CVD (Chemical Vapor Deposition) and PVD (Physical Vapor Deposition) are two widely used techniques for coating inserts, each with distinct processes, material capabilities, and resulting properties. CVD involves chemical reactions between gaseous precursors and the substrate, producing dense, uniform coatings at high temperatures, while PVD relies on physical vaporization of solid materials in a vacuum, depositing thinner, less dense coatings at lower temperatures. The choice between the two depends on factors such as material compatibility, coating thickness, temperature sensitivity, and application requirements. Below, we explore the key differences in detail.
Key Points Explained:
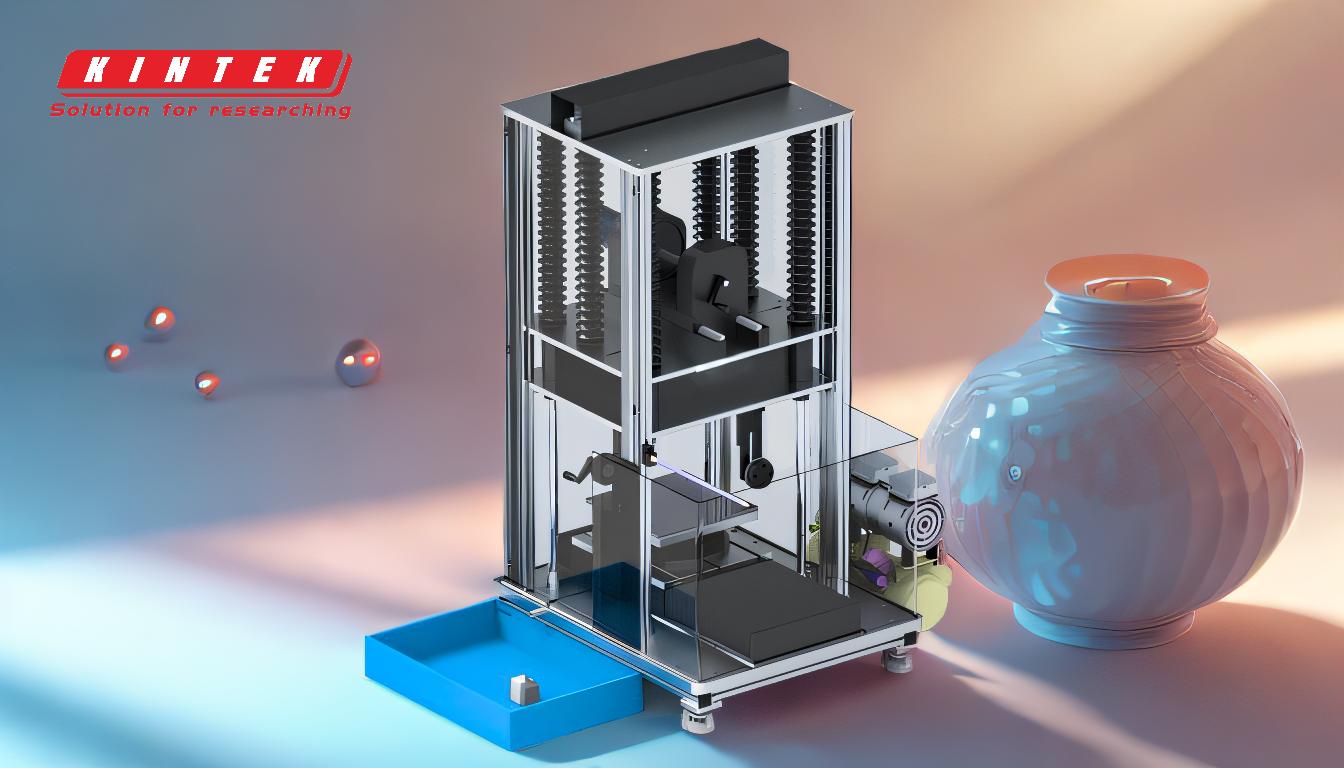
-
Deposition Process:
- CVD: In CVD, gaseous precursors undergo chemical reactions on the substrate surface, forming a solid coating. This process is multidirectional, allowing for uniform coverage even on complex geometries. The chemical reactions typically occur at high temperatures (450°C to 1050°C), which can limit the types of substrates that can be coated.
