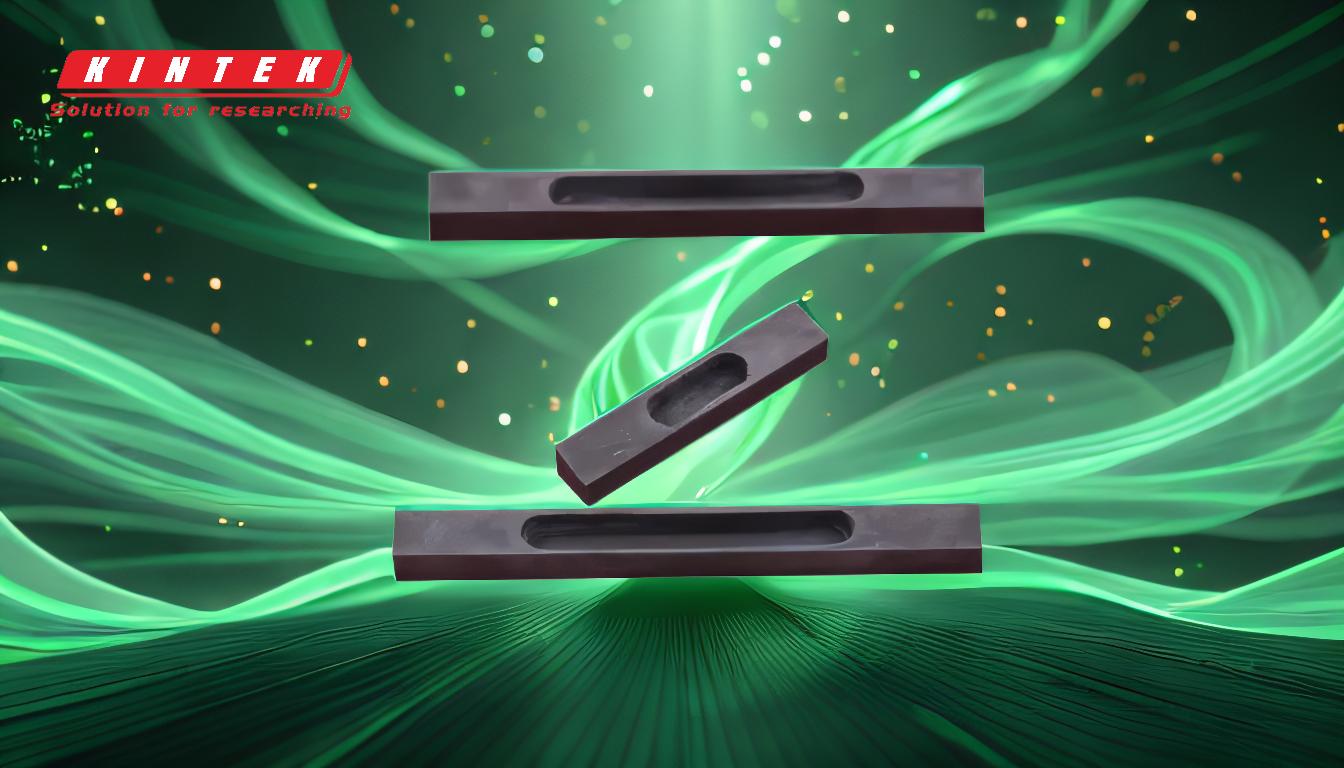
-
Deposition Rate Range:
- The deposition rate for e-beam evaporation typically falls between 0.1 to 100 nanometers (nm) per minute. This range is influenced by several factors, including the material being evaporated, the power of the electron beam, and the substrate temperature. For example, materials with higher melting points may require higher beam power, which can increase the deposition rate.
-
Material Versatility:
- E-beam evaporation is capable of evaporating virtually any material, including those with high melting points, such as refractory metals. This versatility is due to the high-energy electron beam, which can generate the temperatures needed to evaporate even the most challenging materials. This makes it a preferred method for applications requiring high-temperature materials.
-
Low Impurity Levels:
- One of the significant advantages of e-beam evaporation is its ability to produce coatings with low impurity levels. The high vacuum environment minimizes contamination, ensuring that the deposited films are of high purity. This is particularly important in applications such as semiconductor manufacturing, where material purity is critical.
-
Deposition Uniformity Challenges:
- Achieving uniform deposition can be challenging in e-beam evaporation due to its isotropic nature. Atoms are evaporated off the source in all directions equally, leading to non-uniform coatings, especially on substrates not directly above the crucible. To address this, manufacturers often use spherical wafer holders or planetary systems to improve uniformity. However, even with these techniques, achieving perfect uniformity remains a challenge.
-
High Throughput and Directionality:
- E-beam evaporation offers high throughput and good directionality, making it suitable for large-scale production. The process can deposit thin films quickly and efficiently, which is beneficial for industries requiring high-volume production, such as optics and electronics.
-
Applications:
- E-beam evaporation is widely used in industries requiring precise and uniform coatings, such as semiconductor manufacturing, optics, and solar cells. Its ability to deposit high-purity, high-melting-point materials makes it indispensable in these fields.
In summary, the deposition rate of e-beam evaporation is highly variable, ranging from 0.1 to 100 nm per minute, depending on the material and process conditions. While the method offers numerous advantages, including material versatility and low impurity levels, challenges such as deposition uniformity must be carefully managed to achieve optimal results.
Summary Table:
Aspect | Details |
---|---|
Deposition Rate | 0.1 to 100 nanometers (nm) per minute |
Material Versatility | Can evaporate virtually any material, including high-melting-point metals |
Impurity Levels | Low contamination due to high vacuum environment |
Uniformity Challenges | Non-uniform coatings due to isotropic nature; mitigated with special tools |
Throughput & Directionality | High throughput and good directionality for large-scale production |
Applications | Semiconductor manufacturing, optics, solar cells, and more |
Looking to optimize your thin film deposition process? Contact our experts today for tailored solutions!