Induction furnaces and electric arc furnaces are both widely used in metallurgical processes, but they differ significantly in their heating mechanisms, efficiency, and applications. Induction furnaces heat materials directly through electromagnetic induction, resulting in faster heating and higher thermal efficiency. Electric arc furnaces, on the other hand, rely on an electric arc to generate heat, which is then transferred to the material indirectly, leading to lower efficiency. Induction furnaces are typically used for refining steel with general quality requirements, while electric arc furnaces are better suited for high-quality steel production. Both types of furnaces have unique components and control systems that optimize their performance and reliability.
Key Points Explained:
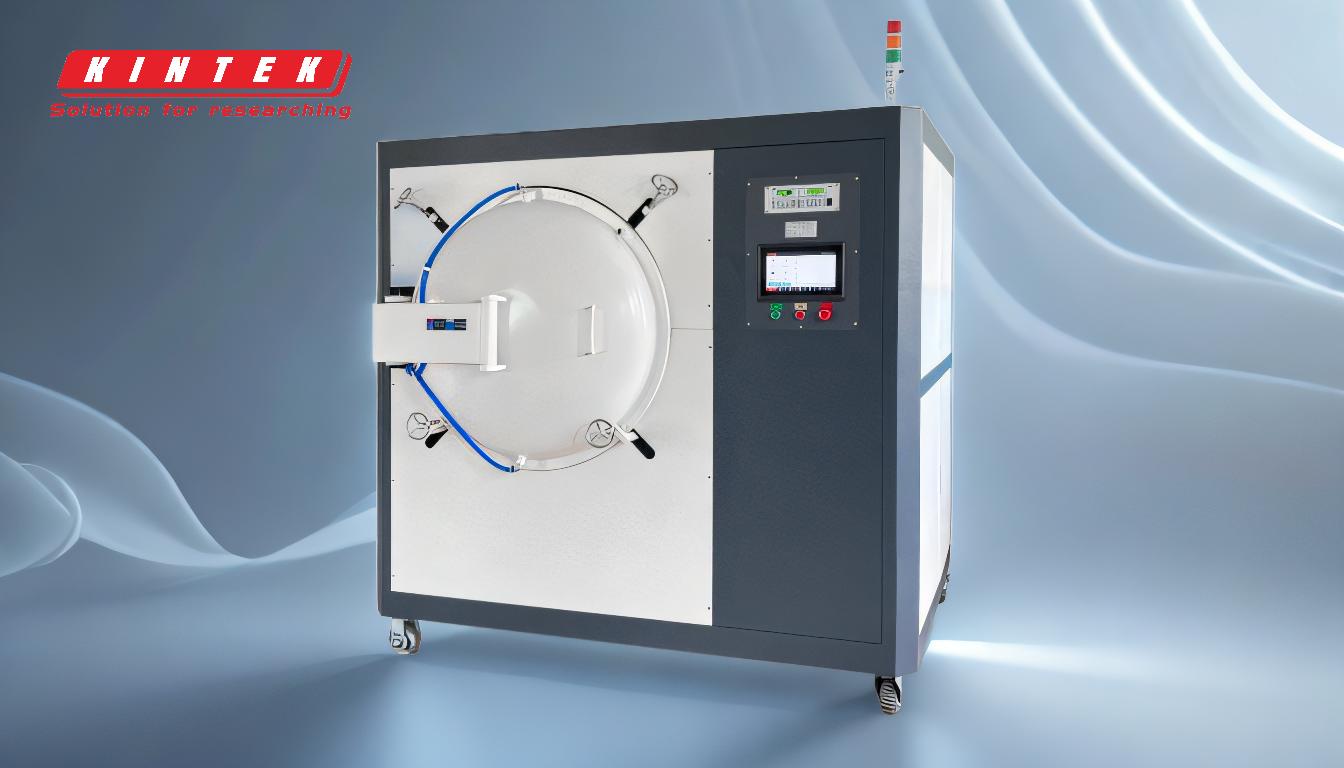
-
Heating Mechanism:
- Induction Furnace: Utilizes electromagnetic induction to generate eddy currents within the material, directly heating it. This method ensures uniform heating and melting, making it highly efficient.
- Electric Arc Furnace: Uses an electric arc to produce heat, which is then transferred to the material through slag. This indirect heating method results in lower thermal efficiency due to heat loss through the furnace cover and walls.
-
Thermal Efficiency:
- Induction Furnace: Higher thermal efficiency due to direct heating of the material. The heat is generated within the material itself, minimizing energy loss.
- Electric Arc Furnace: Lower thermal efficiency because the heat must travel through slag and other materials before reaching the molten steel, leading to significant energy loss.
-
Metallurgical Function:
- Induction Furnace: Generally used for refining steel with standard quality requirements and producing small-sized steel castings. Recent advancements have improved their metallurgical capabilities, allowing for the production of high-quality low-alloy steels, high-alloy steels, and even super low carbon stainless steel and superalloys.
- Electric Arc Furnace: Better suited for high-quality steel production due to its ability to handle more complex metallurgical processes and larger-scale operations.
-
Key Components:
- Induction Furnace: Includes an inductor, furnace body, power supply, capacitor, and control system. The igbt induction furnace is a notable example, featuring advanced control systems for stable performance and ease of maintenance.
- Electric Arc Furnace: Comprises components like AC contactors, silicon-controlled rectifiers, and inverter boards, which are optimized for large-scale integrated circuits and comprehensive protection systems.
-
Applications:
- Induction Furnace: Ideal for small to medium-sized operations requiring uniform heating and melting. Commonly used in foundries and for producing specialized alloys.
- Electric Arc Furnace: Suitable for large-scale steel production, especially in industries requiring high-quality steel with specific metallurgical properties.
-
Control Systems:
- Induction Furnace: Features advanced control systems with automatic frequency scanning, repeated starting functions, and constant power circuit control. These systems ensure smooth operation and high reliability.
- Electric Arc Furnace: Equipped with comprehensive protection systems for over-voltage, over-current, and under-voltage conditions, ensuring safe and reliable operation.
In summary, the choice between an induction furnace and an electric arc furnace depends on the specific requirements of the metallurgical process, including the desired quality of the steel, the scale of production, and the need for efficiency and uniformity in heating.
Summary Table:
Aspect | Induction Furnace | Electric Arc Furnace |
---|---|---|
Heating Mechanism | Direct heating via electromagnetic induction | Indirect heating via electric arc through slag |
Thermal Efficiency | Higher efficiency due to direct heating | Lower efficiency due to heat loss through furnace cover and walls |
Metallurgical Function | Used for refining steel with general quality requirements; capable of producing high-quality alloys | Better suited for high-quality steel production and complex metallurgical processes |
Key Components | Inductor, furnace body, power supply, capacitor, control system | AC contactors, silicon-controlled rectifiers, inverter boards |
Applications | Small to medium-sized operations; foundries and specialized alloys | Large-scale steel production; industries requiring high-quality steel |
Control Systems | Advanced systems with automatic frequency scanning and constant power control | Comprehensive protection systems for over-voltage, over-current, and under-voltage |
Need help choosing the right furnace for your metallurgical process? Contact our experts today!