Physical Vapor Deposition (PVD) and Chemical Vapor Deposition (CVD) are two distinct thin-film deposition techniques used in various industries. While both methods aim to deposit thin films onto substrates, they differ significantly in their mechanisms, processes, and outcomes. PVD relies on physical processes such as evaporation or sputtering to vaporize and deposit materials, typically at lower temperatures and without chemical reactions. In contrast, CVD involves chemical reactions between gaseous precursors and the substrate, often requiring higher temperatures and producing more complex films. The choice between PVD and CVD depends on factors such as deposition rate, substrate temperature, film quality, and application requirements.
Key Points Explained:
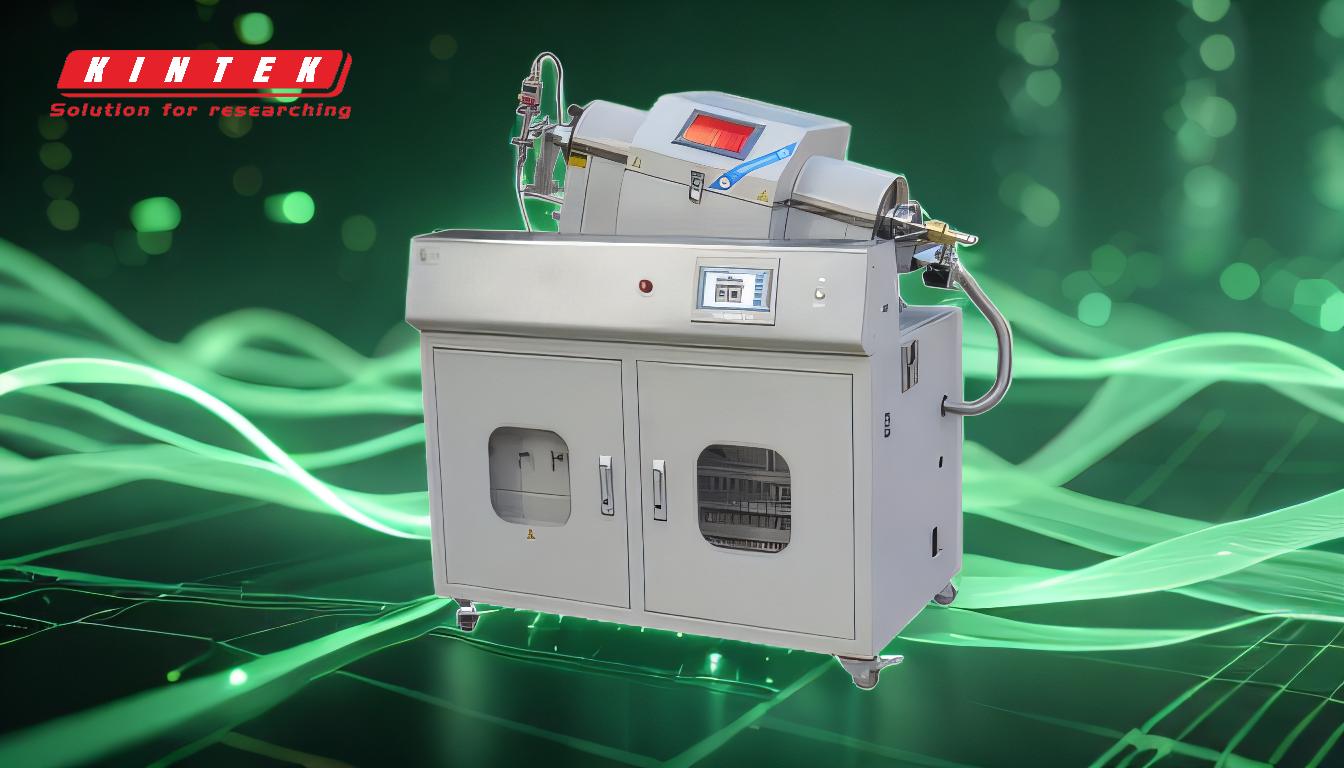
-
Deposition Mechanism:
- PVD: In PVD, the material to be deposited is physically vaporized through processes like evaporation or sputtering. The vaporized atoms or molecules then condense onto the substrate, forming a thin film. This process does not involve chemical reactions.
