Induction furnaces and arc furnaces are both widely used in metal melting and refining, but they differ significantly in their working principles, applications, and capabilities. Induction furnaces use electromagnetic induction to generate heat, making them suitable for melting metals with low carbon content and producing high-quality alloys. They are more environmentally friendly and efficient, with advancements enabling the production of high-quality steels. Arc furnaces, on the other hand, rely on electric arcs to generate heat, making them better suited for large-scale steel production with higher metallurgical requirements. However, they produce more exhaust gases, waste residue, and noise. The choice between the two depends on the specific metallurgical requirements, scale of production, and environmental considerations.
Key Points Explained:
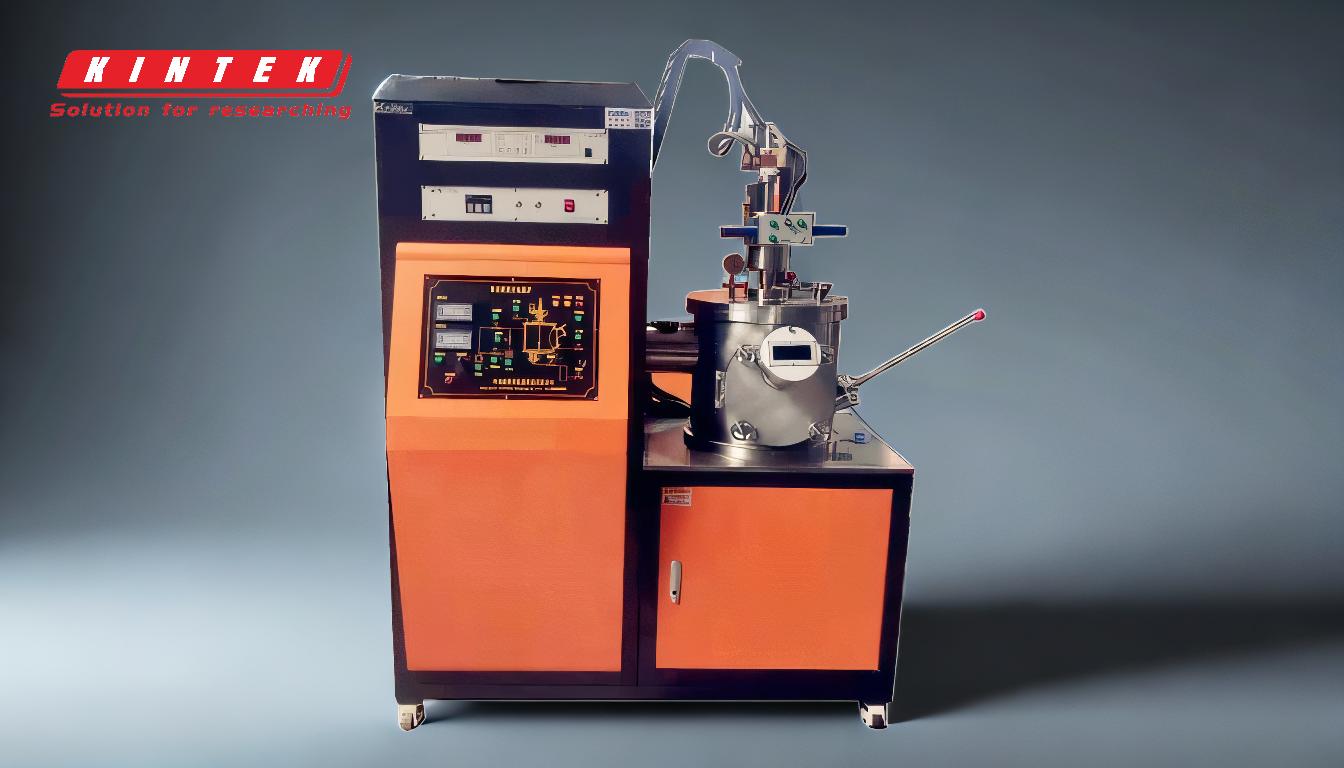
-
Working Principle:
- Induction Furnace: Uses electromagnetic induction to generate heat. A high-frequency alternating current passes through a coil, creating a magnetic field that induces eddy currents in the metal, heating it up. This method does not require direct contact between the heat source and the metal.
