Incineration and gasification are both thermal treatment processes used for waste management, but they differ significantly in their mechanisms, outputs, and environmental impacts. Incineration involves the complete combustion of waste materials in the presence of excess oxygen, resulting in the production of heat, ash, and flue gases. Gasification, on the other hand, is a partial oxidation process that occurs in a controlled environment with limited oxygen, converting carbonaceous materials into a synthetic gas (syngas) composed primarily of hydrogen, carbon monoxide, and carbon dioxide. The key differences lie in the chemical reactions, end products, and applications of each process.
Key Points Explained:
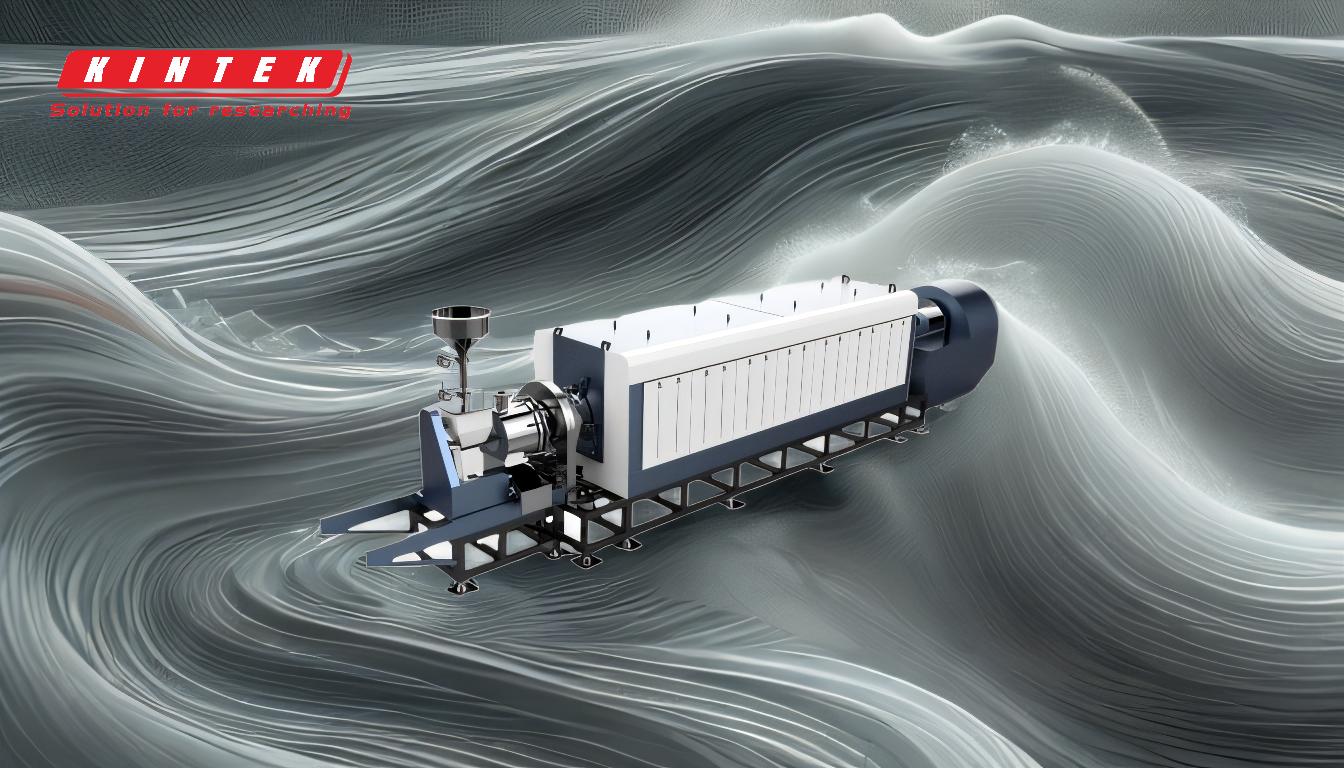
-
Chemical Process and Oxygen Supply:
- Incineration: This process involves the complete oxidation of waste materials in the presence of excess oxygen. The chemical reaction is exothermic, releasing a significant amount of heat energy. The primary goal is to reduce the volume of waste and generate energy in the form of heat.
