The die of a pellet mill is a critical component responsible for shaping feed material into pellets. It works in conjunction with other parts, such as the press roller, to compress and extrude the feed through small holes, forming uniform pellets. The die's design, including factors like inlet depth and material composition, significantly impacts the efficiency, durability, and quality of the pelletizing process. Understanding its role and maintenance is essential for optimizing pellet production and extending the equipment's lifespan.
Key Points Explained:
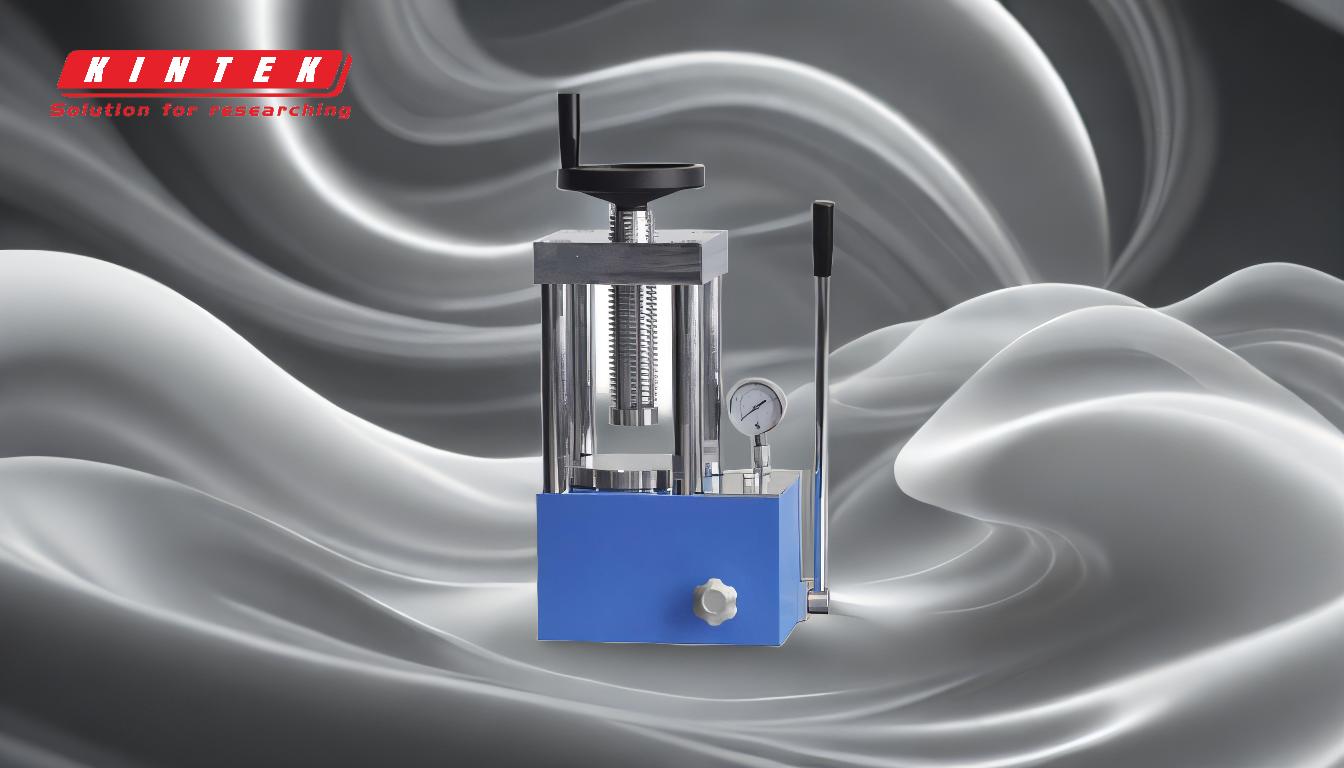
-
Role of the Die in a Pellet Mill:
- The die is the central component that shapes feed material into pellets. It consists of a metal plate with precisely drilled holes through which the feed is forced under pressure.
- The feed material is compressed between the die and the press roller, extruding it through the holes to form pellets of consistent size and density.
- The die's design and quality directly influence the pellet's shape, hardness, and overall production efficiency.
-
Types of Dies:
- Flat Die: Commonly used in small-scale pellet mills, flat dies are horizontal plates with holes. They are simpler in design and easier to maintain, making them suitable for smaller operations.
- Ring Die: Used in large-scale industrial pellet mills, ring dies are cylindrical with holes drilled around the circumference. They offer higher production capacity and are more efficient for continuous operations.
-
Key Design Features:
- Inlet Depth: The depth of the countersink where the feed enters the compression area. Proper inlet depth ensures smooth material flow and reduces wear on the die.
- Hole Diameter and Length: The size and length of the holes determine the pellet's diameter and density. Smaller holes produce finer pellets, while longer holes increase pellet hardness.
- Material Composition: Dies are typically made from high-quality alloy steel to withstand the high pressure and abrasion during the pelletizing process.
-
Impact of Feed Composition:
- The feed's fat content acts as a lubricant, reducing friction and wear on the die. A feed formula containing 1.5-4% fat runs smoother and minimizes abrasion, extending the die's lifespan.
- High-fat feeds can also improve pellet quality by enhancing binding and reducing energy consumption during the pelleting process.
-
Maintenance and Longevity:
- Regular maintenance, such as cleaning and inspecting the die for wear, is essential to ensure consistent pellet quality and prevent downtime.
- Using feeds with appropriate fat content and avoiding abrasive materials can significantly reduce wear and tear, prolonging the die's life.
-
Integration with Other Components:
- The die works in tandem with the press roller, feeder, and power source to form a complete pelletizing system. Proper alignment and synchronization of these components are crucial for efficient operation.
- The electric motor or engine drives the system, while the feeder ensures a consistent supply of feed material to the die.
-
Applications in Livestock Feed Production:
- Pellet mills, including their dies, are widely used in producing feed pellets for livestock such as cattle, pigs, and chickens. The pellets improve feed handling, storage, and acceptance by animals.
- The die's ability to produce uniform pellets ensures balanced nutrition and reduces feed waste, making it a vital component in modern livestock farming.
Understanding the die's role, design, and maintenance is essential for anyone involved in pellet mill operations. By optimizing these factors, producers can enhance efficiency, reduce costs, and ensure high-quality feed pellets for livestock.
Summary Table:
Aspect | Details |
---|---|
Role | Shapes feed material into pellets through compression and extrusion. |
Types | Flat Die (small-scale), Ring Die (large-scale). |
Key Design Features | Inlet depth, hole diameter/length, material composition. |
Feed Composition | Fat content (1.5-4%) reduces friction, improves binding, and extends die life. |
Maintenance | Regular cleaning, inspection, and using appropriate feed formulas. |
Applications | Livestock feed production for cattle, pigs, and chickens. |
Optimize your pellet production with the right die—contact our experts today for tailored solutions!