The primary difference between CVD (Chemical Vapor Deposition) and PVD (Physical Vapor Deposition) carbide lies in the deposition process, materials used, temperature requirements, and the resulting coating properties. CVD involves a chemical reaction between gaseous precursors and the substrate, resulting in a multidirectional deposition that can coat complex geometries. It operates at higher temperatures (450°C to 1050°C) and produces dense, uniform coatings. PVD, on the other hand, is a line-of-sight process where solid materials are vaporized and deposited onto the substrate. It operates at lower temperatures (250°C to 450°C) and is suitable for a broader range of materials, including metals, alloys, and ceramics. Each method has its advantages and limitations, making them suitable for different applications.
Key Points Explained:
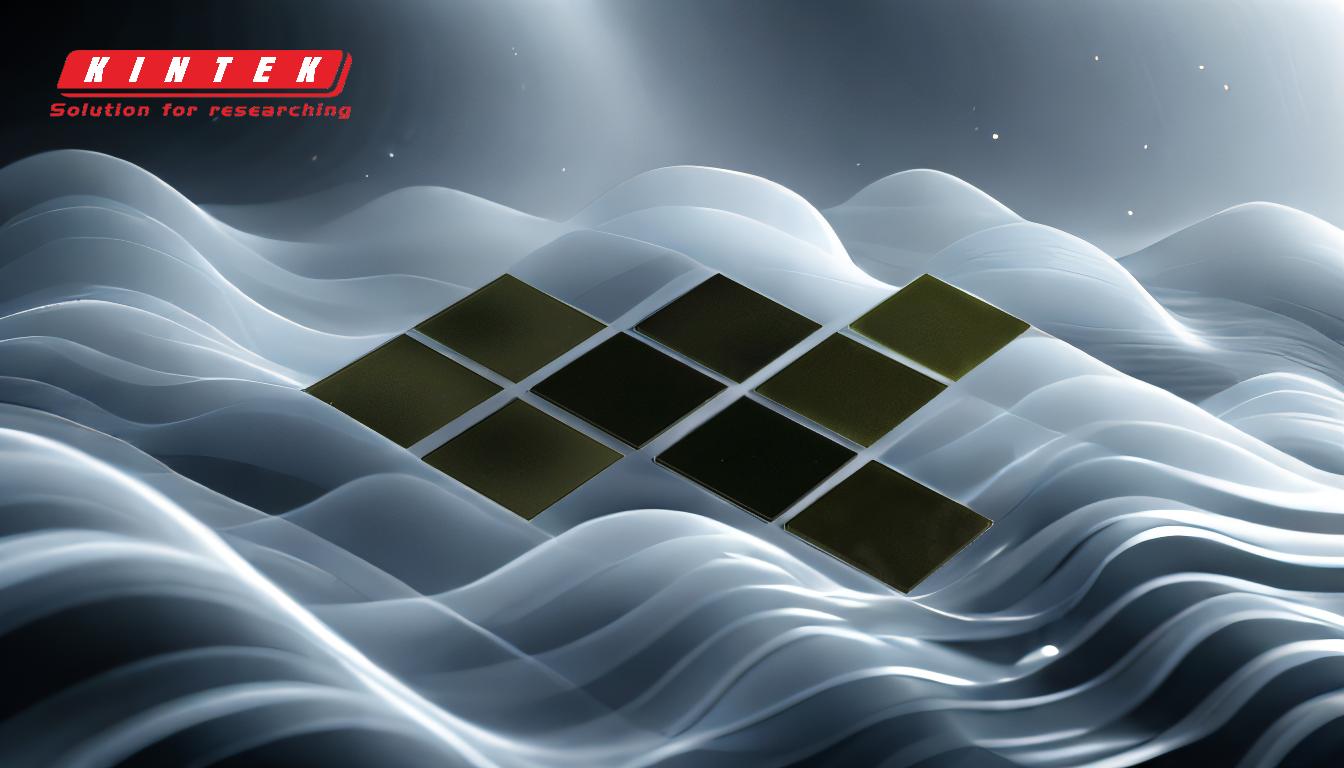
-
Deposition Process:
- CVD: Involves chemical reactions between gaseous precursors and the substrate. The process is multidirectional, allowing for uniform coating of complex shapes, including holes and deep recesses.
- PVD: A physical process where solid materials are vaporized and deposited onto the substrate. It is a line-of-sight process, meaning it only coats surfaces directly exposed to the vapor source.
-
Materials Used:
- CVD: Primarily uses gaseous precursors, limiting its application to ceramics and polymers.
- PVD: Can deposit a wider range of materials, including metals, alloys, and ceramics.
-
Temperature Requirements:
- CVD: Operates at higher temperatures, typically between 450°C and 1050°C. This high-temperature environment can lead to the formation of corrosive gaseous products and impurities in the film.
- PVD: Operates at lower temperatures, typically between 250°C and 450°C. This makes it suitable for substrates that cannot withstand high temperatures.
-
Coating Properties:
- CVD: Produces dense, uniform coatings with high throwing power, making it ideal for complex geometries. However, the process can leave impurities in the film.
- PVD: Coatings are less dense and less uniform compared to CVD but can be applied more quickly. PVD coatings are also more versatile in terms of material compatibility.
-
Deposition Rates and Efficiency:
- CVD: Offers high deposition rates and is often more economical for producing thick coatings. It does not typically require an ultra-high vacuum.
- PVD: Generally has lower deposition rates, although methods like EBPVD (Electron Beam Physical Vapor Deposition) can achieve high rates (0.1 to 100 μm/min) at relatively low substrate temperatures. PVD also has very high material utilization efficiency.
-
Applications:
- CVD: Suitable for applications requiring dense, uniform coatings on complex geometries, such as in the semiconductor and aerospace industries.
- PVD: Ideal for applications requiring a broader range of materials and lower temperature processing, such as in the tooling and decorative coatings industries.
In summary, the choice between CVD and PVD depends on the specific requirements of the application, including the desired coating properties, material compatibility, and temperature constraints. Each method has its unique advantages and limitations, making them complementary rather than competing technologies.
Summary Table:
Aspect | CVD (Chemical Vapor Deposition) | PVD (Physical Vapor Deposition) |
---|---|---|
Deposition Process | Chemical reaction between gaseous precursors and substrate; multidirectional coating. | Physical vaporization of solid materials; line-of-sight coating. |
Materials Used | Primarily ceramics and polymers. | Metals, alloys, and ceramics. |
Temperature Range | 450°C to 1050°C. | 250°C to 450°C. |
Coating Properties | Dense, uniform coatings with high throwing power; may contain impurities. | Less dense, less uniform coatings; versatile material compatibility. |
Deposition Rates | High deposition rates; economical for thick coatings. | Lower deposition rates; high material utilization efficiency. |
Applications | Ideal for complex geometries (e.g., semiconductors, aerospace). | Suitable for broader material range and lower temperature processing (e.g., tooling, decorative). |
Need help choosing between CVD and PVD carbide? Contact our experts today for tailored solutions!