Biochar and pyrolysis are related but distinct processes and products within the realm of biomass conversion. Biochar is a carbon-rich solid material produced through the pyrolysis of biomass, while pyrolysis is the thermal decomposition process that occurs in the absence of oxygen, leading to the production of biochar, bio-oil, and syngas. The key difference lies in their roles: biochar is the end product used for soil amendment, carbon sequestration, and other applications, whereas pyrolysis is the process that enables the creation of biochar and other byproducts. Understanding these differences is crucial for industries and researchers focusing on sustainable energy and agricultural practices.
Key Points Explained:
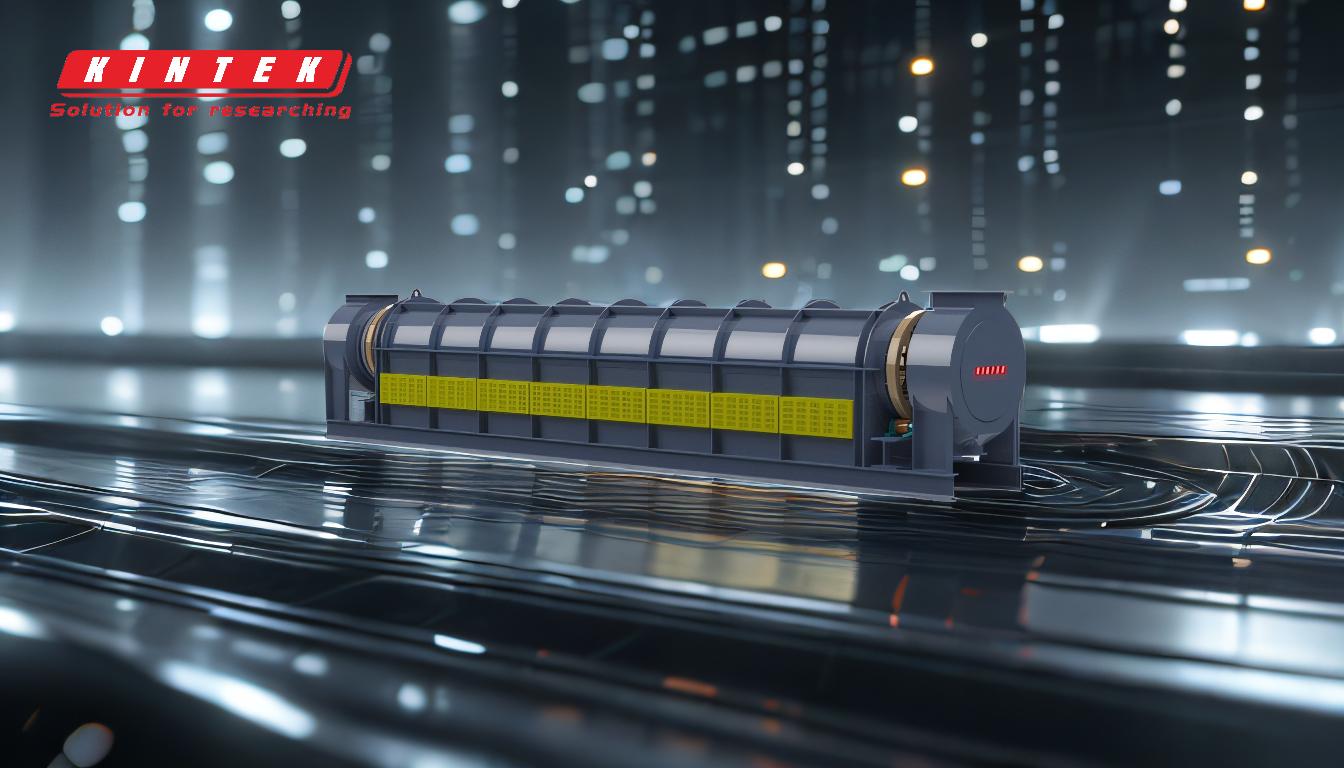
-
Definition and Purpose:
- Biochar: Biochar is a solid, carbon-rich material obtained from the pyrolysis of organic biomass such as wood, agricultural residues, or manure. It is primarily used to improve soil health, enhance carbon sequestration, and reduce greenhouse gas emissions.
- Pyrolysis: Pyrolysis is a thermal decomposition process that breaks down organic materials in the absence of oxygen. It produces three main products: biochar, bio-oil, and syngas. The process is used for energy generation, waste management, and the production of bio-based chemicals.
-
Process and Byproducts:
- Biochar Production: Biochar is produced through slow pyrolysis, a process that involves heating biomass at relatively low temperatures (300–500°C) over a longer duration. This maximizes the yield of biochar while minimizing the production of bio-oil and syngas.
- Pyrolysis Process: Pyrolysis can occur under different conditions, such as fast, intermediate, or slow pyrolysis, depending on the desired end products. Fast pyrolysis, for example, focuses on maximizing bio-oil production, while slow pyrolysis emphasizes biochar yield.
-
Applications:
- Biochar Applications: Biochar is widely used in agriculture to improve soil fertility, water retention, and microbial activity. It is also utilized in environmental applications, such as water filtration and carbon sequestration.
- Pyrolysis Applications: Pyrolysis is employed in waste-to-energy systems, biofuel production, and the creation of bio-based chemicals. For instance, the bioliq® concept involves mixing bio-oil with char to produce a stable suspension for gasification, which is then used to generate synthesis gas for motor fuels and chemicals.
-
Environmental Impact:
- Biochar: Biochar is considered a sustainable solution for carbon sequestration, as it locks carbon in a stable form for centuries, reducing atmospheric CO₂ levels. It also helps mitigate soil degradation and reduces the need for chemical fertilizers.
- Pyrolysis: Pyrolysis contributes to waste reduction and renewable energy production. However, its environmental impact depends on the type of biomass used, the pyrolysis conditions, and the management of byproducts like bio-oil and syngas.
-
Technological and Industrial Relevance:
- Biochar: Biochar production is gaining traction in sustainable agriculture and climate change mitigation strategies. Its production is relatively simple and can be scaled for small or large operations.
- Pyrolysis: Pyrolysis is a more complex process that requires advanced technology and infrastructure. It is often integrated into larger systems, such as the bioliq® concept, which combines pyrolysis with gasification for industrial-scale synthesis gas production.
In summary, biochar and pyrolysis are interconnected but serve different purposes. Biochar is a valuable end product with agricultural and environmental benefits, while pyrolysis is the process that enables the production of biochar and other energy-rich byproducts. Understanding their differences is essential for optimizing their applications in sustainable energy and agriculture.
Summary Table:
Aspect | Biochar | Pyrolysis |
---|---|---|
Definition | Carbon-rich solid material from pyrolysis of biomass. | Thermal decomposition of biomass in the absence of oxygen. |
Purpose | Soil amendment, carbon sequestration, and environmental applications. | Energy generation, waste management, and bio-based chemical production. |
Process | Produced via slow pyrolysis (300–500°C). | Can be fast, intermediate, or slow, depending on desired byproducts. |
Byproducts | Primarily biochar. | Biochar, bio-oil, and syngas. |
Applications | Agriculture (soil health), water filtration, and carbon sequestration. | Waste-to-energy, biofuel production, and industrial-scale synthesis gas. |
Environmental Impact | Reduces CO₂ levels, improves soil health, and reduces fertilizer use. | Reduces waste and produces renewable energy, but depends on biomass type. |
Industrial Relevance | Simple production, scalable for small or large operations. | Requires advanced technology, integrated into larger systems like bioliq®. |
Want to learn more about biochar and pyrolysis? Contact our experts today for tailored solutions!