Chemical vapor deposition (CVD) and physical vapor deposition (PVD) are two distinct thin-film deposition techniques used in various industries. CVD relies on gaseous precursors that undergo chemical reactions to form a solid film on a substrate, typically at high temperatures. In contrast, PVD involves the physical vaporization of a solid target material, which then condenses onto the substrate at lower temperatures. CVD often results in higher purity films but can produce corrosive byproducts, while PVD offers cleaner processes with lower deposition rates. Both methods have unique advantages and are chosen based on the application's specific requirements, such as temperature sensitivity, material compatibility, and desired film properties.
Key Points Explained:
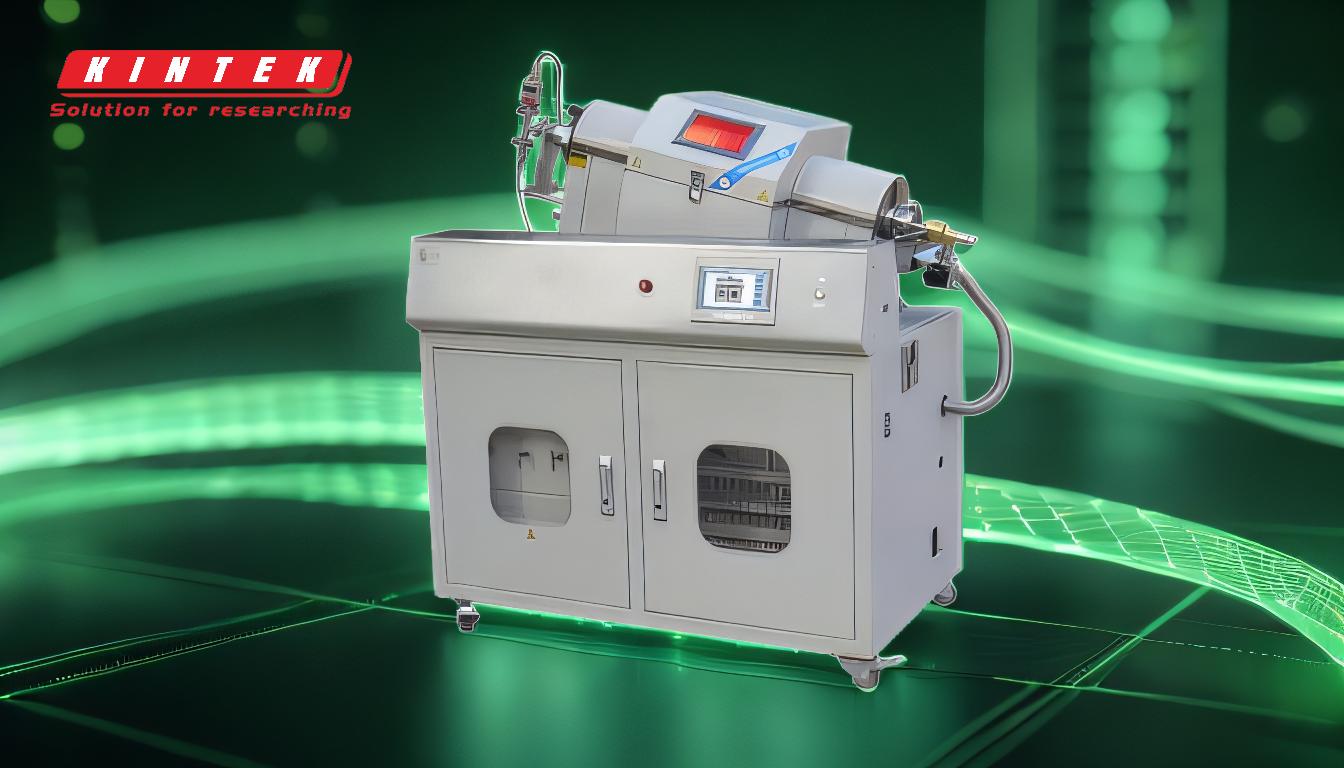
-
Precursor Type:
- CVD: Uses gaseous precursors that chemically react or decompose on the substrate surface to form a solid film. This chemical transformation is a defining feature of CVD.
- PVD: Utilizes solid precursors (targets) that are vaporized through physical processes like evaporation, sputtering, or sublimation. The vaporized material then condenses onto the substrate.
-
Temperature Requirements:
- CVD: Typically operates at high temperatures (500°C–1100°C), which can limit its use with temperature-sensitive substrates. The high temperatures are necessary to drive the chemical reactions.
- PVD: Can be performed at lower temperatures, making it suitable for substrates that cannot withstand high heat. This is particularly advantageous for applications involving plastics or other heat-sensitive materials.
-
Deposition Mechanism:
- CVD: Involves chemical reactions between gaseous precursors or between the precursors and the substrate. This results in a chemically bonded film.
- PVD: Relies on physical processes such as evaporation or sputtering, where atoms or molecules are ejected from a solid target and deposited onto the substrate without chemical reactions.
-
Byproducts and Impurities:
- CVD: Can produce corrosive gaseous byproducts during the chemical reactions, which may require additional handling and disposal measures. Impurities can also be introduced into the film.
- PVD: Generally produces fewer byproducts and cleaner films since it involves physical processes without chemical reactions.
-
Deposition Rates and Efficiency:
- CVD: Offers moderate to high deposition rates, but the process can be slower due to the need for chemical reactions to occur.
- PVD: Typically has lower deposition rates compared to CVD, although specific techniques like Electron Beam Physical Vapor Deposition (EBPVD) can achieve high rates (0.1–100 μm/min) with excellent material utilization efficiency.
-
Film Properties:
- CVD: Produces films with high purity and excellent conformality, making it ideal for applications requiring uniform coatings on complex geometries.
- PVD: Results in films with good adhesion and density, but the conformality may be lower compared to CVD. PVD is often preferred for applications requiring precise control over film thickness and composition.
-
Applications:
- CVD: Commonly used in semiconductor manufacturing, optical coatings, and protective coatings due to its ability to deposit high-quality, uniform films.
- PVD: Widely employed in the production of decorative coatings, wear-resistant coatings, and thin-film solar cells, where lower temperatures and cleaner processes are advantageous.
By understanding these key differences, equipment and consumable purchasers can make informed decisions about which deposition method is best suited for their specific needs, considering factors such as substrate material, desired film properties, and process requirements.
Summary Table:
Aspect | CVD | PVD |
---|---|---|
Precursor Type | Gaseous precursors that chemically react or decompose. | Solid precursors vaporized through physical processes. |
Temperature | High temperatures (500°C–1100°C). | Lower temperatures, suitable for heat-sensitive substrates. |
Deposition Mechanism | Chemical reactions form a solid film. | Physical processes like evaporation or sputtering deposit the film. |
Byproducts | Corrosive gaseous byproducts may form. | Fewer byproducts, cleaner process. |
Deposition Rate | Moderate to high rates, slower due to chemical reactions. | Lower rates, but techniques like EBPVD can achieve high rates. |
Film Properties | High purity, excellent conformality. | Good adhesion and density, lower conformality. |
Applications | Semiconductors, optical coatings, protective coatings. | Decorative coatings, wear-resistant coatings, thin-film solar cells. |
Need help choosing the right deposition method for your application? Contact our experts today!