Batch and continuous pyrolysis are two distinct methods used in the thermal decomposition of organic materials, such as waste tires or plastics, in an oxygen-free environment. The key differences lie in their operational mechanisms, efficiency, equipment complexity, and cost. Batch pyrolysis operates in cycles, requiring repeated heating and cooling of the retort, which reduces thermal efficiency and makes it harder to maintain consistent product quality. Continuous pyrolysis, on the other hand, operates without interruption, offering higher efficiency, stability, and consistent product quality. However, continuous systems require more complex equipment, rigorous material pretreatment, and higher investment and operational costs. Batch systems are simpler, more flexible, and cost-effective but less efficient and stable in comparison.
Key Points Explained:
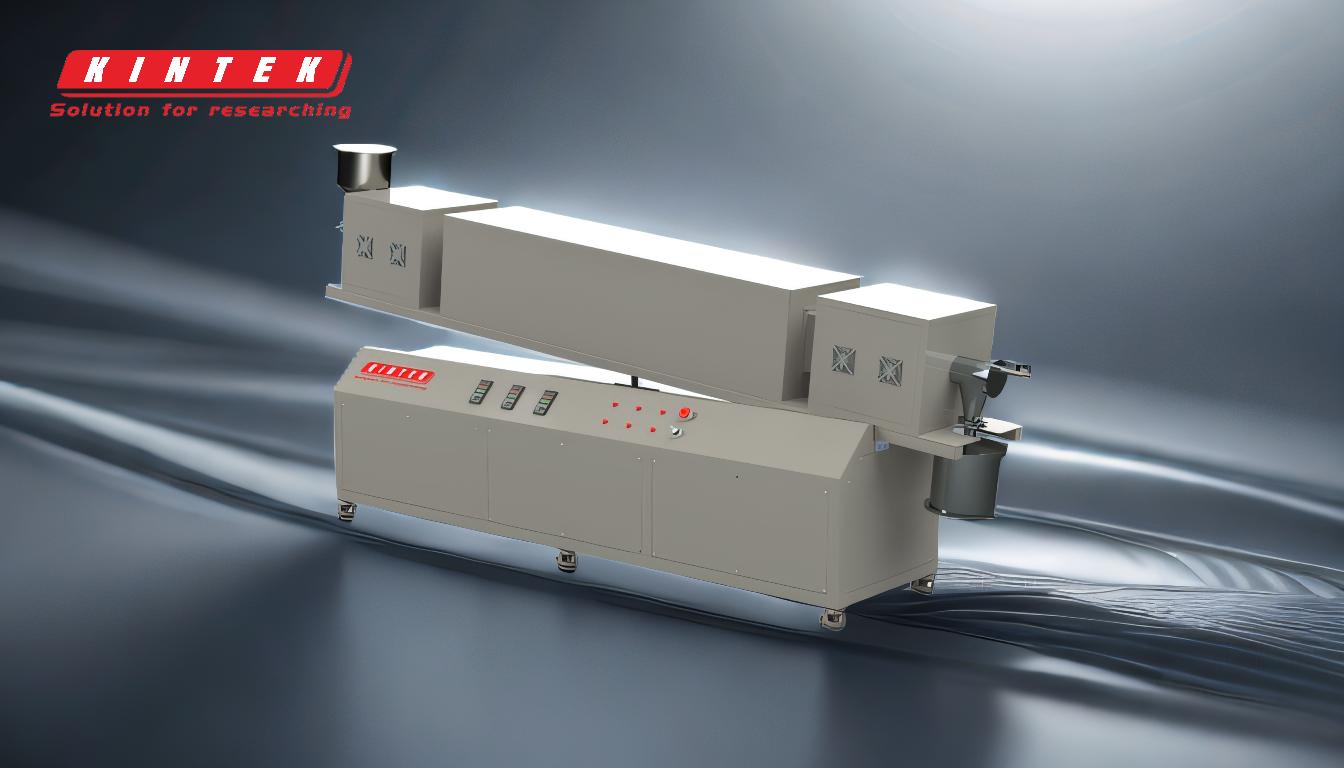
-
Operational Mechanism:
- Batch Pyrolysis: Operates in cycles, where the retort is loaded, heated, cooled, and unloaded repeatedly. This cyclic process involves removing the retort from the high-temperature zone, which reduces thermal efficiency due to repeated heating and cooling.
