Hydraulic and mechanical shaping machines are both used in metalworking to shape materials, but they operate on fundamentally different principles. Hydraulic shaping machines use fluid pressure to generate force, offering smooth and precise control over the shaping process. They are ideal for heavy-duty applications and can handle larger workpieces with ease. Mechanical shaping machines, on the other hand, rely on mechanical linkages and gears to convert rotary motion into linear motion. They are generally faster and more suitable for high-speed operations but may lack the precision and versatility of hydraulic systems. The choice between the two depends on the specific requirements of the task, such as the need for precision, speed, or the ability to handle heavy loads.
Key Points Explained:
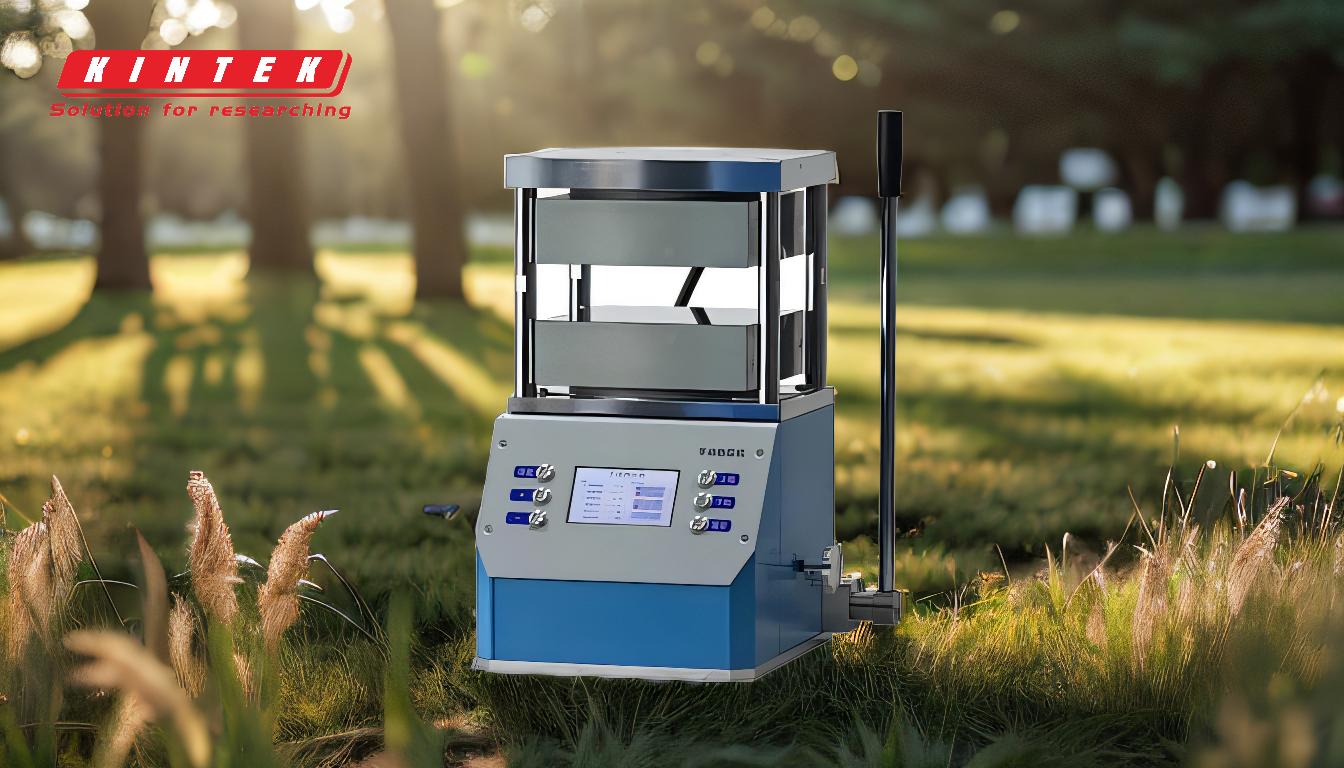
-
Operating Principle:
- Hydraulic Shaping Machines: These machines use hydraulic fluid to generate force. The fluid is pressurized by a pump and directed to a hydraulic cylinder, which moves the ram or tool. This system allows for smooth and continuous force application, making it ideal for tasks requiring precision and control.
- Mechanical Shaping Machines: These machines rely on mechanical components like gears, cams, and linkages to convert the rotary motion of a motor into linear motion. The mechanical system is typically faster but may not offer the same level of control as hydraulic systems.
-
Force and Power:
- Hydraulic Shaping Machines: Hydraulic systems can generate significant force, making them suitable for heavy-duty applications. The force is easily adjustable by controlling the fluid pressure, allowing for precise control over the shaping process.
- Mechanical Shaping Machines: Mechanical systems are generally limited by the strength of their components. While they can be very fast, they may not be able to generate the same level of force as hydraulic systems, especially for larger workpieces.
-
Speed and Efficiency:
- Hydraulic Shaping Machines: These machines are typically slower than mechanical ones due to the time required to build up and release hydraulic pressure. However, they offer excellent control and can handle complex shapes with ease.
- Mechanical Shaping Machines: Mechanical systems are generally faster, making them suitable for high-speed operations. However, they may not be as efficient when it comes to handling complex shapes or requiring precise control.
-
Precision and Control:
- Hydraulic Shaping Machines: The ability to control fluid pressure precisely allows for excellent control over the shaping process. This makes hydraulic machines ideal for tasks requiring high precision and smooth finishes.
- Mechanical Shaping Machines: While mechanical systems can be precise, they may not offer the same level of control as hydraulic systems, especially when it comes to handling complex shapes or requiring fine adjustments.
-
Maintenance and Durability:
- Hydraulic Shaping Machines: Hydraulic systems require regular maintenance to ensure the fluid is clean and the seals are intact. However, they are generally durable and can handle heavy loads without significant wear.
- Mechanical Shaping Machines: Mechanical systems are generally easier to maintain, with fewer components that can fail. However, they may wear out faster under heavy loads, especially if not properly maintained.
-
Applications:
- Hydraulic Shaping Machines: Ideal for heavy-duty applications, such as forging, stamping, and forming large metal parts. They are also suitable for tasks requiring high precision and control, such as in the aerospace and automotive industries.
- Mechanical Shaping Machines: Best suited for high-speed operations, such as cutting, punching, and shearing. They are commonly used in industries where speed is more critical than precision, such as in the production of consumer goods.
In summary, the choice between hydraulic and mechanical shaping machines depends on the specific requirements of the task. Hydraulic machines offer superior control and are ideal for heavy-duty applications, while mechanical machines are faster and more suitable for high-speed operations. Understanding these differences can help in selecting the right machine for the job.
Summary Table:
Feature | Hydraulic Shaping Machines | Mechanical Shaping Machines |
---|---|---|
Operating Principle | Uses hydraulic fluid for force generation | Relies on mechanical linkages and gears |
Force and Power | High force, adjustable pressure | Limited by component strength |
Speed and Efficiency | Slower but precise | Faster, ideal for high-speed operations |
Precision and Control | Excellent control, smooth finishes | Less precise, suitable for simpler tasks |
Maintenance | Requires regular maintenance | Easier to maintain |
Applications | Heavy-duty, precision tasks | High-speed operations |
Need help choosing the right shaping machine for your needs? Contact our experts today!