- PVD: PVD involves the physical vaporization of a solid target material, which is then deposited onto the substrate in a vacuum environment. This process is line-of-sight, meaning the coating is applied directly to surfaces facing the target. PVD operates at lower temperatures (250°C to 450°C), making it suitable for temperature-sensitive materials.
-
Material Compatibility:
- CVD: CVD is primarily used for depositing ceramics and polymers, as the high temperatures and chemical reactions favor these materials. It is less suitable for metals and alloys due to potential thermal and chemical incompatibilities.
- PVD: PVD can deposit a broader range of materials, including metals, alloys, and ceramics. This versatility makes it a preferred choice for applications requiring diverse material properties.
-
Coating Properties:
- CVD: CVD coatings are denser and more uniform due to the chemical bonding process. They are typically thicker (10~20μm) and provide excellent wear resistance and adhesion. However, the high processing temperatures can introduce tensile stress and fine cracks in the coating.
- PVD: PVD coatings are thinner (3~5μm) and less dense, but they exhibit compressive stress, which can enhance durability. The coatings are harder and more wear-resistant, though they may not be as uniform as CVD coatings.
-
Application Speed and Efficiency:
- CVD: CVD processes are generally slower due to the time required for chemical reactions and high-temperature processing. This can be a disadvantage in high-throughput manufacturing environments.
- PVD: PVD is faster to apply, making it more suitable for high-volume production. The lower processing temperatures also reduce energy consumption and minimize thermal damage to the substrate.
-
Temperature Sensitivity:
- CVD: The high temperatures required for CVD can limit its use with temperature-sensitive substrates, such as certain polymers or low-melting-point metals.
- PVD: PVD's lower processing temperatures make it ideal for coating temperature-sensitive materials without compromising their structural integrity.
-
Stress and Cracking:
- CVD: The high temperatures in CVD can lead to tensile stress and fine cracks in the coating, which may affect its long-term performance in demanding applications.
- PVD: PVD coatings develop compressive stress during cooling, which can improve their resistance to cracking and fatigue.
-
Applications:
- CVD: CVD is commonly used in applications requiring thick, durable coatings, such as cutting tools, wear-resistant components, and semiconductor devices.
- PVD: PVD is preferred for applications needing thin, hard coatings, such as decorative finishes, optical coatings, and precision tools.
In summary, the choice between CVD and PVD depends on the specific requirements of the application, including material compatibility, coating thickness, temperature sensitivity, and production efficiency. Both techniques offer unique advantages, making them indispensable in modern manufacturing and materials science.
Summary Table:
Aspect | CVD | PVD |
---|---|---|
Deposition Process | Chemical reactions at high temperatures (450°C–1050°C), multidirectional | Physical vaporization in a vacuum, line-of-sight, lower temperatures (250°C–450°C) |
Material Compatibility | Best for ceramics and polymers; limited for metals/alloys | Suitable for metals, alloys, and ceramics |
Coating Properties | Denser, thicker (10~20μm), uniform, tensile stress, fine cracks | Thinner (3~5μm), less dense, compressive stress, harder, wear-resistant |
Application Speed | Slower due to high-temperature processing | Faster, ideal for high-volume production |
Temperature Sensitivity | Limited for temperature-sensitive substrates | Suitable for temperature-sensitive materials |
Stress and Cracking | Tensile stress, fine cracks | Compressive stress, improved durability |
Applications | Cutting tools, wear-resistant components, semiconductor devices | Decorative finishes, optical coatings, precision tools |
Still unsure which coating technique is right for your needs? Contact our experts today for personalized guidance!