- Continuous Pyrolysis: Operates without interruption, allowing for continuous feeding, pyrolysis, and discharge of slag. This eliminates the need for repeated heating and cooling, improving thermal efficiency and maintaining consistent product quality.
-
Efficiency and Stability:
- Batch Pyrolysis: Cyclic heating and cooling make it difficult to ensure consistent product quality. The repeated thermal cycles reduce overall efficiency.
- Continuous Pyrolysis: Offers higher efficiency and stability due to uninterrupted operation. The consistent high-temperature environment ensures uniform product quality.
-
Equipment Complexity:
- Batch Pyrolysis: Simpler equipment design with fewer requirements for automation and material pretreatment. This makes it more flexible in terms of feeding methods and easier to operate.
- Continuous Pyrolysis: Requires more complex equipment designs, better equipment matching, and advanced automatic control capabilities. The process demands rigorous material pretreatment, such as cutting and shredding waste tires, to ensure smooth operation.
-
Material Pretreatment:
- Batch Pyrolysis: Allows for simpler material pretreatment, making it more adaptable to various types of waste without extensive preprocessing.
- Continuous Pyrolysis: Requires more rigorous material pretreatment to ensure the feedstock is suitable for continuous feeding and pyrolysis. This includes cutting, shredding, and sometimes drying the material.
-
Investment and Operational Costs:
- Batch Pyrolysis: Lower initial investment and operational costs due to simpler equipment and less rigorous pretreatment requirements.
- Continuous Pyrolysis: Higher investment and operational costs due to complex equipment, advanced automation, and the need for rigorous material pretreatment.
-
Flexibility:
- Batch Pyrolysis: Offers more flexibility in feeding methods and can handle a wider variety of materials without extensive preprocessing.
- Continuous Pyrolysis: Less flexible due to the need for consistent feedstock characteristics and rigorous pretreatment. However, it allows for feeding at high temperatures and better slag sealing.
-
Heating Methods:
- Batch Pyrolysis: Typically uses conduction heating, where heat is transferred directly through the retort walls.
- Continuous Pyrolysis: Often uses hot air heating, which provides more uniform and efficient heat distribution throughout the process.
-
Product Quality:
- Batch Pyrolysis: Product quality may vary due to the cyclic nature of the process, which can lead to inconsistencies in temperature and reaction conditions.
- Continuous Pyrolysis: Maintains consistent product quality due to the continuous and stable high-temperature environment, resulting in more uniform pyrolysis products.
In summary, batch pyrolysis is simpler, more flexible, and cost-effective but suffers from lower efficiency and inconsistent product quality. Continuous pyrolysis, while more complex and costly, offers higher efficiency, stability, and consistent product quality, making it suitable for large-scale operations where these factors are critical. The choice between the two methods depends on the specific requirements, scale, and budget of the pyrolysis project.
Summary Table:
Aspect | Batch Pyrolysis | Continuous Pyrolysis |
---|---|---|
Operational Mechanism | Cyclic process with repeated heating and cooling | Continuous process with uninterrupted feeding and pyrolysis |
Efficiency | Lower due to repeated thermal cycles | Higher due to stable, uninterrupted operation |
Equipment Complexity | Simpler design, less automation required | Complex design with advanced automation and material pretreatment |
Material Pretreatment | Minimal preprocessing needed | Rigorous preprocessing (cutting, shredding, drying) required |
Cost | Lower initial and operational costs | Higher initial and operational costs |
Flexibility | More adaptable to various materials | Less flexible, requires consistent feedstock characteristics |
Heating Method | Conduction heating through retort walls | Hot air heating for uniform heat distribution |
Product Quality | Inconsistent due to cyclic nature | Consistent and uniform due to stable high-temperature environment |
Ready to choose the right pyrolysis system for your needs? Contact our experts today for personalized guidance!