- Arc Furnace: Uses an electric arc to generate heat. An electric arc is struck between electrodes and the metal, producing intense heat. This method involves direct contact between the heat source (the arc) and the metal.
-
Metallurgical Capabilities:
- Induction Furnace: Historically, induction furnaces had limited metallurgical capabilities, but advancements since the 1980s have improved their ability to produce high-quality low-alloy steels, high-alloy steels, and even super low-carbon stainless steels and superalloys. They are particularly effective for melting metals with low carbon content and producing alloys under specific conditions (acidic, neutral, or near-vacuum environments).
- Arc Furnace: Generally has superior metallurgical capabilities compared to induction furnaces, making it suitable for refining steel grades with higher quality requirements. It is commonly used in large-scale steel production.
-
Applications:
- Induction Furnace: Typically used for refining steel grades with general metallurgical quality requirements, especially for small-sized steel castings. It is also used for producing high-quality alloys and melting non-magnetic materials like aluminum.
- Arc Furnace: Primarily used in large-scale steel production, where higher metallurgical quality and larger volumes are required. It is less suitable for small-scale or specialized alloy production.
-
Environmental Impact:
- Induction Furnace: More environmentally friendly, with lower emissions, waste residue, and noise. It also has higher energy efficiency, resulting in less burning loss and reduced metal melting time.
- Arc Furnace: Produces a large amount of exhaust gas, waste residue, and noise, and has higher energy consumption. It is less environmentally friendly compared to induction furnaces.
-
Efficiency and Thermal Performance:
- Induction Furnace: More efficient than traditional open-hearth furnaces. It uses high-voltage coils to produce frequencies between 50 Hz and 10,000 Hz, allowing for rapid heating and higher thermal efficiency. This results in better yields with less burning loss and superior steel production.
- Arc Furnace: While effective for large-scale production, it is less efficient in terms of energy use and thermal performance compared to induction furnaces.
-
Material Suitability:
- Induction Furnace: Suitable for melting metals with low carbon content and producing high-quality alloys. It is particularly effective for non-magnetic materials like aluminum, where careful design of the magnetic field is required.
- Arc Furnace: Suitable for a wide range of metals but is particularly effective for large-scale steel production where higher metallurgical quality is required.
-
Technological Advancements:
- Induction Furnace: Significant advancements in equipment and refractories since the 1980s have improved its metallurgical capabilities, allowing for the production of high-quality steels and alloys.
- Arc Furnace: Continues to be the preferred choice for large-scale steel production, with ongoing improvements in efficiency and environmental impact.
In summary, the choice between an induction furnace and an arc furnace depends on the specific requirements of the metallurgical process, including the scale of production, the type of metal being melted, and environmental considerations. Induction furnaces are more suitable for small-scale, high-quality alloy production with lower environmental impact, while arc furnaces are better for large-scale steel production with higher metallurgical requirements.
Summary Table:
Aspect | Induction Furnace | Arc Furnace |
---|---|---|
Working Principle | Uses electromagnetic induction; no direct contact with metal. | Uses electric arcs; direct contact with metal. |
Metallurgical Capabilities | Produces high-quality alloys, low-carbon steels, and superalloys. | Superior for refining high-quality steel grades. |
Applications | Small-scale, high-quality alloy production; melting non-magnetic materials like aluminum. | Large-scale steel production; higher metallurgical requirements. |
Environmental Impact | Lower emissions, waste, and noise; higher energy efficiency. | Higher emissions, waste, and noise; less environmentally friendly. |
Efficiency | Rapid heating, higher thermal efficiency, less burning loss. | Less efficient in energy use and thermal performance. |
Material Suitability | Best for low-carbon metals and non-magnetic materials. | Suitable for a wide range of metals, especially large-scale steel production. |
Technological Advancements | Improved metallurgical capabilities since the 1980s. | Ongoing improvements in efficiency and environmental impact. |
Still unsure which furnace is right for your needs? Contact our experts today for personalized advice!