The primary difference between CVD (Chemical Vapor Deposition) and PCD (Physical Vapor Deposition) coatings lies in their deposition processes, resulting properties, and applications. CVD involves chemical reactions at high temperatures (800–1000°C) to deposit thicker, denser, and more uniform coatings, making it suitable for continuous cutting processes like turning. In contrast, PVD uses physical processes at lower temperatures (around 500°C) to create thinner, less dense coatings with compressive stress, ideal for interrupted cutting like milling. CVD coatings bond strongly with the substrate and are more resistant to abrasion, while PVD coatings offer faster application and versatility in material deposition.
Key Points Explained:
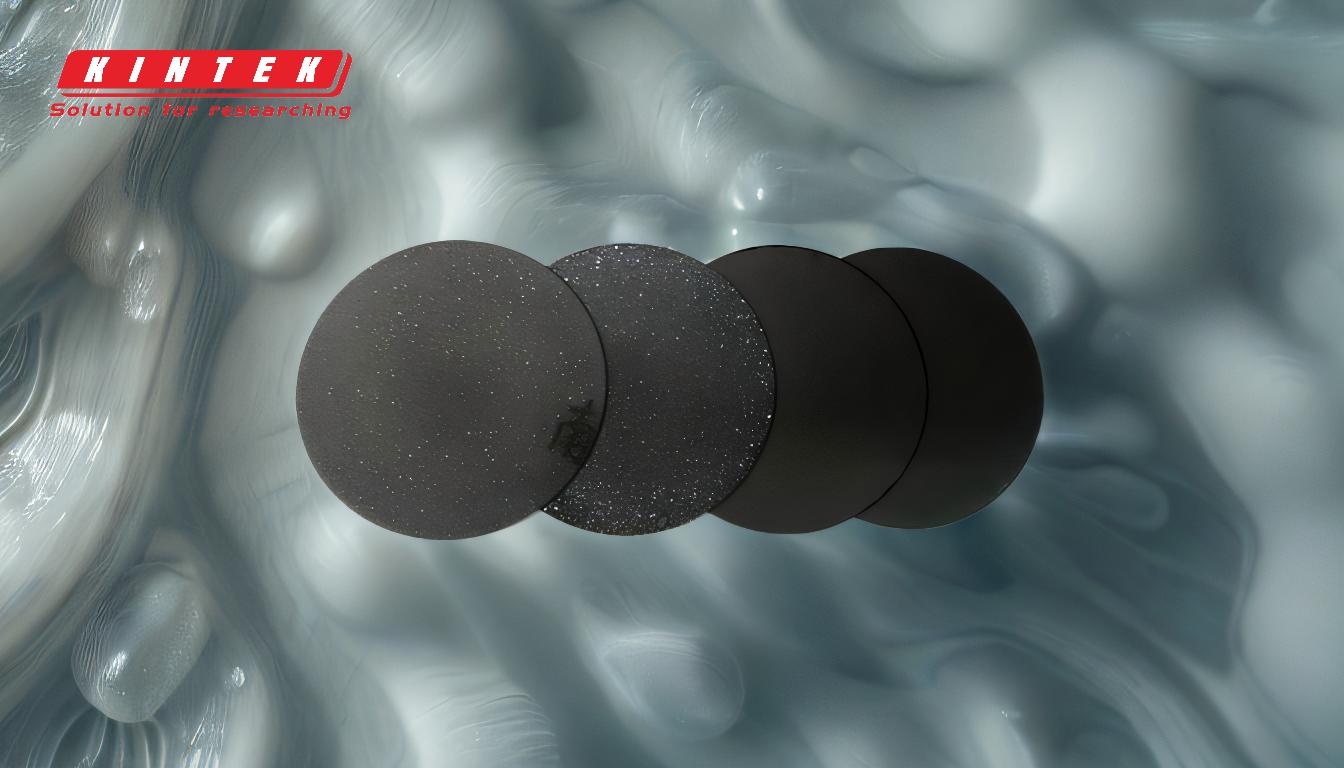
-
Deposition Process:
- CVD: Involves chemical reactions in a controlled environment using reactive gases at high temperatures (800–1000°C). The process deposits a thicker coating (10–20μm) and forms a diffusion-type bond with the substrate, resulting in a stronger adhesion.
- PVD: Uses physical processes, such as arc discharge, to evaporate a metal target in a vacuum at lower temperatures (around 500°C). This creates a thinner coating (3–5μm) with compressive stress during cooling.
-
Coating Properties:
- CVD: Produces denser, more uniform coatings with high abrasion and wear resistance. However, the high processing temperature can introduce residual tensile stress, making the coated equipment more fragile.
- PVD: Results in less dense and less uniform coatings but offers faster application times. The compressive stress in PVD coatings enhances their suitability for interrupted cutting processes.
-
Material Versatility:
- CVD: Typically limited to ceramics and polymers due to the chemical nature of the process.
- PVD: Can deposit a broader range of materials, including metals, alloys, and ceramics, offering greater flexibility in applications.
-
Applications:
- CVD: Best suited for continuous cutting processes (e.g., turning) and high-stress metal-forming applications where sliding friction and galling are concerns. Its ability to coat irregularly shaped surfaces also makes it versatile.
- PVD: Ideal for interrupted cutting processes (e.g., milling) due to its compressive stress and lower processing temperatures. It is also preferred for applications requiring a wider range of materials.
-
Bond Strength and Layer Structure:
- CVD: Forms a diffusion-type bond with the substrate, resulting in stronger adhesion and improved layer structure and thickness homogeneity.
- PVD: Creates a mechanical bond, which is generally weaker than the diffusion-type bond of CVD but sufficient for many applications.
-
Temperature Sensitivity:
- CVD: High processing temperatures limit its use with substrates that cannot withstand extreme heat.
- PVD: Lower processing temperatures make it suitable for temperature-sensitive materials and substrates.
-
Coating Uniformity and Density:
- CVD: Provides denser and more uniform coatings, enhancing durability and wear resistance.
- PVD: Coatings are less dense and less uniform but can be applied more quickly, making them cost-effective for certain applications.
-
Residual Stress:
- CVD: Residual tensile stress can make the coated equipment more fragile, despite its abrasion resistance.
- PVD: Compressive stress improves the coating's performance in interrupted cutting processes and reduces the risk of cracking.
By understanding these key differences, equipment and consumable purchasers can make informed decisions based on the specific requirements of their applications, such as cutting processes, material compatibility, and desired coating properties.
Summary Table:
Aspect | CVD (Chemical Vapor Deposition) | PVD (Physical Vapor Deposition) |
---|---|---|
Deposition Process | Chemical reactions at high temperatures (800–1000°C) | Physical processes at lower temperatures (around 500°C) |
Coating Thickness | Thicker (10–20μm) | Thinner (3–5μm) |
Coating Density | Denser and more uniform | Less dense and less uniform |
Bond Strength | Diffusion-type bond, stronger adhesion | Mechanical bond, weaker but sufficient |
Material Versatility | Limited to ceramics and polymers | Broader range (metals, alloys, ceramics) |
Applications | Continuous cutting (e.g., turning), high-stress metal-forming | Interrupted cutting (e.g., milling), temperature-sensitive materials |
Residual Stress | Tensile stress, may make equipment fragile | Compressive stress, improves performance in interrupted cutting |
Processing Time | Slower | Faster |
Need help choosing the right coating for your application? Contact our experts today for personalized guidance!