Metallic and non-metallic coatings differ primarily in their composition, properties, and applications. Metallic coatings are typically made from metals or metal alloys and are used to enhance properties like corrosion resistance, wear resistance, and conductivity. Non-metallic coatings, on the other hand, are made from organic or inorganic materials such as polymers, ceramics, or composites and are used for insulation, aesthetic purposes, or protection against environmental factors. The choice between the two depends on the specific requirements of the application, such as durability, cost, and environmental conditions.
Key Points Explained:
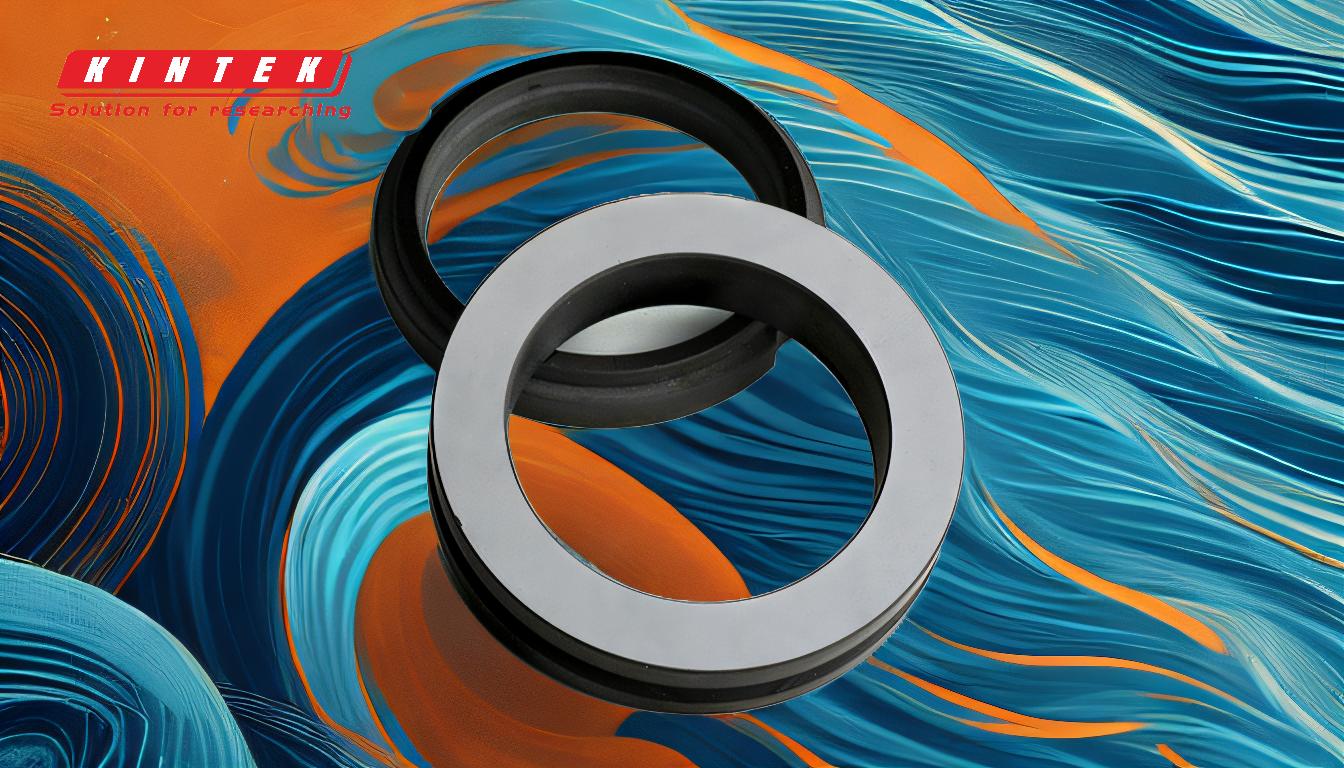
-
Composition:
- Metallic Coatings: These are made from metals or metal alloys such as zinc, aluminum, nickel, or chromium. They are often applied through processes like electroplating, galvanizing, or thermal spraying.
- Non-Metallic Coatings: These are composed of organic or inorganic materials like polymers, ceramics, or composites. Common examples include epoxy, polyurethane, and ceramic coatings.
-
Properties:
-
Metallic Coatings:
- Corrosion Resistance: Metals like zinc and aluminum provide excellent protection against corrosion, especially in harsh environments.
- Conductivity: Metallic coatings are often used in electrical applications due to their good electrical conductivity.
- Wear Resistance: These coatings can enhance the wear resistance of surfaces, making them suitable for high-stress applications.
-
Non-Metallic Coatings:
- Insulation: Non-metallic coatings are often used for electrical insulation, preventing the flow of electricity.
- Aesthetic Appeal: These coatings can be applied in various colors and finishes, making them ideal for decorative purposes.
- Chemical Resistance: Many non-metallic coatings offer excellent resistance to chemicals, making them suitable for use in chemical processing industries.
-
Metallic Coatings:
-
Application Methods:
- Metallic Coatings: Common application methods include electroplating, galvanizing, and thermal spraying. These methods ensure a strong bond between the coating and the substrate.
- Non-Metallic Coatings: These are typically applied through spraying, brushing, or dipping. Some coatings may require curing or baking to achieve their final properties.
-
Cost and Durability:
- Metallic Coatings: Generally more expensive due to the cost of raw materials and application processes. However, they offer long-lasting protection, especially in corrosive environments.
- Non-Metallic Coatings: Often more cost-effective and easier to apply. While they may not last as long as metallic coatings in some environments, they offer excellent performance in specific applications like insulation and chemical resistance.
-
Environmental Considerations:
- Metallic Coatings: Some metallic coatings, especially those involving heavy metals, can have environmental and health impacts. Proper disposal and handling are essential.
- Non-Metallic Coatings: Generally considered more environmentally friendly, especially those based on water-based or low-VOC (volatile organic compounds) formulations.
-
Applications:
- Metallic Coatings: Widely used in industries like automotive, aerospace, and construction for corrosion protection, wear resistance, and conductivity.
- Non-Metallic Coatings: Commonly used in electronics, construction, and consumer goods for insulation, aesthetic purposes, and protection against environmental factors.
In summary, the choice between metallic and non-metallic coatings depends on the specific requirements of the application, including factors like durability, cost, and environmental conditions. Understanding the differences in composition, properties, and application methods can help in selecting the right coating for a particular use case.
Summary Table:
Aspect | Metallic Coatings | Non-Metallic Coatings |
---|---|---|
Composition | Metals or metal alloys (e.g., zinc, aluminum, nickel, chromium) | Organic or inorganic materials (e.g., polymers, ceramics, composites) |
Properties | Corrosion resistance, conductivity, wear resistance | Insulation, aesthetic appeal, chemical resistance |
Application Methods | Electroplating, galvanizing, thermal spraying | Spraying, brushing, dipping, curing/baking |
Cost & Durability | More expensive, long-lasting in corrosive environments | Cost-effective, excellent performance in specific applications |
Environmental Impact | Potential environmental and health impacts (e.g., heavy metals) | Generally more environmentally friendly (e.g., water-based, low-VOC formulations) |
Applications | Automotive, aerospace, construction (corrosion protection, wear resistance) | Electronics, construction, consumer goods (insulation, aesthetics, environmental protection) |
Need help selecting the right coating for your project? Contact our experts today for personalized advice!