The primary difference between fast pyrolysis and slow pyrolysis of biochar lies in their process conditions, reaction times, and product distributions. Slow pyrolysis is a longer process, taking several hours, and primarily produces biochar. In contrast, fast pyrolysis occurs in seconds, with higher heating rates, and yields a mix of bio-oil (60%), biochar (20%), and syngas (20%). Fast pyrolysis requires finely ground feed, controlled temperatures around 500°C, and rapid cooling of vapors, making it more energy-efficient for biofuel production. Slow pyrolysis, however, is better suited for maximizing biochar yield.
Key Points Explained:
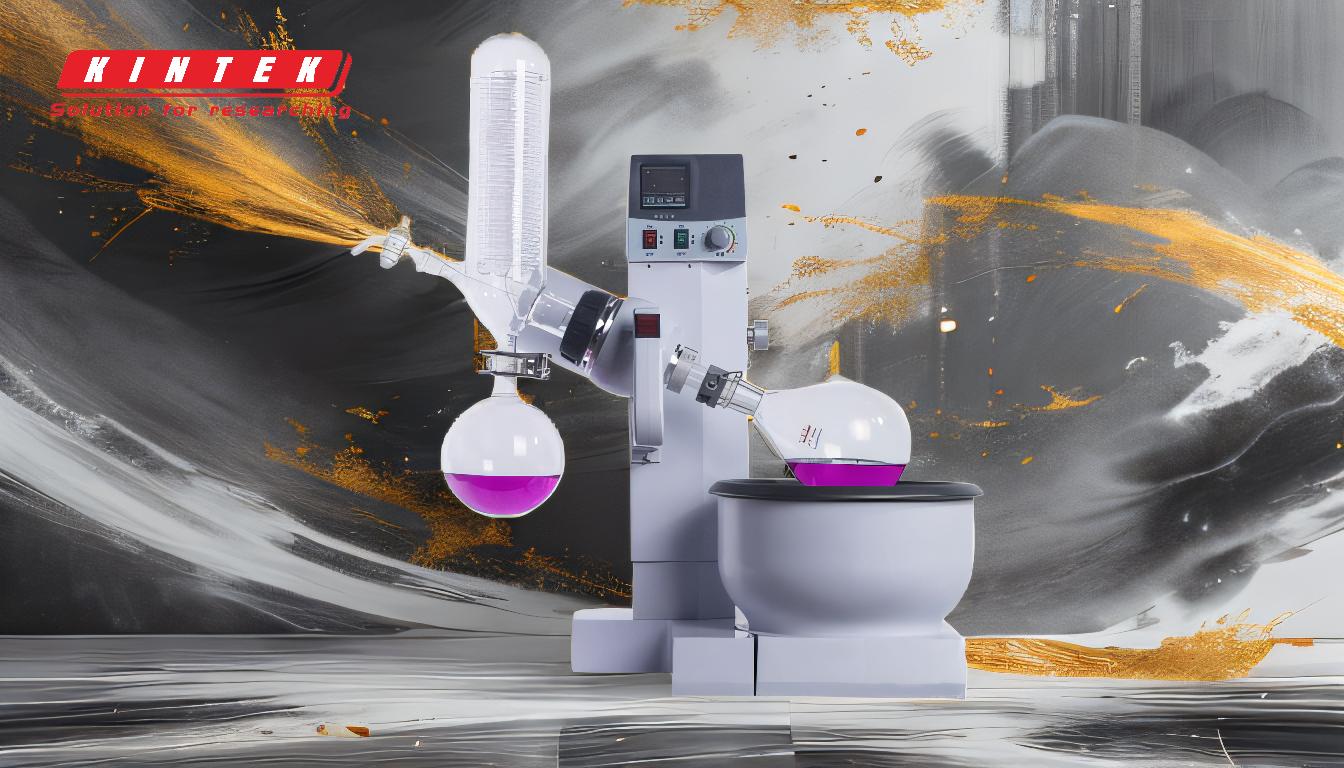
-
Reaction Time:
- Slow Pyrolysis: Takes several hours to complete, allowing for a more gradual breakdown of biomass into biochar.
- Fast Pyrolysis: Completes in seconds, requiring rapid heating and cooling to achieve the desired product mix.
-
Product Distribution:
- Slow Pyrolysis: Primarily produces biochar, with minimal yields of bio-oil and syngas. This makes it ideal for applications where biochar is the main goal, such as soil amendment or carbon sequestration.
- Fast Pyrolysis: Yields a higher proportion of bio-oil (60%) and syngas (20%), with biochar making up only 20% of the output. This is advantageous for biofuel production.
-
Heating Rates and Temperature Control:
- Slow Pyrolysis: Operates at lower heating rates, allowing for a more controlled and stable process. The slower reaction time ensures a higher yield of biochar.
- Fast Pyrolysis: Requires very high heating and heat transfer rates, with temperatures controlled around 500°C. The rapid heating and cooling are essential for maximizing bio-oil and syngas production.
-
Feed Preparation:
- Slow Pyrolysis: Can handle a broader range of feed sizes, as the slower process allows for more uniform heating.
- Fast Pyrolysis: Requires finely ground feed to ensure rapid and even heating, which is critical for the short reaction time.
-
Energy Efficiency:
- Slow Pyrolysis: Generally requires more energy input relative to the energy output, as the process is slower and less efficient in terms of biofuel production.
- Fast Pyrolysis: More energy-efficient, with less energy input relative to the energy output, making it a preferred method for biofuel production.
-
Applications:
- Slow Pyrolysis: Best suited for applications where biochar is the primary product, such as agricultural soil enhancement or carbon sequestration.
- Fast Pyrolysis: Ideal for applications requiring high yields of bio-oil and syngas, such as renewable energy production or chemical feedstock.
In summary, the choice between fast and slow pyrolysis depends on the desired end products. Slow pyrolysis is better for biochar production, while fast pyrolysis is more efficient for generating biofuels like bio-oil and syngas.
Summary Table:
Aspect | Slow Pyrolysis | Fast Pyrolysis |
---|---|---|
Reaction Time | Several hours | Seconds |
Product Distribution | Biochar (primary), minimal bio-oil & syngas | Bio-oil (60%), biochar (20%), syngas (20%) |
Heating Rates | Lower heating rates | High heating rates (~500°C) |
Feed Preparation | Broad range of feed sizes | Finely ground feed required |
Energy Efficiency | Less energy-efficient | More energy-efficient |
Applications | Biochar production (e.g., soil amendment) | Biofuel production (e.g., bio-oil, syngas) |
Need help choosing the right pyrolysis method for your needs? Contact our experts today!