CVD (Chemical Vapor Deposition) is a widely used method for creating high-quality thin films, but it has limitations such as high costs, complexity, and restrictions on substrate size. PECVD (Plasma-Enhanced Chemical Vapor Deposition) and HDPCVD (High-Density Plasma Chemical Vapor Deposition) are advanced variants of CVD that address some of these limitations. PECVD uses plasma to enhance the chemical reactions, allowing for lower processing temperatures and faster deposition rates. HDPCVD, on the other hand, employs a high-density plasma to achieve even greater control over film properties, such as uniformity and step coverage, making it ideal for advanced semiconductor applications.
Key Points Explained:
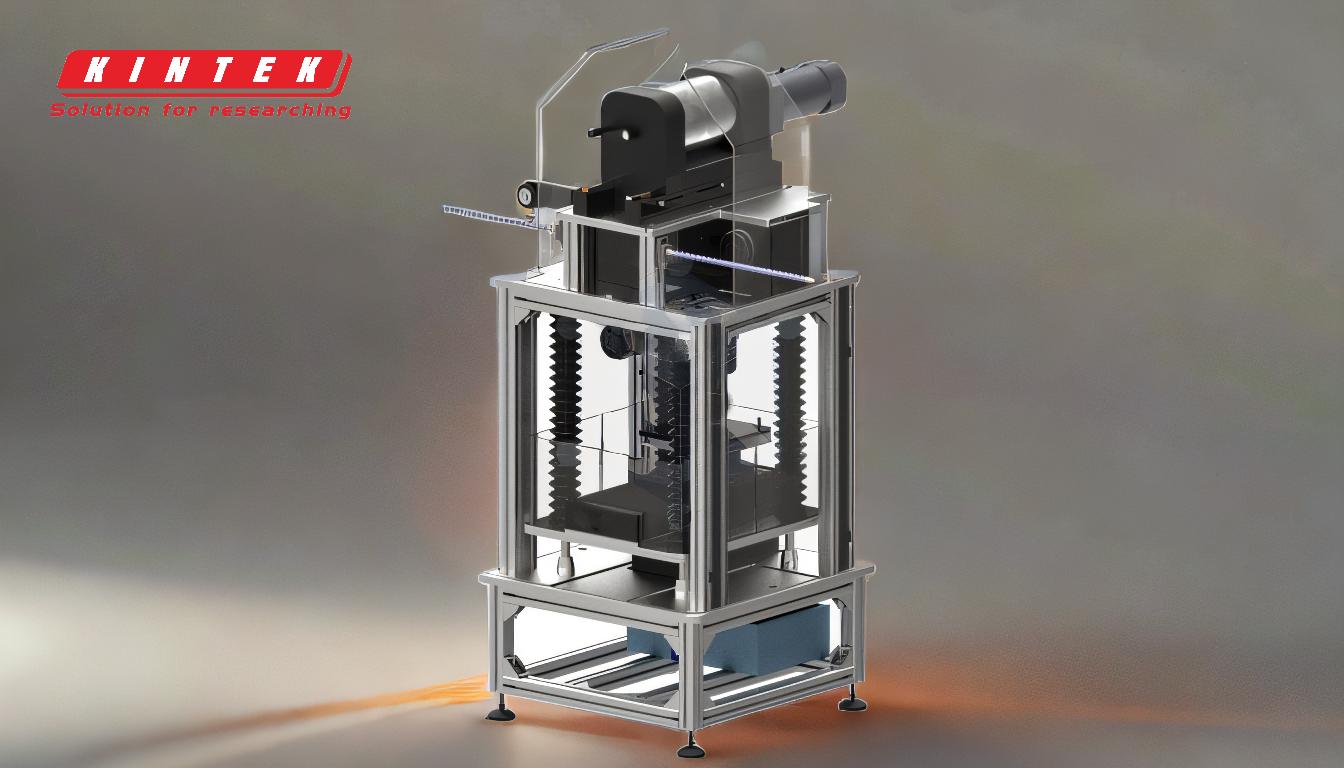
-
Basic Principles of CVD:
- CVD is a chemical process where volatile precursors react on a substrate to form a thin film.
- It is known for producing high-purity and dense films, suitable for coating irregular surfaces.
- However, CVD has drawbacks such as high costs, limited substrate size, and complexity in controlling process parameters.
-
Introduction to PECVD:
- PECVD (Plasma-Enhanced Chemical Vapor Deposition) introduces plasma to the CVD process.
- Plasma provides energy to the gas phase, enabling chemical reactions at lower temperatures compared to traditional CVD.
- This makes PECVD suitable for temperature-sensitive substrates and allows for faster deposition rates.
-
Introduction to HDPCVD:
- HDPCVD (High-Density Plasma Chemical Vapor Deposition) uses a high-density plasma to further enhance the CVD process.
- The high-density plasma increases the ionization of gas molecules, improving the uniformity and step coverage of the deposited films.
- HDPCVD is particularly useful in semiconductor manufacturing, where precise control over film properties is critical.
-
Key Differences Between PECVD and HDPCVD:
- Plasma Density: PECVD uses a lower-density plasma, while HDPCVD employs a high-density plasma, leading to better control over film properties.
- Temperature Requirements: PECVD operates at lower temperatures compared to traditional CVD, but HDPCVD can achieve even lower temperatures due to the high-density plasma.
- Application Scope: PECVD is widely used in industries like solar cells and displays, whereas HDPCVD is more specialized, primarily used in advanced semiconductor fabrication.
- Film Quality: HDPCVD generally produces films with superior uniformity and step coverage, making it ideal for complex geometries and high-aspect-ratio structures.
-
Advantages of PECVD and HDPCVD Over Traditional CVD:
- Lower Processing Temperatures: Both PECVD and HDPCVD allow for deposition at lower temperatures, reducing thermal stress on substrates.
- Faster Deposition Rates: The use of plasma accelerates the chemical reactions, leading to quicker film formation.
- Improved Film Quality: Enhanced control over plasma parameters results in films with better uniformity, density, and adhesion.
-
Challenges and Considerations:
- Complexity: Both PECVD and HDPCVD require sophisticated equipment and precise control over plasma parameters.
- Cost: The advanced equipment and energy requirements for plasma generation can increase production costs.
- Health and Safety: The use of plasma and hazardous gases necessitates strict safety protocols.
In summary, while both PECVD and HDPCVD are advanced forms of CVD that address some of the limitations of traditional CVD, they differ in terms of plasma density, temperature requirements, and application scope. PECVD is more versatile and widely used, while HDPCVD offers superior film quality and is ideal for specialized applications in semiconductor manufacturing. Understanding these differences is crucial for selecting the appropriate technique based on the specific requirements of the application.
Summary Table:
Aspect | PECVD | HDPCVD |
---|---|---|
Plasma Density | Lower-density plasma | High-density plasma |
Temperature | Lower than traditional CVD | Even lower temperatures due to high-density plasma |
Application Scope | Solar cells, displays | Advanced semiconductor fabrication |
Film Quality | Good uniformity and step coverage | Superior uniformity and step coverage for complex geometries |
Need help choosing the right thin film deposition technique? Contact our experts today!