Chemical vapor deposition (CVD) is a versatile and widely used technique for depositing thin films and coatings on substrates through chemical reactions involving gaseous precursors. Unlike physical vapor deposition (PVD), which relies on physical processes like evaporation or sputtering, CVD involves chemical reactions that transform gaseous molecules into solid materials on the substrate surface. CVD offers unique advantages, such as the ability to coat complex shapes uniformly, high purity of deposited films, and precise control over film properties. Specific variants of CVD, such as microwave plasma chemical vapor deposition, further enhance the process by using plasma to lower deposition temperatures and improve reaction efficiency. This method is particularly useful in applications like microelectronics and advanced material synthesis.
Key Points Explained:
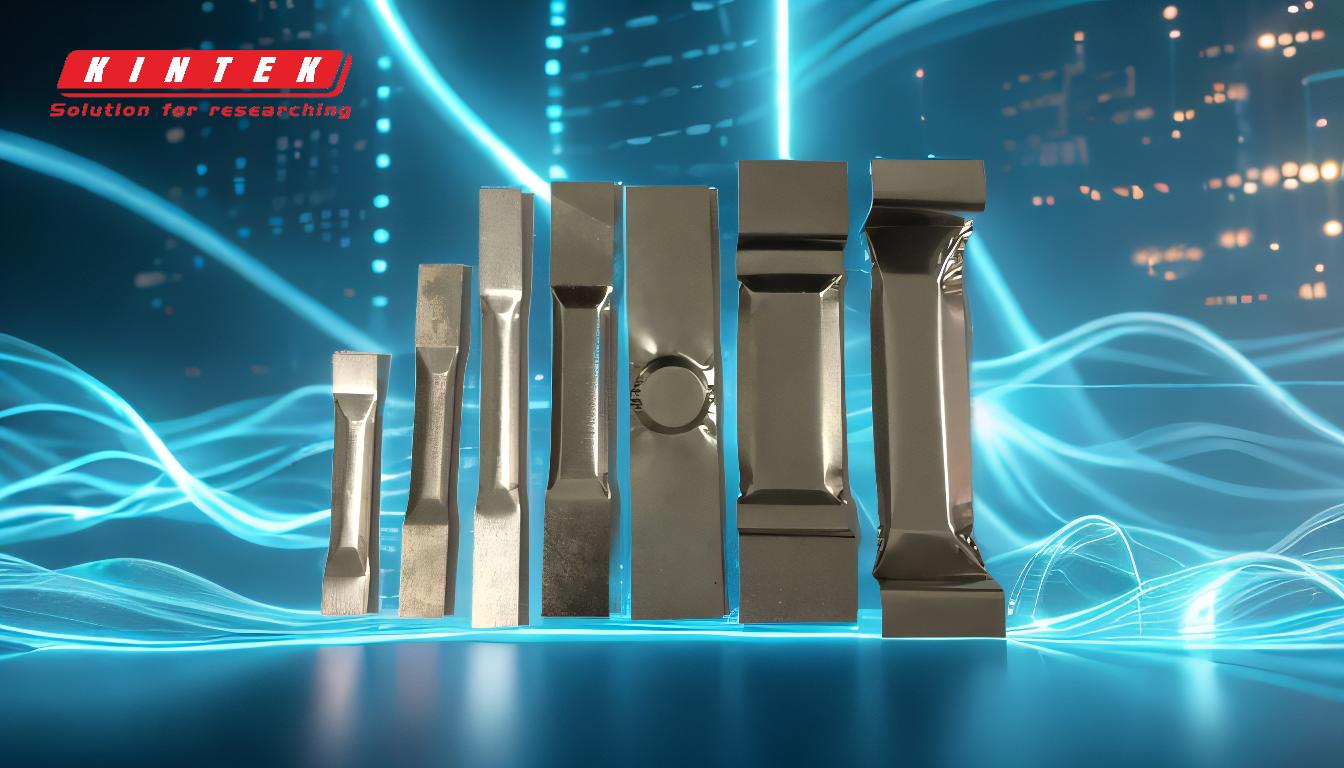
-
Fundamental Difference Between CVD and PVD:
- CVD: Involves chemical reactions between gaseous precursors and the substrate to form thin films. The process relies on the decomposition or reaction of gases on the substrate surface.
- PVD: Uses physical methods like evaporation or sputtering to deposit material. It does not involve chemical reactions and typically requires a line of sight between the target and substrate.
-
Process Mechanism of CVD:
- Gaseous precursors are introduced into a reaction chamber, where they undergo chemical reactions or decomposition on the heated substrate surface.
- The resulting solid material is deposited as a thin film, with properties controlled by adjusting parameters like temperature, pressure, and gas flow rates.
-
Advantages of CVD:
- Uniform Coating: CVD can coat complex shapes and intricate geometries due to the gaseous nature of precursors.
- High Purity: The process produces films with high purity and density.
- Versatility: A wide range of materials, including metals, ceramics, and alloys, can be deposited.
- No Line of Sight Requirement: Unlike PVD, CVD does not require a direct line of sight, enabling the coating of multiple parts simultaneously.
-
Types of CVD:
- Thermal CVD: Uses heat to drive the chemical reactions. It is suitable for high-temperature applications.
- Plasma-Enhanced CVD (PECVD): Employs plasma to lower the deposition temperature, making it ideal for temperature-sensitive substrates.
- Microwave Plasma Chemical Vapor Deposition: A specialized form of PECVD that uses microwave-generated plasma to enhance reaction efficiency and control film properties.
-
Applications of CVD:
- Microelectronics: Used for depositing thin films in semiconductor manufacturing.
- Optoelectronics: Applied in the production of LEDs and solar cells.
- Protective Coatings: Enhances the durability and performance of tools and components.
- Advanced Materials: Used to synthesize materials like carbon nanotubes and graphene.
-
Comparison with PVD:
- Material Compatibility: CVD can deposit a wider range of materials, including organic and inorganic compounds, while PVD is more limited.
- Deposition Temperature: CVD often requires higher temperatures, but PECVD and microwave plasma chemical vapor deposition reduce this requirement.
- Film Quality: CVD films typically have better uniformity and purity compared to PVD films.
-
Future Prospects:
- The demand for CVD is expected to grow due to its applications in emerging technologies like nanotechnology, renewable energy, and advanced electronics.
- Innovations in CVD techniques, such as microwave plasma chemical vapor deposition, are expanding its capabilities and making it more accessible for industrial use.
In summary, CVD stands out as a highly adaptable and efficient deposition method, with its chemical reaction-based approach offering distinct advantages over PVD. Variants like microwave plasma chemical vapor deposition further enhance its utility, making it a cornerstone of modern material science and industrial applications.
Summary Table:
Aspect | CVD | PVD |
---|---|---|
Process | Chemical reactions transform gases into solid films on the substrate. | Physical methods like evaporation or sputtering deposit material. |
Line of Sight | Not required; can coat complex shapes uniformly. | Required; limits coating to surfaces with direct exposure. |
Material Compatibility | Wide range, including metals, ceramics, and alloys. | Limited to specific materials. |
Deposition Temperature | Higher, but reduced in plasma-enhanced variants. | Generally lower than CVD. |
Film Quality | High purity, uniform, and dense films. | Less uniform and pure compared to CVD. |
Learn more about how CVD can benefit your applications—contact our experts today!