- CVD: CVD relies on chemical reactions between gaseous precursors and the substrate. The gaseous molecules react on the substrate surface, forming a solid film. This method often requires higher temperatures to facilitate the chemical reactions.
-
Temperature Requirements:
- PVD: PVD processes typically occur at lower temperatures, usually between 250°C to 450°C. This makes PVD suitable for substrates that cannot withstand high temperatures.
- CVD: CVD processes generally require higher temperatures, ranging from 450°C to 1050°C. These elevated temperatures are necessary to activate the chemical reactions involved in film formation.
-
Deposition Rate:
- PVD: PVD generally has lower deposition rates compared to CVD. However, specific PVD techniques like Electron Beam Physical Vapor Deposition (EBPVD) can achieve high deposition rates, ranging from 0.1 to 100 μm/min.
- CVD: CVD typically offers higher deposition rates, making it more efficient for certain applications, especially those requiring thick films.
-
Film Quality and Characteristics:
- PVD: PVD films often exhibit better surface smoothness and adhesion. The lack of chemical reactions in PVD can result in purer films with fewer impurities.
- CVD: CVD films tend to have better density and coverage, especially on complex geometries. The chemical reactions in CVD can produce films with excellent conformality and uniformity.
-
Material Utilization Efficiency:
- PVD: PVD processes, particularly EBPVD, are known for their high material utilization efficiency. This means that a significant portion of the vaporized material is deposited onto the substrate, reducing waste.
- CVD: CVD processes may have lower material utilization efficiency due to the involvement of gaseous precursors and chemical reactions, which can lead to the formation of by-products and impurities.
-
Applications:
- PVD: PVD is commonly used in applications requiring high-purity films, such as optical coatings, decorative coatings, and certain electronic applications. It is also preferred for high-volume production due to its ability to deposit films onto large substrate areas efficiently.
- CVD: CVD is widely used in the semiconductor industry for creating organic and inorganic films on metals, semiconductors, and other materials. It is also employed in the production of coatings for wear resistance, corrosion protection, and thermal barrier applications.
-
Environmental and Safety Considerations:
- PVD: PVD processes generally produce fewer corrosive by-products and are considered safer and more environmentally friendly compared to CVD.
- CVD: CVD processes can produce corrosive gaseous by-products and may require more stringent safety measures and waste management practices.
In summary, while both PVD and CVD are valuable techniques for thin-film deposition, they differ in their mechanisms, temperature requirements, deposition rates, film characteristics, and applications. The choice between PVD and CVD depends on the specific requirements of the application, including the desired film properties, substrate compatibility, and production efficiency.
Summary Table:
Aspect | PVD | CVD |
---|---|---|
Deposition Mechanism | Physical processes (evaporation/sputtering) without chemical reactions. | Chemical reactions between gaseous precursors and the substrate. |
Temperature | Lower (250°C to 450°C). | Higher (450°C to 1050°C). |
Deposition Rate | Lower, but EBPVD can achieve 0.1 to 100 μm/min. | Higher, ideal for thick films. |
Film Quality | Better surface smoothness and adhesion; fewer impurities. | Better density, coverage, and conformality on complex geometries. |
Material Efficiency | High material utilization efficiency. | Lower due to by-products and impurities. |
Applications | Optical coatings, decorative coatings, high-volume production. | Semiconductor films, wear resistance, corrosion protection coatings. |
Environmental Impact | Fewer corrosive by-products; safer and more eco-friendly. | Produces corrosive by-products; requires stringent safety measures. |
Need help choosing the right thin-film deposition technique? Contact our experts today!