CVD (Chemical Vapor Deposition) and PVD (Physical Vapor Deposition) are two prominent methods for synthesizing nanomaterials, each with distinct processes, advantages, and limitations. CVD involves chemical reactions at lower temperatures, producing dense and uniform coatings, often used for ceramics and polymers. In contrast, PVD operates in a vacuum at high temperatures, utilizing physical processes to deposit a broader range of materials, including metals, alloys, and ceramics. While PVD coatings are less dense and less uniform, they are faster to apply. CVD coatings, though denser and more uniform, require longer application times. Understanding these differences is crucial for selecting the appropriate method based on the desired material properties and application requirements.
Key Points Explained:
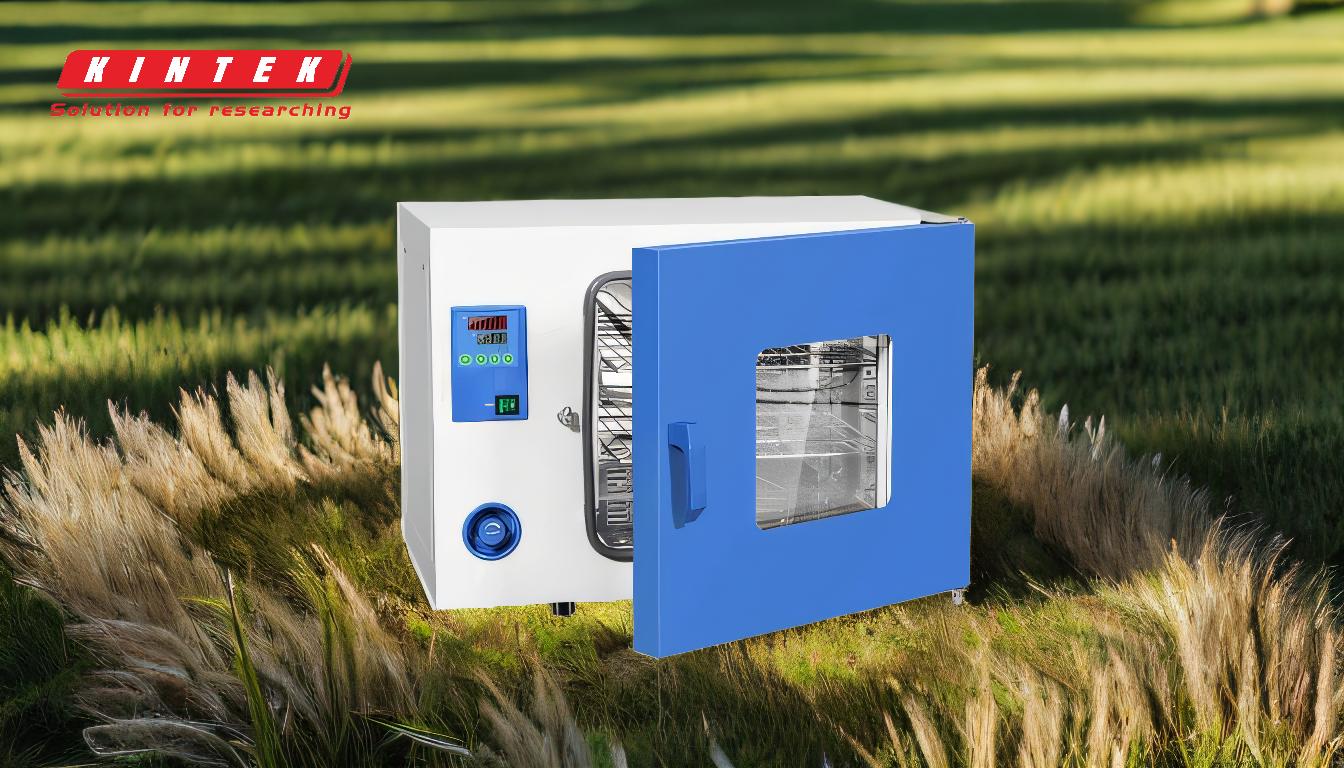
-
Material Range:
- PVD: Can deposit a wide variety of materials, including metals, alloys, and ceramics. This versatility makes PVD suitable for applications requiring diverse material properties.
- CVD: Primarily limited to ceramics and polymers. This limitation is due to the chemical reactions involved, which are more suited for these types of materials.
-
Process Environment:
- PVD: Operates in a vacuum at high temperatures. The physical processes involved, such as sputtering or evaporation, require these conditions to ensure proper material deposition.
- CVD: Utilizes chemical reactions at lower temperatures. The process involves introducing reactive gases into a chamber, where they react to form a solid material on the substrate.
-
Coating Characteristics:
- PVD: Produces coatings that are less dense and less uniform. This can be advantageous for applications where a specific texture or surface roughness is desired.
- CVD: Results in denser and more uniform coatings. This uniformity is beneficial for applications requiring precise thickness and consistency, such as in semiconductor manufacturing.
-
Application Speed:
- PVD: Faster to apply due to the physical nature of the process. This speed can be crucial in high-volume production environments where time is a critical factor.
- CVD: Takes longer to apply because of the chemical reactions involved. The slower process allows for more controlled and precise deposition, which is essential for high-quality coatings.
-
Applications:
- PVD: Commonly used in industries requiring durable and wear-resistant coatings, such as tool manufacturing and decorative finishes.
- CVD: Often employed in applications needing high-purity and high-performance materials, such as in the production of laboratory-grown diamonds and advanced electronic components.
Understanding these key differences between CVD and PVD methods is essential for selecting the appropriate technique based on the specific requirements of the nanomaterial synthesis and the intended application. Each method has its unique advantages and limitations, making them suitable for different industrial and scientific purposes.
Summary Table:
Aspect | CVD (Chemical Vapor Deposition) | PVD (Physical Vapor Deposition) |
---|---|---|
Material Range | Primarily ceramics and polymers | Metals, alloys, and ceramics |
Process Environment | Chemical reactions at lower temperatures | Operates in a vacuum at high temperatures |
Coating Characteristics | Denser and more uniform coatings | Less dense and less uniform coatings |
Application Speed | Slower due to chemical reactions | Faster due to physical processes |
Applications | High-purity materials, semiconductors, lab-grown diamonds | Durable coatings, tool manufacturing, decorative finishes |
Need help choosing the right synthesis method for your nanomaterials? Contact our experts today for personalized guidance!