- Gasification: Gasification is a partial oxidation process that occurs in a controlled environment with limited oxygen. The process is endothermic, requiring an external heat source to drive the reactions. The goal is to convert solid or liquid carbonaceous materials into a gaseous fuel (syngas) that can be used for energy production or chemical synthesis.
-
End Products:
- Incineration: The primary end products of incineration are heat, ash, and flue gases. The heat can be harnessed for electricity generation or district heating. The ash typically contains non-combustible materials and may require further treatment or disposal. Flue gases include carbon dioxide, water vapor, and potentially harmful pollutants like dioxins and furans, which must be treated before release into the atmosphere.
- Gasification: The main product of gasification is syngas, a mixture of hydrogen, carbon monoxide, and carbon dioxide. This syngas can be used as a fuel for power generation or as a feedstock for chemical production. The process also produces a small amount of solid residue, known as slag, which is typically inert and can be used in construction materials.
-
Environmental Impact:
- Incineration: While incineration reduces waste volume and generates energy, it can produce harmful emissions, including dioxins, furans, and heavy metals, if not properly controlled. Advanced incineration plants are equipped with pollution control technologies to minimize these emissions, but the process still contributes to greenhouse gas emissions, primarily carbon dioxide.
- Gasification: Gasification is generally considered more environmentally friendly than incineration. The process produces fewer pollutants and greenhouse gases, and the syngas can be cleaned and used more efficiently. Additionally, gasification can handle a wider variety of feedstocks, including biomass and municipal solid waste, making it a more versatile option for waste management.
-
Energy Efficiency:
- Incineration: The energy efficiency of incineration is relatively high, as the heat generated can be directly used for electricity production or heating. However, the overall efficiency depends on the quality of the waste and the technology used in the incineration plant.
- Gasification: Gasification can achieve higher energy efficiency compared to incineration, especially when the syngas is used in combined cycle power plants or for chemical synthesis. The syngas can also be stored and transported, providing flexibility in energy use.
-
Applications:
- Incineration: Incineration is widely used for municipal solid waste management, medical waste disposal, and hazardous waste treatment. It is particularly effective in urban areas where land for landfills is limited.
- Gasification: Gasification is used in a variety of applications, including power generation, chemical production, and biofuels. It is also being explored as a method for carbon capture and storage (CCS) to reduce greenhouse gas emissions.
-
Feedstock Flexibility:
- Incineration: Incineration is generally limited to combustible waste materials. Non-combustible materials, such as metals and glass, are not suitable for incineration and must be separated before processing.
- Gasification: Gasification can process a wider range of feedstocks, including biomass, coal, municipal solid waste, and even some types of hazardous waste. This flexibility makes gasification a more versatile option for waste management and energy production.
In summary, while both incineration and gasification are used for waste management and energy recovery, they differ in their chemical processes, end products, environmental impacts, and applications. Gasification offers several advantages, including higher energy efficiency, lower emissions, and greater feedstock flexibility, making it a promising technology for sustainable waste management and energy production.
Summary Table:
Aspect | Incineration | Gasification |
---|---|---|
Chemical Process | Complete oxidation with excess oxygen (exothermic). | Partial oxidation with limited oxygen (endothermic). |
End Products | Heat, ash, and flue gases (CO2, H2O, pollutants). | Syngas (H2, CO, CO2) and inert slag. |
Environmental Impact | Higher emissions (dioxins, furans, CO2); requires pollution control. | Fewer pollutants, lower greenhouse gas emissions, and cleaner syngas. |
Energy Efficiency | High for heat generation; efficiency depends on waste quality and technology. | Higher efficiency, especially with syngas in combined cycle power plants. |
Applications | Municipal, medical, and hazardous waste management. | Power generation, chemical production, biofuels, and carbon capture. |
Feedstock Flexibility | Limited to combustible waste; non-combustibles must be separated. | Handles biomass, coal, municipal waste, and some hazardous waste. |
Learn how gasification can revolutionize your waste management strategy—contact our experts today!