The deposition rate of electron beam evaporation typically ranges from 0.1 to 100 nanometers (nm) per minute, depending on the material being evaporated, the power of the electron beam, and the substrate temperature. This method is highly efficient for depositing thin films, especially for materials with high melting points, and is widely used in industries such as aerospace, semiconductors, and optics. The process leverages a high-energy electron beam to heat and evaporate the target material, enabling precise control over the deposition rate and uniformity.
Key Points Explained:
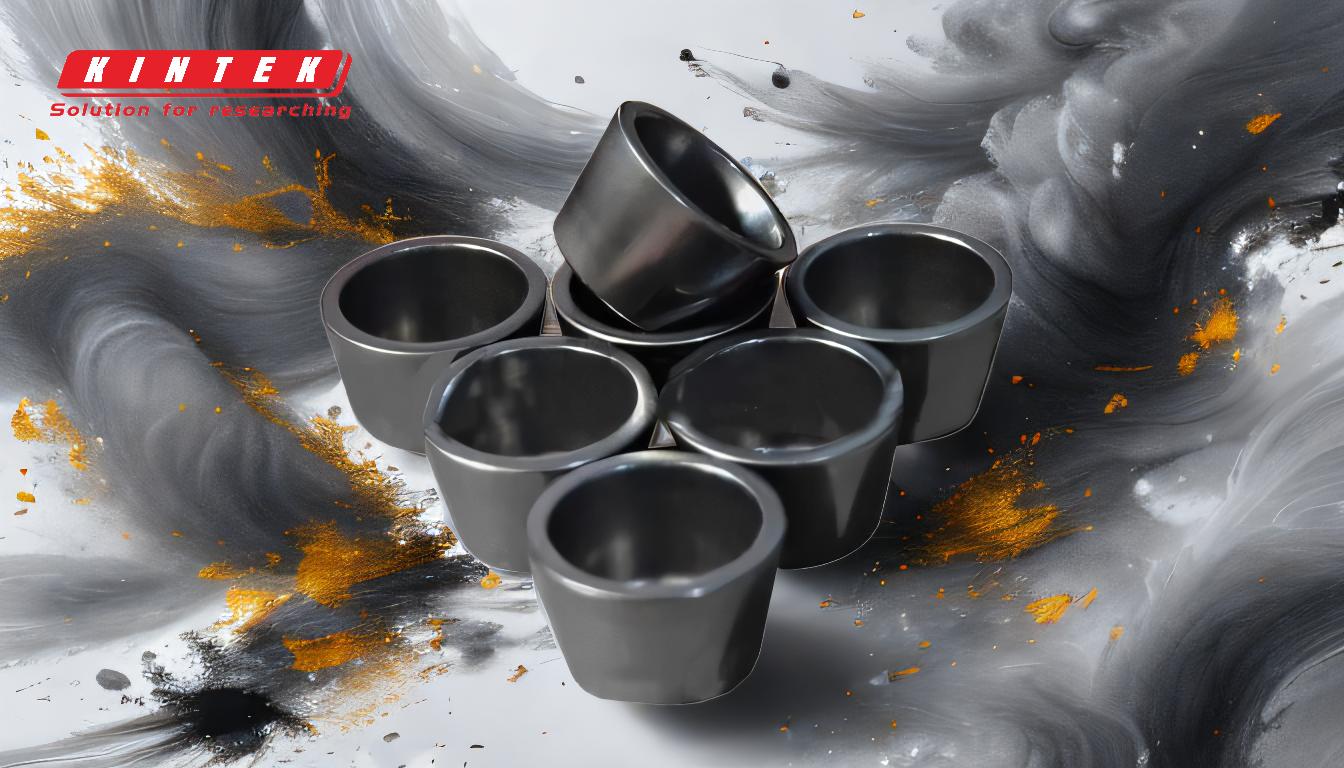
-
Deposition Rate Range:
- The deposition rate for electron beam evaporation typically falls between 0.1 to 100 nanometers (nm) per minute.
- This range is influenced by factors such as the material's properties, the electron beam's power, and the substrate's temperature.
-
Factors Influencing Deposition Rate:
- Material Properties: Materials with high melting points, such as gold or ceramics, require higher energy to evaporate, which can affect the deposition rate.
- Electron Beam Power: Higher power levels increase the kinetic energy of the electrons, leading to faster evaporation and higher deposition rates.
- Substrate Temperature: Lower substrate temperatures can slow down the deposition process, while higher temperatures may enhance it, depending on the material.
-
Advantages of Electron Beam Evaporation:
- High Deposition Rates: The process is capable of achieving rapid deposition rates, making it suitable for industrial applications.
- Material Versatility: It can handle a wide range of materials, including those with high melting points, such as metals and ceramics.
- Uniformity and Control: The process offers excellent control over film thickness and uniformity, which is critical for applications in optics and semiconductors.
-
Applications of Electron Beam Evaporation:
- Optical Coatings: Used for depositing thin films on solar panels, eyeglasses, and architectural glass.
- Aerospace and Automotive Industries: Ideal for creating high-temperature and wear-resistant coatings.
- Semiconductors: Used for depositing electrical contacts and other thin-film components.
-
Mechanism of Electron Beam Evaporation:
- A high-energy electron beam is directed at the target material, converting kinetic energy into thermal energy upon impact.
- The heat generated evaporates the material, which then condenses on the substrate to form a thin film.
-
Comparison with Other Deposition Methods:
- Higher Deposition Rates: Compared to traditional thermal evaporation, electron beam evaporation offers faster deposition rates.
- Better Material Utilization: The process is more efficient, reducing material waste and lowering costs.
By understanding these key points, equipment and consumable purchasers can better evaluate the suitability of electron beam evaporation for their specific applications, ensuring optimal performance and cost-effectiveness.
Summary Table:
Aspect | Details |
---|---|
Deposition Rate Range | 0.1 to 100 nanometers (nm) per minute |
Key Influencing Factors | Material properties, electron beam power, substrate temperature |
Advantages | High deposition rates, material versatility, excellent uniformity & control |
Applications | Optical coatings, aerospace, automotive, semiconductors |
Mechanism | High-energy electron beam heats and evaporates target material |
Optimize your thin film deposition process with electron beam evaporation—contact our experts today!